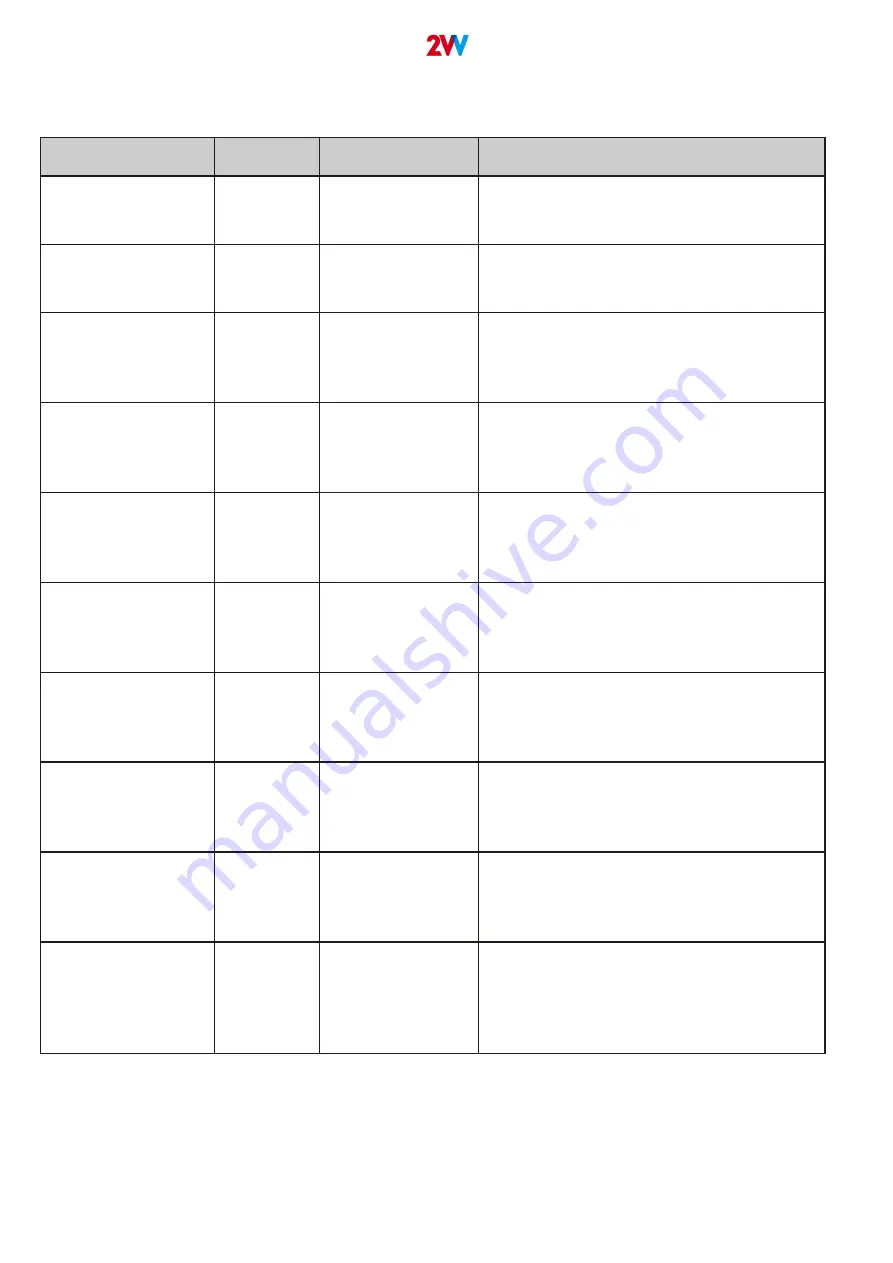
28
29
2VV.
Creating innovative solutions for you and your business since 1995.
ver.5 5-05-20
9. REMOVING FAULTS
Description
Unit's be-
haviour
Likely problem
Solution
12 – CO2 sensor failure
Unit is ven-
tilating
Defective air quality
sensor
Check that the CO2 sensor is connected co-
rrectly or check that it is operating correctly
(output signal value)
14 - ADB module
error
Unit is ven-
tilating
Failure of adiabatic
module
Check that the input error is correctly conne-
cted to the electronics or, if necessary, that the
adiabatic module is operating correctly
15 - Heat pump error Unit is ven-
tilating
Heat pump failure
Check that the input error is correctly conne-
cted to the electronics or, if necessary, that the
heat pump is operating correctly (according to
the instructions of its manufacturer)
16 – Inlet – External
temperature sensor
failure (T-EXT1)
Unit is not
working
Room temperature
sensor failure
Check that the sensor is correctly connected
to the electronics or test it measuring its resi-
stance (the resistance value at +20°C is around
10kW)
17 – Inlet – Failure
of the temperature
sensor behind the
exchanger (T-EXT2)
Unit is not
working
Room temperature
sensor failure
Check that the sensor is correctly connected
to the electronics or test it measuring its resi-
stance (the resistance value at +20°C is around
10kW)
18 – Inlet – Tempe-
rature sensor failure
in the supply canal
(T-EXT3)
Unit is not
working
Room temperature
sensor failure
Check that the sensor is correctly connected
to the electronics or test it measuring its resi-
stance (the resistance value at +20°C is around
10kW)
19 - Inlet - Tempe-
rature sensor failure
after the second ex-
changer (T-EXT4)
Unit is not
working
Room temperature
sensor failure
Check that the sensor is correctly connected
to the electronics or test it measuring its resi-
stance (the resistance value at +20°C is around
10kW)
20 - Exhaust – Tem-
perature sensor failure
in the exhaust canal
(T-INT0)
Unit is not
working
Room temperature
sensor failure
Check that the sensor is correctly connected
to the electronics or test it measuring its resi-
stance (the resistance value at +20°C is around
10kW)
21 – Exhaust – Tem-
perature sensor failure
in the exhaust canal
(T-INT1)
Unit is not
working
Room temperature
sensor failure
Check that the sensor is correctly connected
to the electronics or test it measuring its resi-
stance (the resistance value at +20°C is around
10kW)
22 – Exhaust – Failure
of the temperature
sensor of the exchan-
ger's anti-freeze pro-
tection (T-INT2)
Unit is not
working
Room temperature
sensor failure
Check that the sensor is correctly connected
to the electronics or test it measuring its resi-
stance (the resistance value at +20°C is around
10kW)