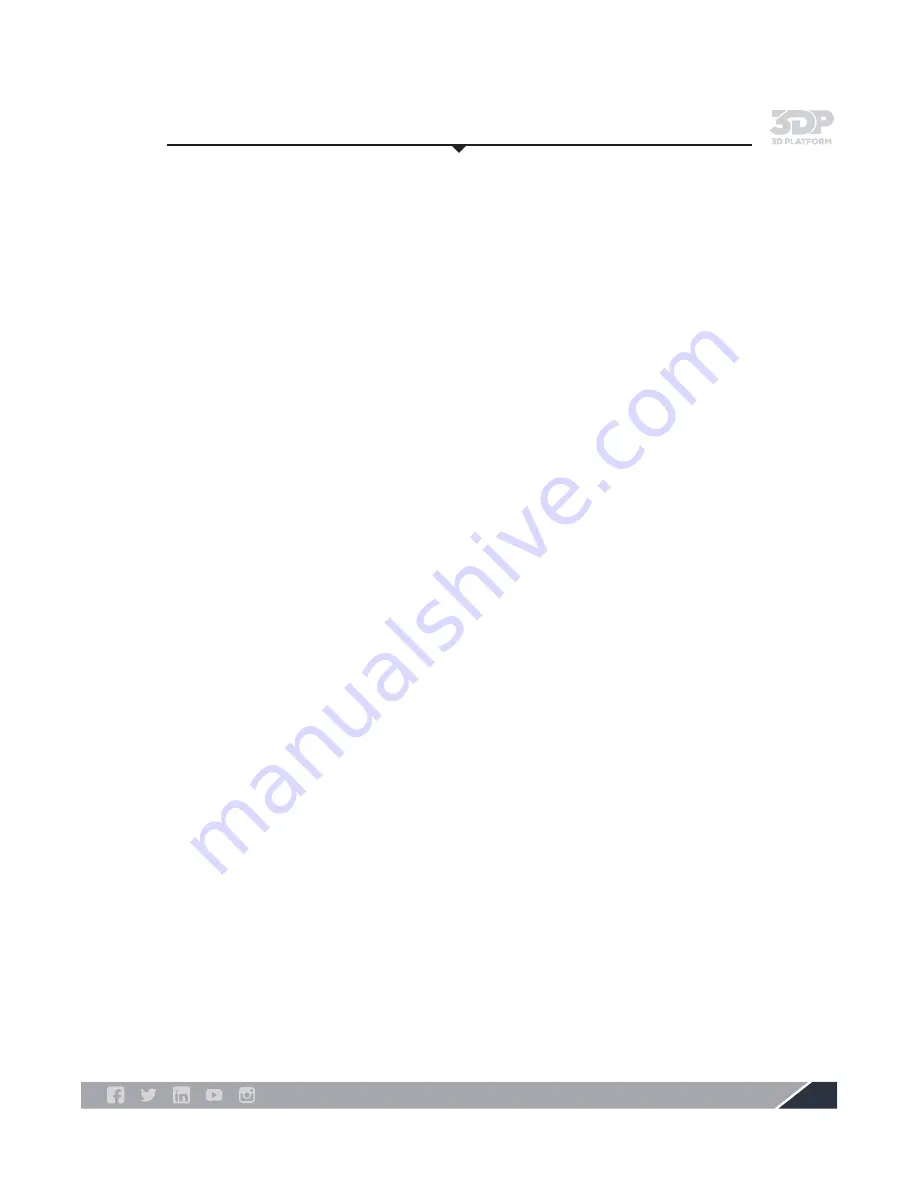
3DPlatform.com
11
G-Codes
// M30 - Delete file from SD (M30 filename.g)
// M31 - Output time since last M109 or SD card start to serial
// M32 - Select file and start SD print (Can be used _while_ printing
from SD card files): syntax "M32 /path/filename#", or "M32
S<startpos bytes> !filename#" Call gcode file : "M32 P !filename#"
and return to caller file after finishing (similar to #include). The '#'
is necessary when calling from within sd files, as it stops buffer
prereading
// M42 - Change pin status via gcode Use M42 Px Sy to set pin x to
value y, when omitting Px the onboard led will be used.
// M80 - Turn on Power Supply
// M81 - Turn off Power Supply
// M82 - Set E codes absolute (default)
// M83 - Set E codes relative while in Absolute Coordinates (G90)
mode
// M84 - Disable steppers until next move, or use S<seconds> to
specify an inactivity timeout, after which the steppers will be
disabled. S0 to disable the timeout.
// M85 - Set inactivity shutdown timer with parameter S<seconds>.
To disable set zero (default)
// M92 - Set axis_steps_per_unit - same syntax as G92
// M104 - Set extruder target temp
// M105 - Read current temp
// M106 - Fan on
// M107 - Fan off
// M109 - Sxxx Wait for extruder current temp to reach target temp.
