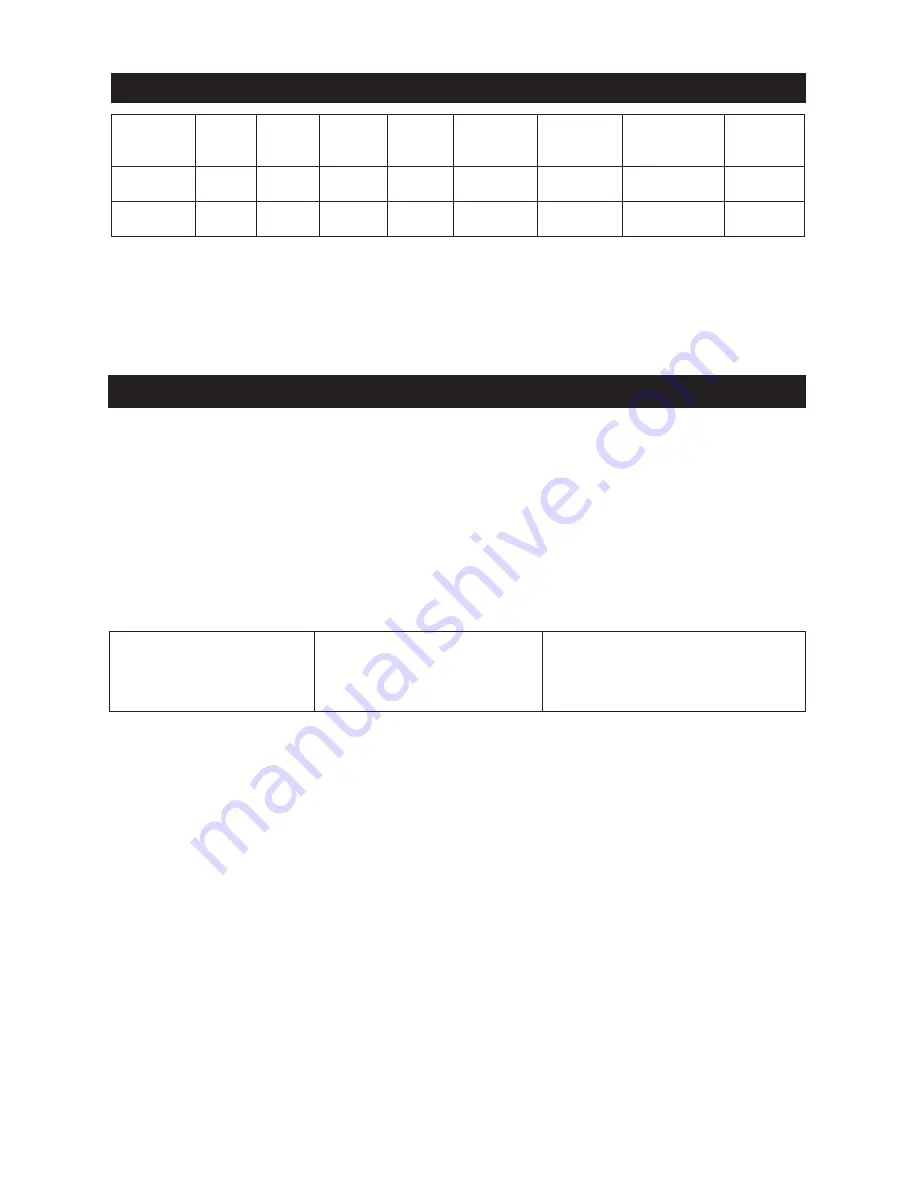
5
Product Configuration/Specifications:
Operating / Maintenance Instructions
PRIOR TO THE OPERATION
The tool is intended to be operated as a hand held tool. It is always recommended that while using the tool, operators stand on a solid floor, in a secure position
with a firm grip and footing. Be aware that the tool can develop a torque reaction. See the section “SAFETY PRECAUTIONS”.
Use a clean lubricated air supply that will give a measured air pressure at the tool of 6.2 bar (90 psig) when the tool is running with the lever fully depressed. It is
recommended to use an approved 10 mm (3/8 in) x 8 m (25 ft) maximum length airline. Connect the tool to the air supply as shown in Figure 1. Do not connect the
tool to the airline system without an easily accessible air shut off valve. It is strongly recommended that an air filter, regulator and lubricator (FRL) be used as shown
in Figure 1 as this will supply clean, lubricated air at the correct pressure to the tool. In any case appropriate air pressure regulators shall be used at all times while
operating this tool where the supply pressure exceeds the marked maximum of the tool. Details of such equipment can be obtained for your tool distributor. If such
equipment is not used, the tool should be manually lubricated. To manually lubricate the tool, disconnect the airline and put 2 to 3 drops of suitable pneumatic motor
lubricating oil such as 3M™ Air Tool Lubricant PN 20451 (or equivalent 10 centistoke oil) into the air inlet of the tool. Reconnect tool to the air supply and run tool
slowly for a few seconds to allow air to circulate the oil. If the tool is used frequently, lubricate it on a daily basis or lubricate it if the tool starts to slow or lose power.
It is recommended that the air pressure at the tool be 6.2 bar (90 psig) while the tool is running so the maximum RPM is not exceeded. The tool can be run at lower
pressures but should never be run higher than 6.2 bar (90 psig). If run at lower pressure the performance of the tool is reduced.
* Declared noise levels; measurements carried out in accordance with standard EN ISO 15744.
** Declared vibration levels in accordance with EN ISO 20643 and EN ISO 28927.
IMPORTANT NOTE:
The noise and vibration values stated in the table are from laboratory testing in conformity with stated codes and standards and are not
sufficient risk evaluation for all exposure scenarios. The actual exposure values and amount of risk or harm experienced to an individual is unique to each
situation and depends upon the surrounding environment, the way in which the individual works, the particular material being worked, work station design, as
well as upon the exposure time and the physical condition of the user. 3M™ cannot be held responsible for the consequences of using declared values instead of
actual exposure values for any individual risk assessment.
For Series C grinders, the angle head and gears have been designed to last the life of the tool without periodic maintenance. When rebuilding or repairing the tool,
lubricate angle head with Castrol Longtime PD 00 grease or equivalent lithium thickener, NCGI Grade 00 grease, 1 tsp approximate quantity.
Model
Number
Speed
RPM
Spindle
(in.)
Product
Net WT. kg.
(lb.)
Height
mm (in.)
*Noise Level
dBA Pressure
(Power)
**Vibration
Level
m/s
2
(ft/s
2
)
**Uncertainty
K m/s
2
(ft/s
2
)
Series
Designation
28403
12,000
3/8-24
T-27
1.60 (3.53)
108 (4.25)
83.0 (94.6)
3.24 (10.63)
0.04 (0.13)
C
28405
12,000
5/8-11
T-27
1.71 (3.78)
108 (4.25)
83.7 (95.3)
6.61 (21.67)
0.26 (0.85)
C
Recommended Airline
Size - Minimum
Recommended Maximum
Hose Length
Air Pressure
10mm
3/8 in
8 meters
25 feet
Maximum Working Pressure 6.2 bar
90psig
Recommended Minimum
NA
NA