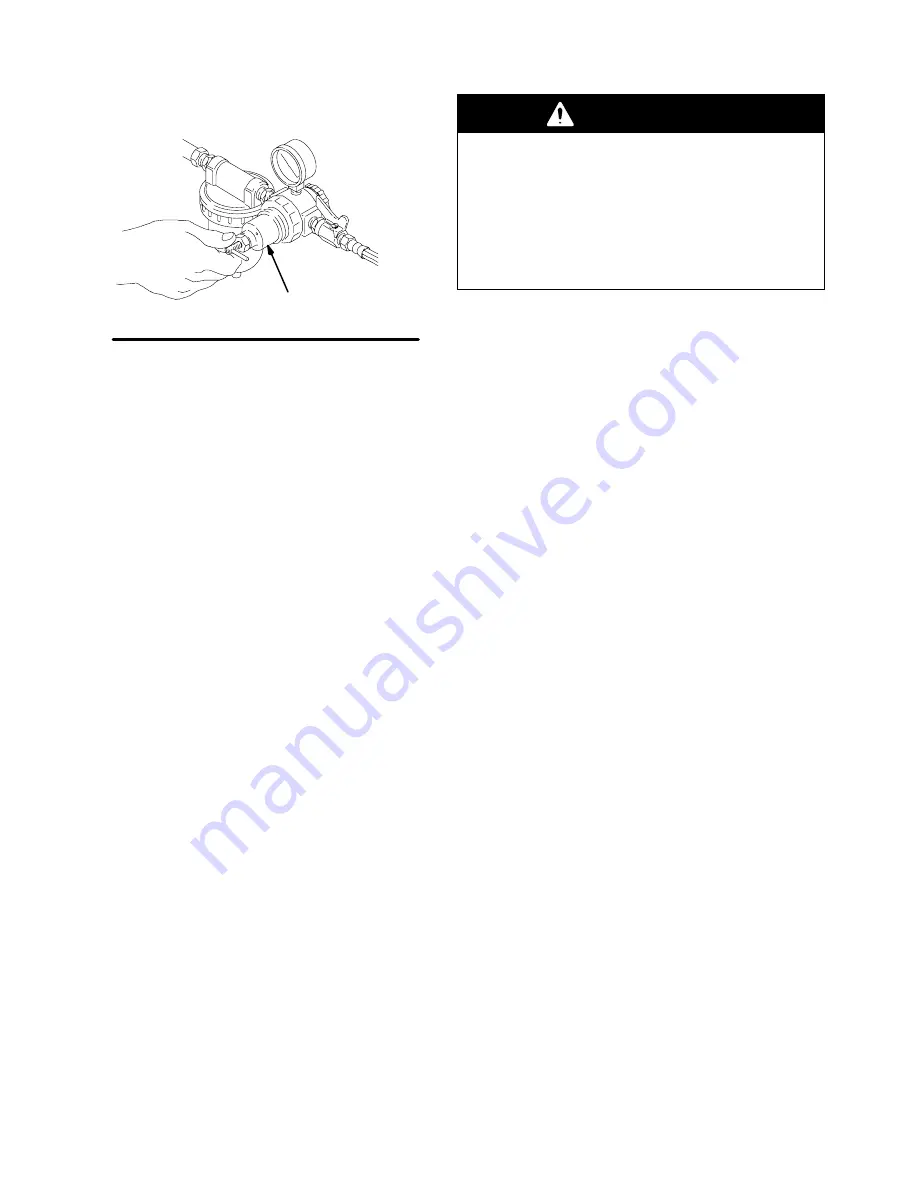
10
Setup
3.
Adjust the air supply regulator (F) to about 100 psi.
Fig. 12
F
01997
4.
Trigger the gun and adjust the gun inlet pressure,
turning the needle valve at the gun air inlet:
HVLP, Compliant
29 psi
Airspray
50psi
5.
Spray a test pattern to evaluate fluid flow and
atomization.
6.
To reach the desired pattern width, fluid flow rate,
and finish, make the following adjustments:
.
For a narrower pattern (25), turn the pattern
adjustment valve clockwise.
.
To reduce the fluid flow, turn the fluid adjust-
ment valve (21) clockwise to limit the trigger
travel or replace the nozzle with a smaller
orifice.
.
To improve atomization, reduce the fluid flow
rate. Increasing the air pressure can improve
atomization but may result in poor Transfer
Efficiency (TE) or non–compliant operation.
WARNING
PRESSURIZED EQUIPMENT HAZARD
To avoid injury, never open the fluid adjustment
knob (21) beyond the one half turn indicated in
Adjusting the Spray Pattern
, page 9. If the red
band on the knob stem (21) is visible, the knob is
not adjusted correctly and could result in serious
injury. Repeat steps in
Adjusting the Spray
Pattern,
page 9.
7.
For HVLP only, to measure the air cap atomizing
pressures, use the accessory aircap verification
kit.
NOTES:
If the fluid adjustment knob is turned in clockwise
all the way the gun will emit only air.
For maximum transfer efficiency, always use the
lowest air setting needed to achieve the desired
finish.
If available, use the fluid manufacturer’s recom-
mendations for this gun model to set the air line
pressure.
For Compliant guns
, to maintain compliant opera-
tion (TE equal to HVLP) the gun inlet pressure must
not exceed 29 psi.
For HVLP guns
, at 29 psi (200 kPa, 2.0 bar) gun
inlet air pressure, the pressure at the aircap will be
10 psi (70 kPa, 0.7 bar).
For HVLP guns
, local laws may limit the maximum
automatic air pressure to 10 psi (70 kPa, 0.7 bar) at
the air cap for HVLP compliance. The accessory Air
Cap Verification Kit 16231 is available to measure
the atomizing pressure at the air cap.