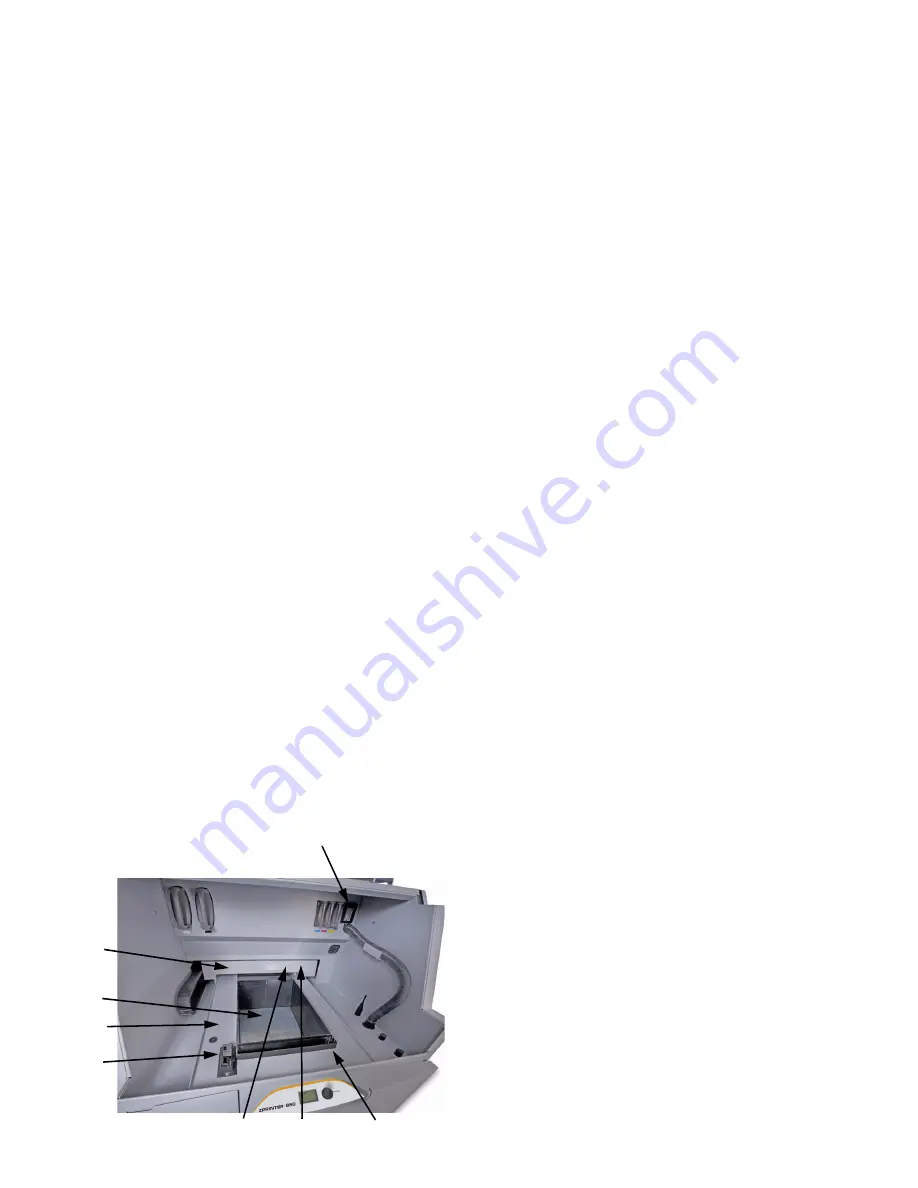
6
3dscentral.3dsystems.com
2. Check The Printer
Before you start your print job, it’s important that you check the
printer.
A clean, well-maintained printer produces better
parts, has less downtime, and needs fewer service calls.
1.
Open the printer top cover and pull the fast axis out toward
you.
2.
Check for loose powder in or around the Build Bed, Fast
Axis, and Deck. There should be no powder in these areas
prior to printing. If you need to clean these areas, follow the
steps in
Section 6.1, “Vacuum Up Excess Powder”
.
3.
Check that the Debris Separator, Parking Caps, the Rails and
Carriage, and the Service Station are clean. If any of these
need cleaning, follow the procedures in these sections:
•
Section 6.2, “Clean The Debris Separator”
•
Section 6.3, “Clean the Parking Caps”
•
Section 6.4, “Clean The Rails and Carriage”
•
Section 6.5, “Clean The Service Station”
4.
Close the printer top cover. The Fast Axis reparks and the
printer goes Online.
Service
Station
Build
Bed
Deck
Fast
Axis
Deck
Debris Separator
Parking Caps
(hidden)
Rails and Carriage
(hidden)