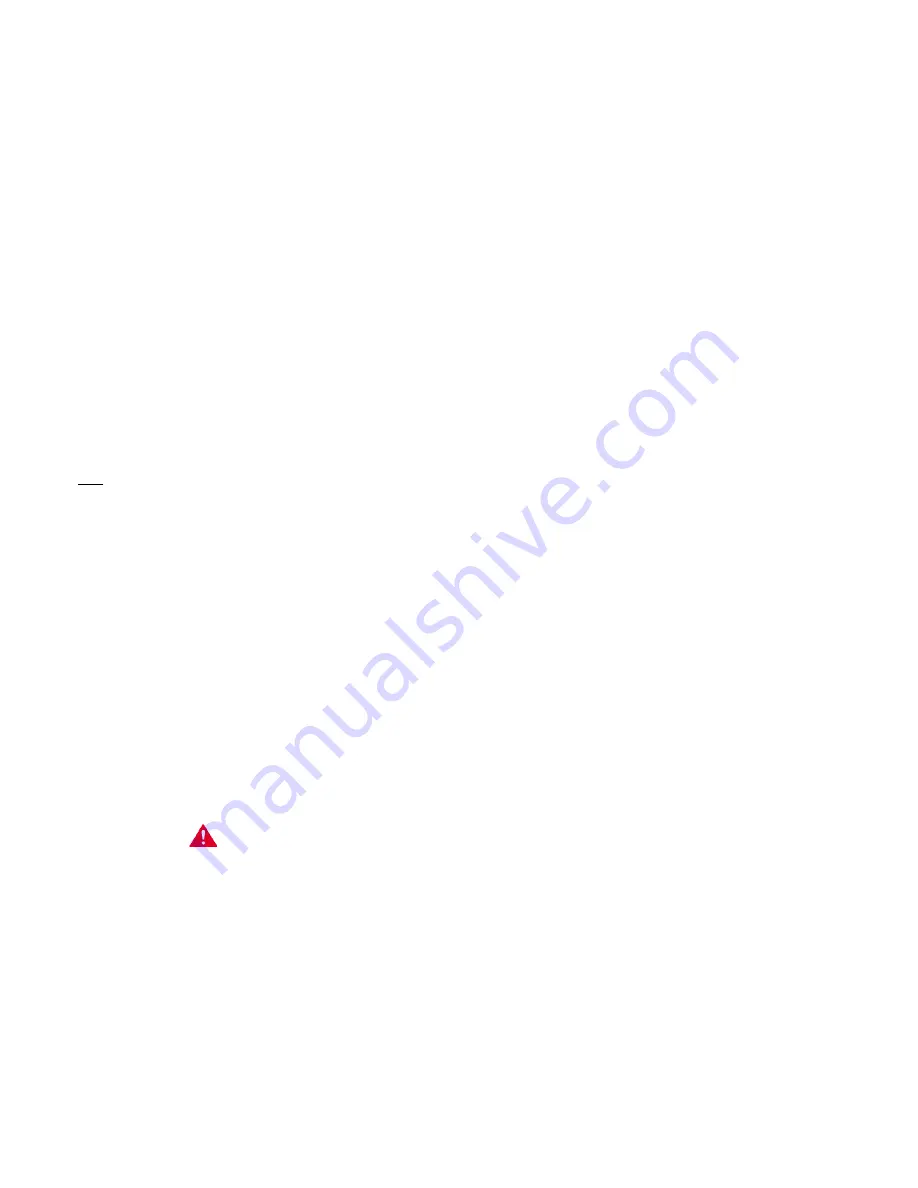
8
If the confined space is within a building of tight construction, air for
combustion, ventilation, and draft hood dilution must be obtained
from outdoors. When directly communicating with the outdoors or
communicating with the outdoors through vertical ducts, two
permanent openings, located in the aforementioned manner, shall
be provided. Each opening shall have a free area of not less than
one square inch per 4000 Btu/hr (551 mm
2
per kw) of the total
input of all appliances in the enclosure. If horizontal ducts are
used, each opening shall have a free area of not less than one
square inch per 2000 Btu/hr (1101 mm
2
per kw)
of the total input of
all appliances in the enclosure.
(B) CANADIAN INSTALLATIONS
Ventilation of the space occupied by the boiler(s) shall be provided
by an opening for ventilation air at the highest practical point
communicating with outdoors. The total cross- sectional area shall
be at least 10% of the area of the combustion air opening but in no
case shall the cross-sectional area be less than 10 square inches
(6500 mm²).
