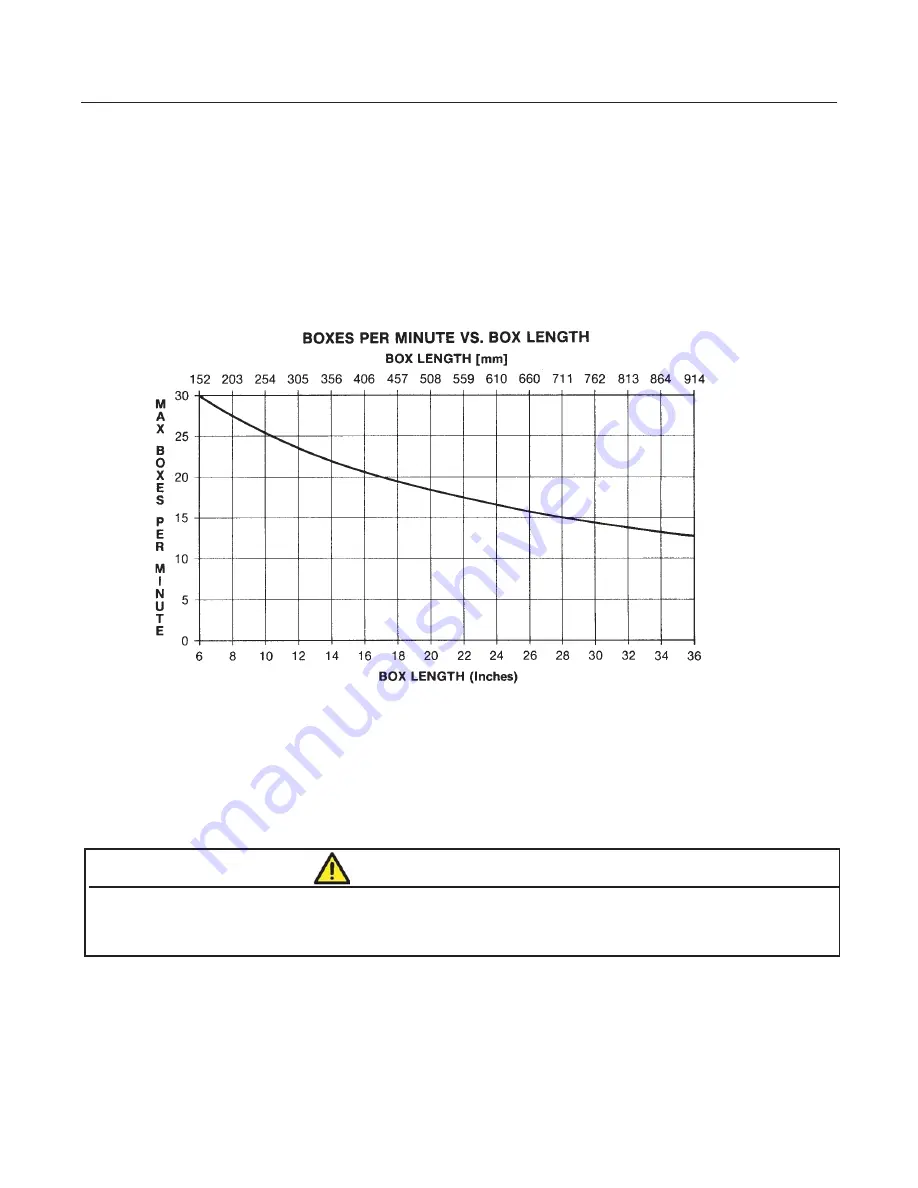
12
4-SPECIFICATIONS
2011 April
a80b-NA
4.1 Power Requirements:
Electrical – 115 VAC, 60 Hz, 3.6 A
These machines are equipped with a 2.4m
[8 foot] standard neoprene covered power cord and a grounded plug.
Contact your 3M Representative for power requirements not listed above.
4.2 Operating Rate:
Belt speed is 0.40 m/s [78 ft/min]
IMPORTANT SAFEGUARD
IMPORTANT SAFEGUARD
4.5 Tape Width:
Minimum – 36mm [1-1/2 inches]
Maximum – 48mm [2 inches]
4.4 Tape
Scotch
®
pressure-sensitive
fi
lm box sealing tapes.
4.3 Operating Conditions
Use in dry, relatively clean environments at 4.4
o
C to 48.9
o
C [40
o
F to 120
o
F] with clean, dry boxes.
Note:
Machine should not be washed or subjected to conditions causing moisture condensation
on
components.
•
To reduce the risk associated with fi re and explosion hazards:
−
Do not operate this equipment in potentially
fl
ammable or explosive environments.
WARNING
Actual production rate is dependent on operator's dexterity.
Boxes must be 18 inches (455mm) apart minimum.
Summary of Contents for 3M-Matic a80b
Page 4: ...THIS PAGE IS BLANK ...
Page 6: ...6 THIS PAGE IS BLANK ...
Page 8: ...THIS PAGE IS BLANK ...
Page 42: ...32 THIS PAGE IS BLANK ...
Page 43: ...33 2011 April a80b NA 16 TECHNICAL DIAGRAMS continued 16 1 Electric Diagram ...
Page 46: ...36 THIS PAGE IS BLANK ...
Page 56: ...46 2011 April a80b NA Figure 10916 a80b ...
Page 58: ...48 THIS PAGE IS BLANK ...