Waits only when heating
// Rxxx Wait for extruder current temp to reach target temp. Waits
when heating and cooling
// IF AUTOTEMP is enabled, S<mintemp> B<maxtemp> F<factor>.
Exit autotemp by any M109 without F
// M112 - Emergency stop
// M114 - Output current position to serial port
// M115 - Capabilities string
// M117 - Display message
// M119 - Output Endstop status to serial port
// M126 - Solenoid Air Valve Open (BariCUDA support by jmil)
// M127 - Solenoid Air Valve Closed (BariCUDA vent to atmospheric
pressure by jmil)
// M128 - EtoP Open (BariCUDA EtoP = electricity to air pressure
transducer by jmil)
// M129 - EtoP Closed (BariCUDA EtoP = electricity to air pressure
transducer by jmil)
// M140 - Set bed target temp
// M150 - Set BlinkM Color Output R: Red<0-255> U(!): Green<0-
255> B: Blue<0-255> over i2c, G for green does not work.
// M190 - Sxxx Wait for bed current temp to reach target temp. Waits
only when heating
// Rxxx Wait for bed current temp to reach target temp. Waits when
heating and cooling
// M200 D<millimeters>- set filament diameter and set E axis units to
cubic millimeters (use S0 to set back to millimeters).
// M201 - Set max acceleration in units/s^2 for print moves (M201
X1000 Y1000)
// M202 - Set max acceleration in units/s^2 for travel moves (M202
X1000 Y1000) Unused in Marlin!!
// M203 - Set maximum feedrate that your machine can sustain
(M203 X200 Y200 Z300 E10000) in mm/sec
// M204 - Set default acceleration: S normal moves T filament only
moves (M204 S3000 T7000) in mm/sec^2 also sets minimum
segment time in ms (B20000) to prevent buffer under-runs and
M20 minimum feedrate
// M205 - Advanced settings: minimum travel speed S=while
printing T=travel only, B=minimum segment time X= maximum xy
jerk, Z=maximum Z jerk, E=maximum E jerk
// M206 - Set additional (babystepped) homing offset
// M207 - Set retract length S[positive mm] F[feedrate mm/min]
Z[additional zlift/hop], stays in mm regardless of M200 setting
// M208 - Set recover=unretract length S[positive mm surplus to the
M207 S*] F[feedrate mm/sec]
// M209 - S<1=true/0=false> enable automatic retract detect if the
slicer did not support G10/11: every normal extrude-only move will
be classified as retract depending on the direction.
// M218 - Set hotend offset (in mm): T<extruder_number> X<offset_
on_X> Y<offset_on_Y>
// M220 S<factor in percent> or P<incremental percentage>- set
speed factor override percentage
// M221 S<factor in percent> or P<incremental percentage>- set
extrude factor override percentage
// M226 P<pin number> S<pin state>- Wait until the specified pin
reaches the state required
// M240 - Trigger a camera to take a photograph
// M250 - Set LCD contrast C<contrast value> (value 0..63)
// M280 - Set servo position absolute. P: servo index, S: angle or
microseconds
// M300 - Play beep sound S<frequency Hz> P<duration ms>
// M301 - Set PID parameters P I and D
// M302 - Allow cold extrudes, or set the minimum extrude
S<temperature>.
// M303 - PID relay autotune S<temperature> sets the target
temperature. (default target temperature = 150C)
// M304 - Set bed PID parameters P I and D
// M400 - Finish all moves
// M401 - Lower z-probe if present
// M402 - Raise z-probe if present
// M404 - N<dia in mm> Enter the nominal filament width (3mm,
1.75mm ) or will display nominal filament width without parameters
// M405 - Turn on Filament Sensor extrusion control. Optional
D<delay in cm> to set delay in centimeters between sensor and
extruder
// M406 - Turn off Filament Sensor extrusion control
// M407 - Displays measured filament diameter
// M500 - Stores parameters in EEPROM
// M501 - Reads parameters from EEPROM (if you need reset them
after you changed them temporarily)
// M502 - Reverts to the default "factory settings", You still need to
store them in EEPROM afterwards if you want to
// M503 - Print the current settings (from memory not from EEPROM)
// M540 - Use S[0|1] to enable or disable the stop SD card print on
endstop hit (requires ABORT_ON_ENDSTOP_HIT_FEATURE_
ENABLED)
// M600 - Pause for filament change X[pos] Y[pos] Z[relative lift]
E[initial retract] L[later retract distance for removal]
// M601 - Resume the print from filament change
// M602 - Use extra extruder(s) as resumable backup
// M665 - Set delta configurations
// M666 - Set delta endstop adjustment
// M605 - Set dual x-carriage movement mode: S<mode> [
X<duplication x-offset> R<duplication temp offset> ]
// M907 - Set digital trimpot motor current using axis codes
// M908 - Control digital trimpot directly
// M350 - Set microstepping mode
// M351 - Toggle MS1 MS2 pins directly