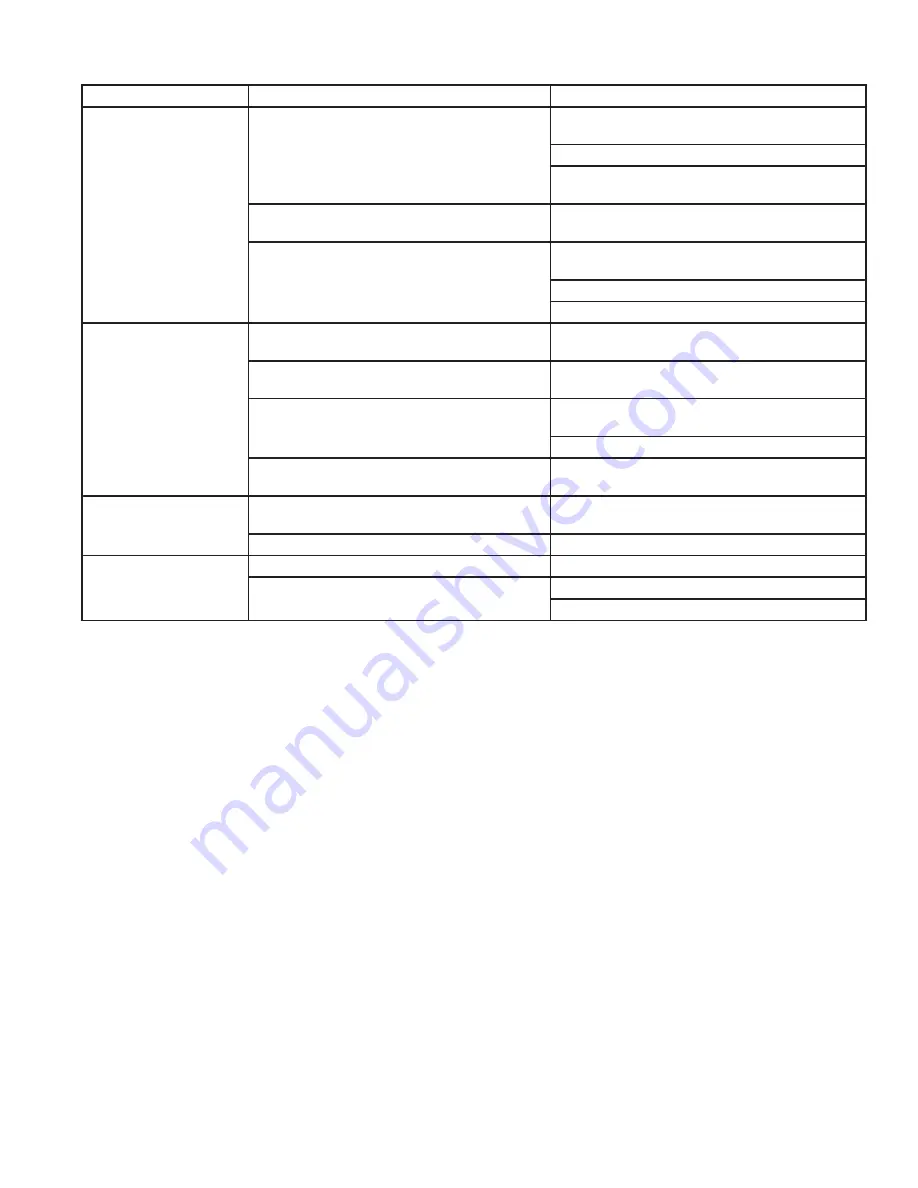
PROBLEM
CAUSE
SOLUTION
1
Excessive pressure drop
through fi lter
A
Filter not backwashing
1
Check motor by manually initiating a regeneration, re-
place as necessary
2
Check for uninterrupted power supply.
3
Check backwash frequency. Change program if neces-
sary.
B
Filter bed loaded with sand.
1
Verify sediment being reduced is less dense than the
fi lter media.
C
“Cementing” or “Channeling” of media.
1
Probe bed for this condition. Verify adequate pumping
rate for backwashing.
2
Check for frozen, plugged or restricted drain line.
3
Check for adequate backwash frequency.
2
Contaminant not being
properly reduced.
A
Leaking bypass valve.
1
Check bypass valve in “SERVICE” position. Repair or re-
place if necessary.
B
Internal valve leak.
1
Check piston and spacers and seals. Replace as neces-
sary.
C
Distributor not properly seated in control valve.
1
Make sure distributor is in tube adaptor protruding from
bottom of control valve.
2
Check distributor tube o-ring. Replace as necessary.
D
Flow rate too high for fi lter.
1
Check demand requirements against fi lter recommend-
ed fl ow rates.
3
Filter raises pH too high
(Neutralizer)
A
Filter is brand new.
1
Crack the bypass valve allowing some water to bypass
the unit.
B
Wrong media used.
1
Rebed unit.
4
Filter fails to raise pH
(Neutralizer)
A
Flow rates too high.
1
Verify demand rate does not exceed fi lter rating.
B
Filter bed cemented or channeled.
1
Verify adequate pumping rate for backwashing unit.
2
Check drain line for freezing, plugging or restrictions.
SECTION 4: TROUBLESHOOTING
4-1