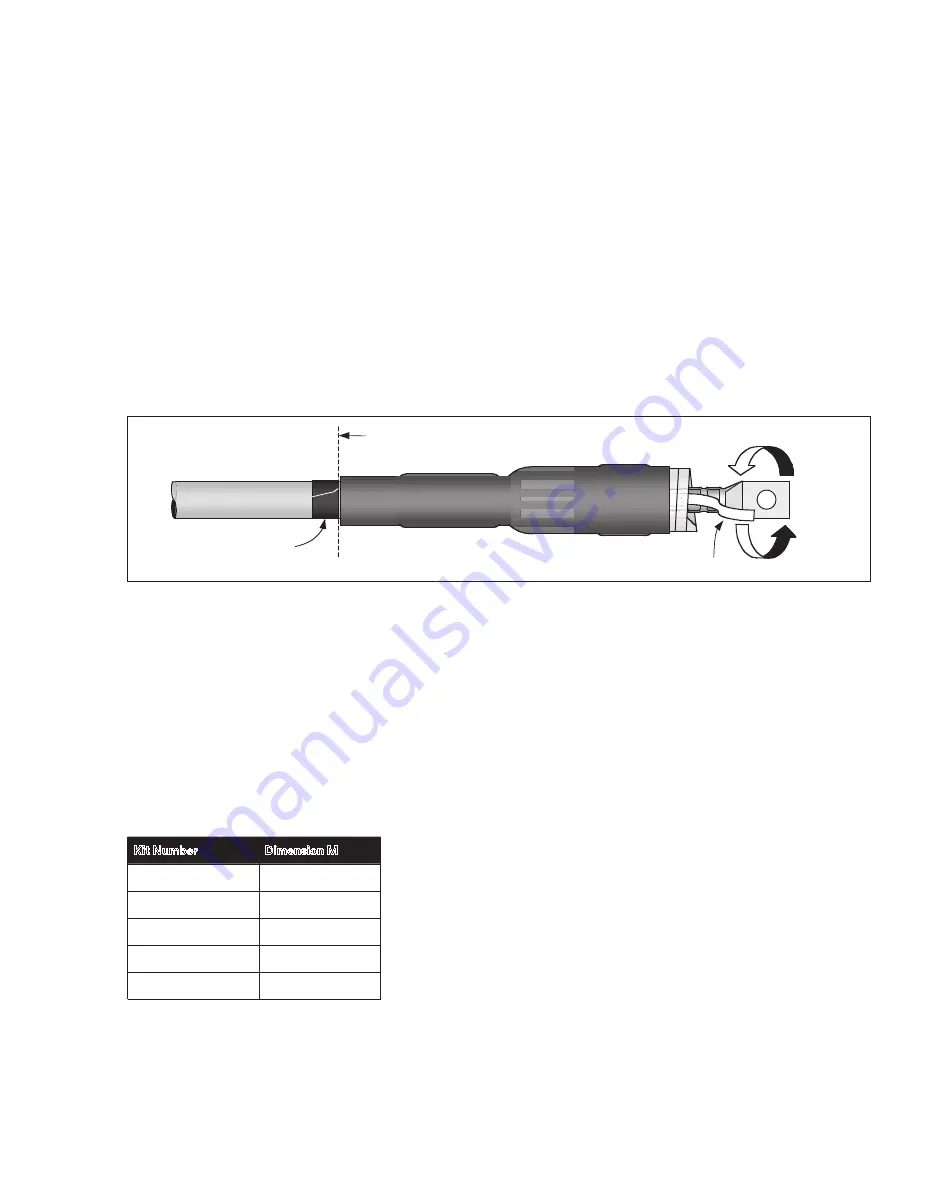
17
78-8124-5866-5-E
3M
™
Cold Shrink QT-lll Silicone Rubber Three Core Inverted Skirted Termination
with High-K Stress Relief
6.6 Install Tubular 3M
™
Cold Shrink QT-III Silicone Rubber Termination assemblies.
a. Remove the inner red shipping core from the termination assembly by pulling and unwinding the loose red
core end.
b. Position the termination assembly with the loose white core ribbon directed toward the terminal lug.
c. Align the base of the termination (not the plastic core) with the installation marker tape as shown (Figure 23).
d. Grasp the loose white core ribbon. Pull the core while unwinding, counterclockwise, starting with the loose
end (Figure 23). Be sure to alternate the pulling and unwinding actions (pull-unwind-pull-unwind-etc.) to
help prevent the core material from binding up as the core is being removed.
Note: After the silicone rubber termination makes adequate contact (approximately 1.0" (25 mm)), release the
assembly and continue unwinding the core.
DO NOT PULL OR PUSH ON THE TERMINATION ASSEMBLY WHILE
UNWINDING THE CORE.
e. Remove the installation marker tape.
Termination Base Aligned With Marker Tape Edge
Marker Tape
White Core Ribbon
Counterclockwise
Rejacketing Sleeve
Figure 23
6.7 Install Cold Shrink skirted insulators.
a. Position skirted insulator over previously installed tubular termination as shown (Figure 24).
b. Align skirted insulator body (not the core) to install Dimension [M] from base of tubular termination (Figure 24).
c. Grasp the loose white core ribbon (Figure 24). Pull the core while unwinding, counterclockwise, starting
with the loose end (Figure 24). Be sure to alternate the pulling and unwinding actions (pull-unwind-pull-
unwind-etc.) to help prevent the core material from binding up as the core is being removed.
Note: After skirted insulator makes adequate contact (approximately 1.0" (25 mm)), release the assembly and continue
unwinding the core.
DO NOT PULL OR PUSH ON THE ASSEMBLY WHILE UNWINDING.
Kit Number
Dimension M
7620-S-2-INV-3G
.5" (12,7 mm)
7621-S-2-INV-3G
.5" (12,7 mm)
7622-S-2-INV-3G
3.5" (88,9 mm)
7693-S-4-INV-3G
3.5" (88,9 mm)
7695-S-4-INV-3G
3.5" (88,9 mm)