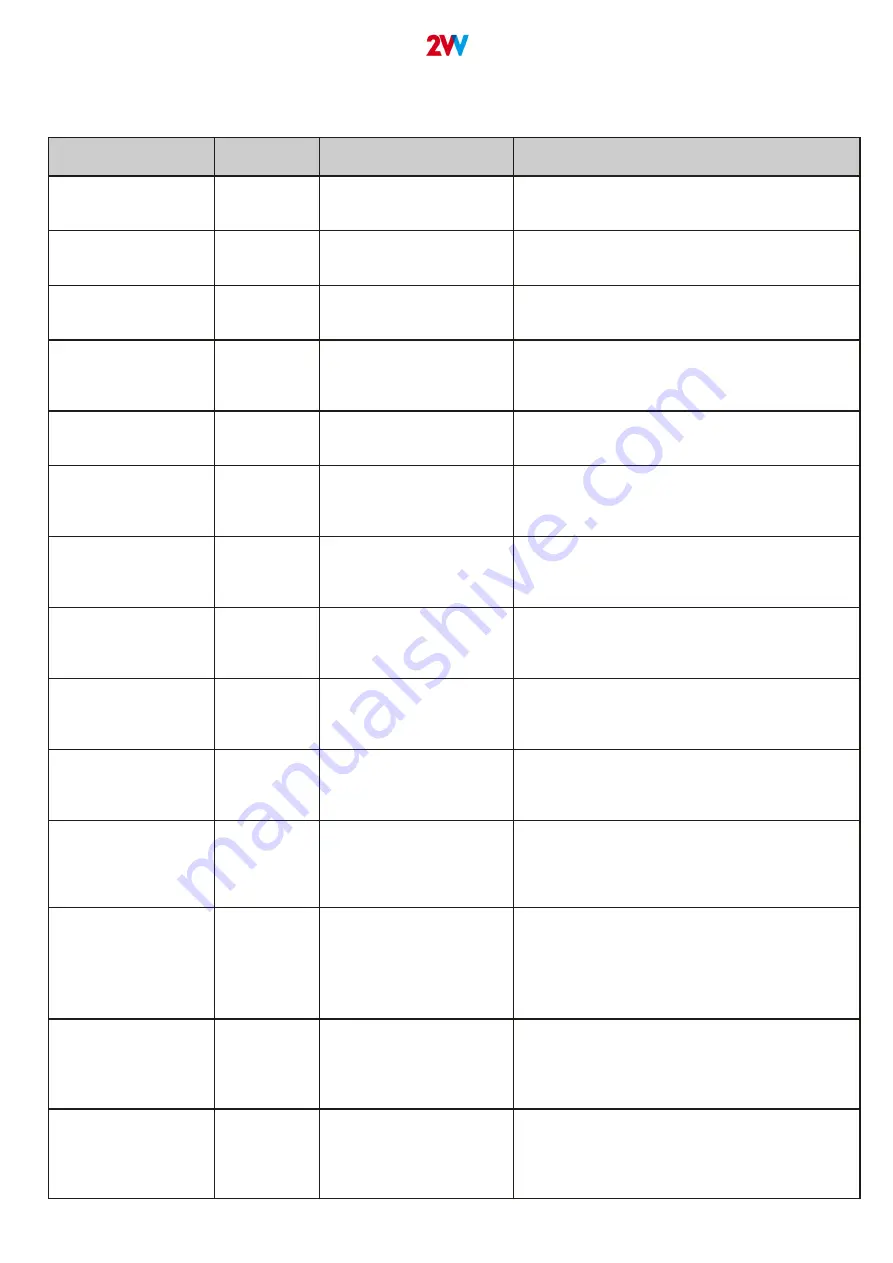
26
27
2VV.
Creating innovative solutions for you and your business since 1995.
ver.3 29-04-20
9. TROUBLESHOOTING
Description
Unit's behav
-
iour
Likely problem
Solution
12 – CO2 sensor
failure
Unit is venti
-
lating
Defective air quality sen
-
sor
Check that the CO2 sensor is connected correct
-
ly or check that it is operating correctly (output
signal value)
13 - Failure of rotary
heat exchanger
Unit is not
working
Failure of rotary heat ex
-
changer
Check that the input error is correctly connected
to the electronics or check what type of error the
heat exchanger is indicating.
14 - ADB module er
-
ror
Unit is venti
-
lating
Failure of adiabatic mod
-
ule
Check that the input error is correctly connected
to the electronics or, if necessary, that the adia
-
batic module is operating correctly
15 - Heat pump error
Unit is venti
-
lating
Heat pump failure
Check that the input error is correctly connected
to the electronics or, if necessary, that the heat
pump is operating correctly (according to the
instructions of its manufacturer)
16 – Inlet – External
temperature sensor
failure (T-EXT1)
Unit is not
working
Room temperature sensor
failure
Check that the sensor is correctly connected to
the electronics or test it measuring its resistance
(the resistance value at +20°C is around 10kΩ
)
17 – Inlet – Failure
of the temperature
sensor behind the ex
-
changer (T-EXT2)
Unit is not
working
Room temperature sensor
failure
Check that the sensor is correctly connected to
the electronics or test it measuring its resistance
(the resistance value at +20°C is around 10kΩ
)
18 – Inlet – Tempera
-
ture sensor failure
in the supply canal
(T-EXT3)
Unit is not
working
Room temperature sensor
failure
Check that the sensor is correctly connected to
the electronics or test it measuring its resistance
(the resistance value at +20°C is around 10kW)
19 - Inlet - Tempera
-
ture sensor failure
after the second ex
-
changer (T-EXT4)
Unit is not
working
Room temperature sensor
failure
Check that the sensor is correctly connected to
the electronics or test it measuring its resistance
(the resistance value at +20°C is around 10kΩ
)
20 - Exhaust – Tem
-
perature sensor failure
in the exhaust canal
(T-INT0)
Unit is not
working
Room temperature sensor
failure
Check that the sensor is correctly connected to
the electronics or test it measuring its resistance
(the resistance value at +20°C is around 10kΩ
)
21 – Exhaust – Tem
-
perature sensor failure
in the exhaust canal
(T-INT1)
Unit is not
working
Room temperature sensor
failure
Check that the sensor is correctly connected to
the electronics or test it measuring its resistance
(the resistance value at +20°C is around 10kΩ
)
22 – Exhaust – Failure
of the temperature
sensor of the ex
-
changer's anti-freeze
protection (T-INT2)
Unit is not
working
Room temperature sensor
failure
Check that the sensor is correctly connected to
the electronics or test it measuring its resistance
(the resistance value at +20°C is around 10kΩ
)
23 - Temperature
sensor failure of the
exchanger's water
supply (T_WATER_
IN)
Unit is not
working
Room temperature sen-
sor failure
Check that the sensor is correctly connected
to the electronics or test it measuring its resis-
tance (the resistance value at +20°C is around
10
kΩ
)
24 - Failure in the re-
turn water sensor of
exchanger (T_WA-
TER_OUT)
Unit is not
working
Room temperature sen-
sor failure
Check that the sensor is correctly connected
to the electronics or test it measuring its resis-
tance (the resistance value at +20°C is around
10
kΩ
)
25 – Room tempera-
ture sensor failure
(T_Room)
Unit is ven-
tilating
Room temperature sen-
sor failure
Check that the sensor is correctly connected
to the electronics or test it measuring its resis-
tance (the resistance value at +20°C is around
10
kΩ
)