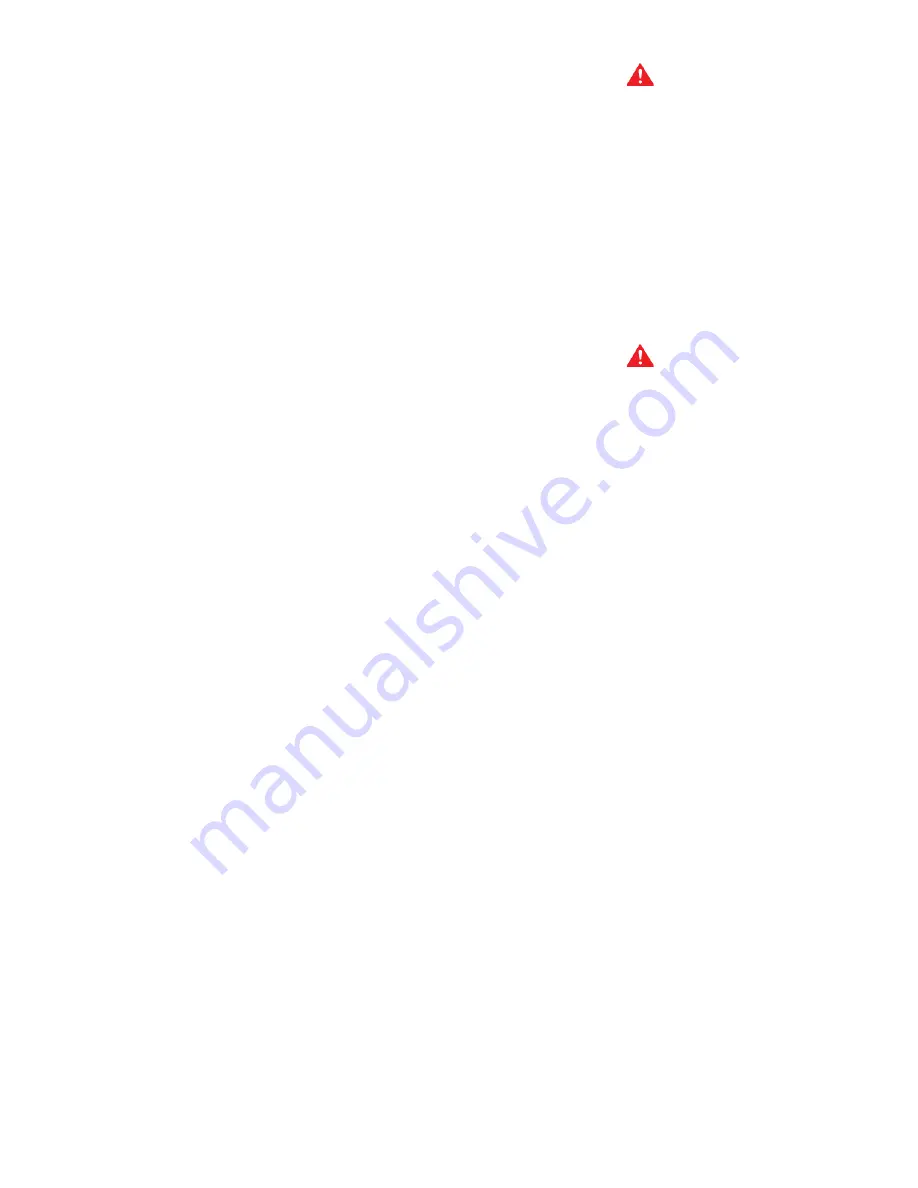
17
OPERATION
IMPORTANT
Only qualified personnel shall perform the initial firing of the heater.
At this time the user should not hesitate to ask the start-up
technician any questions regarding the operation and
maintenance of the unit.
Lighting and Operating instructions are included with this manual.
By using these instructions, the user may be able to make minor
operational adjustments and save unnecessary service calls.
However the user should not attempt repairs, but should contact
a service technician or gas supplier.
GENERAL
Never operate the water heater without first making sure the water
heater and system are filled with water, in addition:
•
Make sure a temperature and pressure relief valve is installed
at the water heater and if used, the storage tank. Also check
for leaks.
•
Also be sure to check the gas piping for leaks before beginning
the initial firing of the boiler.
FILLING
1. Close the systems drain valve by turning handle clockwise.
2. Open a nearby hot water faucet to permit the air in the system
to escape.
3. Fully open the cold water inlet pipe valve allowing the heater
and piping to be filled.
4. Close the hot water faucet as water starts to flow.
5. The heater is ready to be operated.
PURGING OF GAS LINE
Gas line purging is required with new piping or systems in which
air has entered.
CAUTION
PURGING SHOULD BE PERFORMED BY PERSONS
EXPERIENCED IN THIS TYPE GAS SERVICE. TO AVOID RISK
OF FIRE OR EXPLOSION, PURGE DISCHARGE MUST NOT
ENTER CONFINED AREAS OR SPACES WHERE IGNITION
CAN OCCUR. THE AREA MUST BE WELL VENTILATED AND
ALL SOURCES OF IGNITION MUST BE INACTIVATED OR
REMOVED.
BEFORE PLACING THE WATER HEATER IN OPERATION,
CHECK FOR GAS LEAKAGE. USE A SOAP AND WATER
SOLUTION OR OTHER MATERIAL ACCEPTABLE FOR THE
PURPOSE OF LOCATING GAS LEAKS. DO NOT USE
MATCHES, CANDLES, FLAME OR OTHER SOURCES OF
IGNITION FOR THIS PURPOSE.
CAUTION
BEFORE PROCEEDING WITH THE OPERATION OF THE UNIT,
MAKE SURE HEATER AND SYSTEM ARE FILLED WITH WATER
AND ALL AIR IS EXPELLED FROM HEATER AND PIPING.
THE MAIN MANUAL GAS SHUTOFF VALVE AND THE PILOT
ADJUSTING VALVE (WHEN APPLICABLE) MUST HAVE BEEN
CLOSED FOR AT LEAST FIVE (5) MINUTES. THIS WAITING
PERIOD IS AN IMPORTANT SAFETY STEP.
ITS PURPOSE IS
TO PERMIT GAS THAT MIGHT HAVE ACCUMULATED IN THE
COMBUSTION CHAMBER TO CLEAR.
IF YOU DETECT GAS
AT THE END OF THIS PERIOD, DO NOT PROCEED WITH
LIGHTING. RECOGNIZE THAT GAS ODOR, EVEN IF IT SEEMS
WEAK MAY INDICATE PRESENCE OF ACCUMULATED GAS
SOMEPLACE IN THE AREA WITH A RISK OF FIRE OR
EXPLOSION. SEE THE FRONT PAGE FOR STEPS TO BE
TAKEN.
DO NOT USE THIS HEATER IF ANY PART HAS BEEN UNDER
WATER. IMMEDIATELY CALL A QUALIFIED SERVICE
TECHNICIAN TO INSPECT THE HEATER AND TO REPLACE
ANY PART OF THE CONTROL SYSTEM AND ANY GAS
CONTROL WHICH HAS BEEN UNDER WATER.
Light the unit in accordance with the instructions on the lighting
label attached to the boiler. These instructions are repeated in
the following.