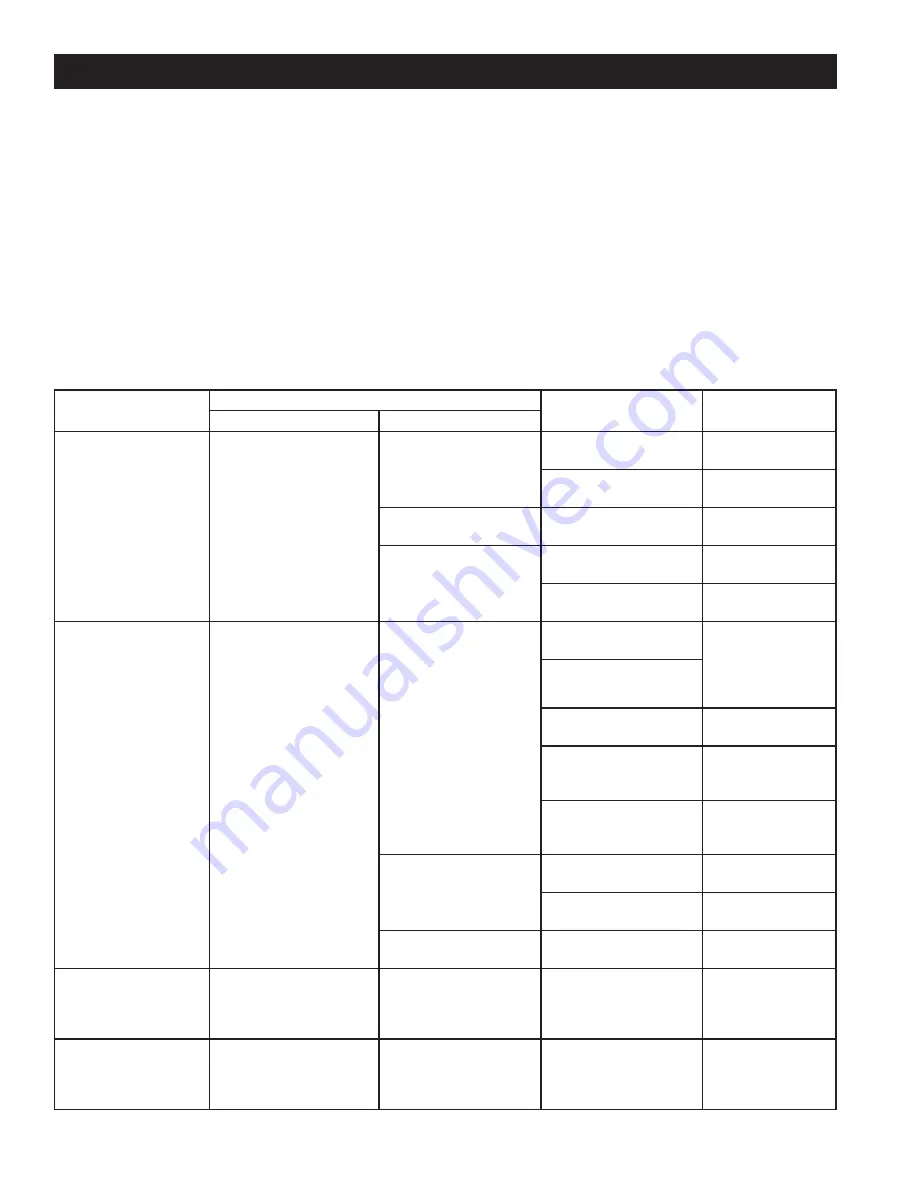
16
TABLE 3. CER-TEMP 80 RECOVERY SYSTEM CHECKOUT PROCEDURE
Before any extensive troubleshooting, perform the following:
Ensure that:
• Voltage (120 vac) is supplied to the boiler.
• System control (tank temperature control, thermostat,
etc.) is calling for boiler operation (call for heat).
• Other contacts (switches) are closed (relay, low water
cutoff, flow switch, coil protector, pressure switch, etc.).
• Gas supply pressure is within the maximum and minimum
operating ranges listed on the boiler rating plate/label.
• Voltage (24 vac) is supplied by transformer.
• Boiler is wired according to wiring diagram.
Note: Cross wiring the 24 volt circuit of the relay will short the
transformer.
• All wire terminals/connectors are firmly attached to
valves, modules, switches, limit controls, etc.
• For Propane (LP) models only check for possible lockout
condition of the ignition module.
Use this checkout for Cer-Temp 80 Recovery Systems. (For hot water supply application only)
CHECKOUT SEQUENCE
SYSTEM OPERATION
CAUSE
REMEDY
CORRECT
INCORRECT
Set tank temperature
control (thermostat)
20°F (10°C) below tank
water temperature.
Circulating pump and
burner shut off.
With thermal balancer,
pump off delay of
approximately 2 minutes.
Pump and burner remain
on.
Tank temperature control
(thermostat) defective.
Replace.
System wiring is
incorrect.
Correct wiring.
Circulating pump on.
Pump wired for
continuous operation.
Correct wiring.
Burner on.
Gas control valve stuck
or defective.
Correct or replace
valve.
System wiring is
incorrect.
Correct wiring.
Set tank temperature
control (thermostat)
20°F (10°C) above tank
water temperature.
Circulating pump and
burner on.
Circulating pump on.
High limit control set too
low.
Replace. (If
problem proven to
be at this control by
applying jumper to
terminals.)
High limit control
differential too wide.
System wiring is
incorrect.
Correct wiring.
Coil protector switch has
activated.
Remove control
cover, depress
reset button.
Gas control valve or
wiring defective.
Check wiring.
Repair or replace
valve.
Circulating pump and
burner off.
Power off or system
wiring is incorrect.
Check power supply
and wiring.
Tank temperature control
(thermostat) defective.
Replace.
Burner on.
System wiring is
incorrect.
Correct wiring.
Boiler outlet
temperature exceeds
210°F (100°C).
Circulating pump on.
Circulating pump and
burner on.
High limit control
defective, or set too high
(max. should be set at
200°F).
Replace.
Set tank temperature
control (thermostat)
for desired water
temperature.
System maintains desired
water temperature.
TROUBLESHOOTING
Summary of Contents for Burkay HW-300
Page 4: ...4 GENERAL SAFETY...
Page 6: ...6 Figure 1 COMPONENT LOCATIONS CONTROL COMPONENTS...
Page 14: ...14 LIGHTING AND OPERATING INSTRUCTIONS NATURAL AND PROPANE FOR HW300 HW399...
Page 15: ...15 LIGHTING AND OPERATING INSTRUCTIONS NATURAL AND PROPANE WITH I I D FOR HW420 UP...
Page 26: ...26 NOTES...