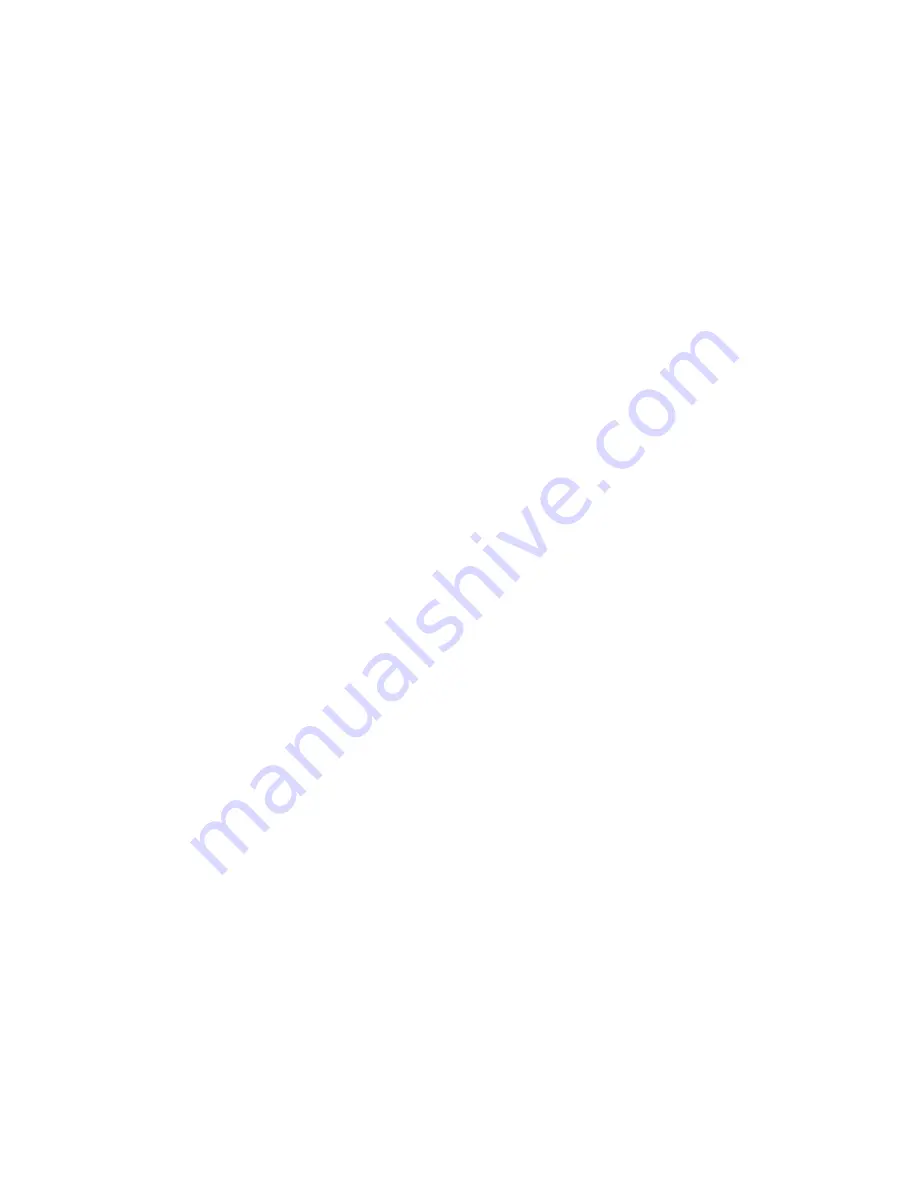
4-9
AFTER SERVICE START-UP
Whenever the controller is unplugged or the system is put in bypass for maintenance, a start-up is required. This start-up is not normally as extensive as the new
system start-up procedure needs to be followed.
The initial power-up procedure should be used if a new controller or a new valve has been installed. This procedure is explained in the users manual.
The following service start-up procedure can be used when the controller was programmed prior to servicing the unit and removing power. The unit should be fully
assembled with the cover off.
To start-up after service:
1) Plug the transformer into the controller. Resin/media volume should not need to be entered. If the display is fl ashing three dashes and a decimal point, contact
the factory.
2) Set time of day and day of week if necessary.
NOTE: Time of day and day of week settings are stored in a temporary memory and will be maintained at least 8 hours.
The display will fl ash four dashes and a colon if the time of day needs to be set. If the display shows the correct time, proceed to step 5.
3) The UP and DOWN arrows are used to set the time of day. When the correct time is displayed push SET. If using the 12 hour setting PM will be displayed behind
the time. AM is not designated.
4) Use the UP and DOWN arrow buttons to move a small fl ag (box) at the top of the display under the day of the week. When the correct day is fl agged push SET.
The controller is ready to operate. The media tank should be ready for operation.
5) Hold the REGEN button on the controller down for fi ve seconds. This will initiate a manual regeneration. The controller will indicate that the motor is turning the
camshaft to the C1 cycle (Backwash) position. The display will show the total regen time remaining and the hourglass will fl ash when the motor is running.
6) Open the supply valve to the 1/4 open position. Any air in the media tank and valve will escape from the valves’ drain line.
7) Open supply valve to full open.
8) Advance the controller to the Refi ll Position. From cycle C1 (Backwash), press and hold the SET button. This will display the current cycle. Press the UP arrow
to advance to the next cycle.
Continue to advance through each cycle until you have reached cycle C9 (Refi ll).
NOTE: As you advance through each cycle there will be a slight delay before you can advance to the next cycle. The hourglass icon will fl ash while the camshaft is
indexing to each cycle. There may be a pause at cycle C4 (System Pause). This cycle allows the water pressure to equalize on each side of the valve discs before
moving on to the next cycle. The hourglass will fl ash indicating that the system is paused.
9) Allow a small amount of water to fl ow into the brine tank. Press SET and UP buttons simultaneously to advance to the treated water position.
10) Turn on a faucet and run the water until it is clear.
The unit is ready for operation.