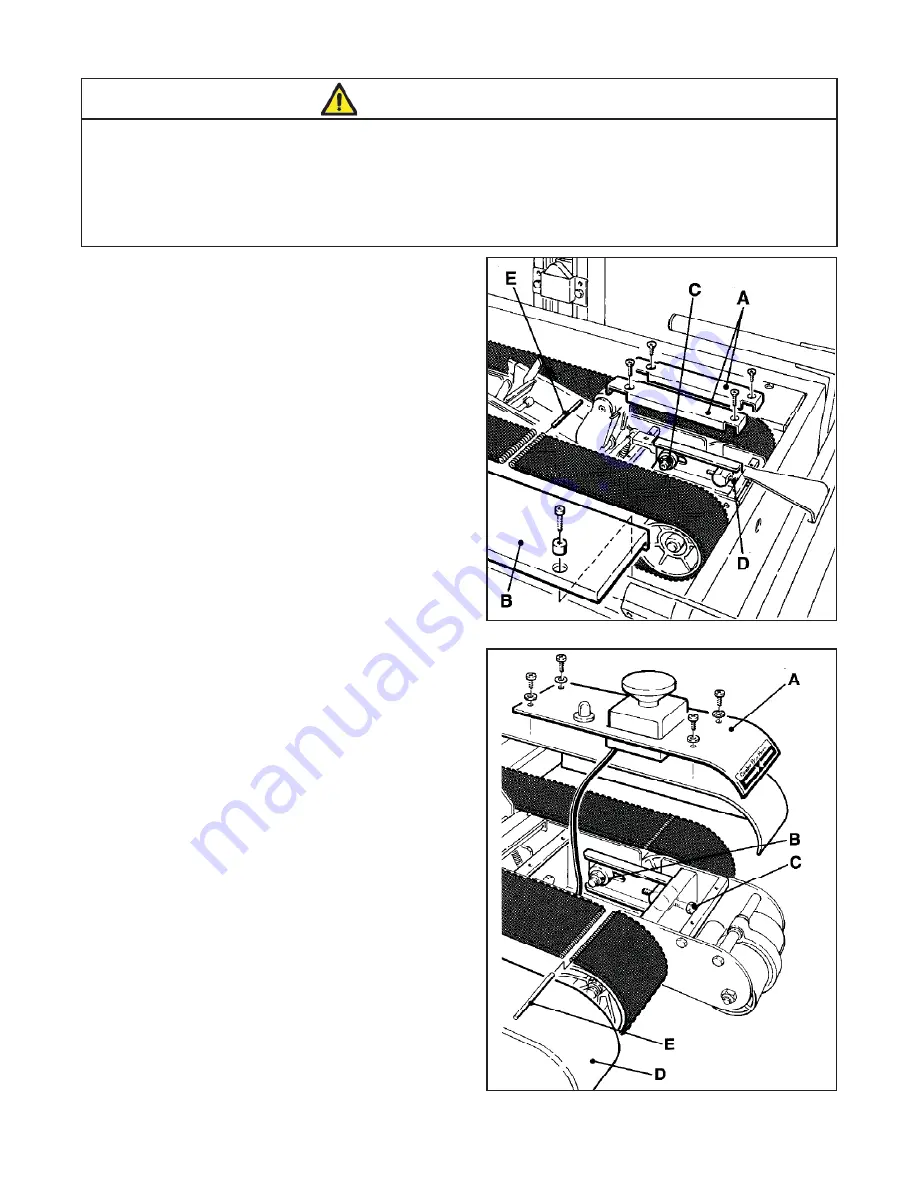
44
Maintenance
(continued)
13.8 Box Drive Belt Replacement
Note –
3M recommends the replacement of drive
belts in pairs, especially if belts are
unevenly
worn.
Lower Drive Belts
Figure 13-4
1. Remove and retain center plates
(A)
and four (4)
screws.
2. Remove and retain side cover
(B)
and fasteners.
3. Loosen, but do not remove lock nut
(C)
.
4. Loosen tension screw
(D)
until all belt tension is
removed.
5. Pull belt splicing pin
(E)
out and remove belt.
6. Place new belt over pulleys with laced splice
at top. Insert splicing pin.
Note –
Pin must not
extend beyond edge of belt.
7. Adjust belt tension as explained in
"Adjustments – Box Drive Belt Tension".
8. Replace side cover and center plates and
secure with original fasteners.
Upper Drive Belts
Figure 13-5
1. Remove and retain center plate
(A)
and four
screws and plain washers.
2. Loosen, but do not remove lock nut
(B)
.
3. Loosen tension screw
(C)
until all tension is
removed from belt.
4. Remove four (4) screws on side of belt guard
(D)
and slide belt guard out to expose belt.
5. Pull belt splicing pin
(E)
out and remove belt.
6. Place new belt over pulleys with laced splice
at top. Insert splicing pin.
Note –
Pin must not
extend beyond edge of belt.
7. Adjust belt tension as explained in
"Adjustments – Box Drive Belt Tension".
8. Replace front cover and belt guard(s) and
secure with original fasteners.
Figure 13-4 – Lower Drive Belt Replacement
•
To reduce the risk associated with mechanical and electrical hazards:
−
Turn electrical and air supply off and disconnect before performing any adjustments, maintenance or
servicing the machine or taping heads
•
To reduce
the risk associated with impact hazards:
−
Always use appropriate supporting means when working under the upper drive assembly
WARNING
Figure 13-5 – Upper Drive Belt Replacement
700r3-NA
2011 November
Summary of Contents for 700r3
Page 4: ...THIS PAGE IS BLANK...
Page 6: ...6 THIS PAGE IS BLANK...
Page 8: ...iv THIS PAGE IS BLANK...
Page 62: ...52 THIS PAGE IS BLANK...
Page 64: ...54 16 TECHNICAL DIAGRAMS 16 1 Electric Diagram 700r3 NA 2011 November...
Page 68: ...58 THIS PAGE IS BLANK...
Page 70: ...60 2011 November 700r3 NA 700r3 Figure 15031 20...
Page 72: ...62 2011 November 700r3 NA 700r3 Figure 15009 Optional 35 36 37 38...
Page 74: ...64 2011 November 700r3 NA 700r3 Figure 3439 5...
Page 76: ...66 2011 November 700r3 NA 700r3 Figure 6246...
Page 78: ...68 2011 November 700r3 NA 700r3 Figure 15010 1...
Page 86: ...76 700r3 NA Random Case Sealer 700r3 Figure 15011 2 59 2011 November 700r3 NA...
Page 90: ...80 700r3 NA Random Case Sealer 700r3 2011 November 700r3 NA Figure 5920...
Page 94: ...84 THIS PAGE IS BLANK...
Page 96: ......
Page 98: ...THIS PAGE IS BLANK...
Page 100: ...THIS PAGE IS BLANK...
Page 104: ...2 THIS PAGE IS BLANK...
Page 140: ...THIS PAGE IS BLANK...
Page 141: ......
Page 142: ......