In addition to the above, there shall be permanent air supply
opening(s) having a cross-sectional area of not less than 1 square
inch per 7,000 BTUH (315 mm²/kw) up to and including 1,000,000
BTUH plus 1 square inch per 14,000 BTU (158 mm
2
/kw) in excess
of 1,000,000 BTUH. This opening(s) shall be located at, or ducted
to, a point neither more than 18" (450 mm) nor less than 6 inches
(150 mm) above the floor level.
Where power vented equipment is used in the same room as the
boiler, sufficient air openings must be supplied.
UNDERSIZED OPENINGS MAY RESULT IN INSUFFICIENT AIR
FOR COMBUSTION.
Where an exhaust fan is installed in the same room with a boiler,
sufficient openings for air must be provided in the walls.
UNDERSIZED OPENINGS WILL CAUSE AIR TO BE DRAWN
INTO THE ROOM THROUGH THE CHIMNEY, CAUSING POOR
COMBUSTION. SOOTING MAY RESULT WITH AN INCREASED
RISK OF ASPHYXIATION.
VENTING THE BOILER
WARNING
THE INSTRUCTIONS IN THIS SECTION ON VENTING THE
BOILER MUST BE FOLLOWED TO AVOID CHOKED
COMBUSTION OR RECIRCULATION OF FLUE GASES. SUCH
CONDITIONS CAUSE SOOTING OR RISKS OF FIRE AND
ASPHYXIATION.
SINGLE WALL OR TYPE B VENTING MAY BE USED WITH
THESE BOILERS. ALL LOCAL UTILITY, STATE/ PROVINCIAL,
REGULATIONS ON VENTING MUST BE FOLLOWED.
VENT SIZING, INSTALLATION AND TERMINATION SHALL BE
IN ACCORDANCE WITH PART 7, VENTING OF EQUIPMENT,
OF THE NATIONAL FUEL GAS CODE, ANSI Z223.1, OR SECTION
7, VENTING SYSTEMS AND AIR SUPPLY FOR APPLIANCES,
OF THE CAN/CSA B149, INSTALLATION CODES, OR
APPLICABLE PROVISIONS OF THE LOCAL BUILDING CODES.
1.
DRAFT HOOD
The integral draft hood, louvers or cabinetry must not be altered.
Provision must be made if the boiler is installed in confined space
or a small boiler room to accommodate draft hood spillage and
avoid risks described above. The upper air opening called for in
the AIR REQUIREMENTS section of this manual is for this purpose.
2.
VENT CONNECTION
The minimum distance from adjacent public walkways, adjacent
buildings, openable windows and building openings shall not be
less than those values specified in the National Fuel Gas Code,
ANSI Z223.1 and/or CAN/CSA B149.1-00, Installation Codes:
Stack or chimney must be a minimum height of 12" (305 mm)
above the annual snow fall to prevent blockage.
Building materials must not come in contact with combustion
products from stack or chimney, due to the degrading properties of
flue products.
Materials may be protected from flue products by use of metal or
copper sheeting.
Flue products must have a minimum clearance of 4 feet (1.22 m)
horizontally from, and in no case above or below, unless a 4-foot
(1.22 m) horizontal distance is maintained, from electric meters,
gas meters, regulators and relief equipment.
The Canadian B149.1-00, Installation Code specifies a 6 foot
horizontal vent terminal clearance to gas and electric meters and
relief devices (this clearance is specified as 4 feet in the U.S. under
the National Fuel Gas Code, ANSI/Z223.1). Therefore instruction
provision 1.34.1-b19(d), which specifies compliance with the 4 foot
clearance, as applies in the U.S. only, and the B149.1-00 Installation
Code applies in Canada.
Vent connections must be made to an adequate stack or chimney
and shall be in accordance with Part 7, Venting of Equipment, of
the National Fuel Gas Code, ANSI Z223.1, or Section 7, Venting
Systems and Air Supply for Appliances, of the CAN/CSA-B149.1-
00, Installation Codes, or applicable provisions of the local building
codes. Size and install proper size vent pipe. Do not reduce pipe
size to less than that of the draft hood outlet unless permitted by
local code.
Horizontal runs of vent pipe shall be securely supported by
adequately placed (approximately every 4 feet [1.2 m]),
noncombustible hangers suitable for the weight and design of the
materials employed to prevent sagging and to maintain a minimum
upward slope of 1/4" per foot (21mm/m) from the boiler to the vent
terminals. Dampers or other obstructions must not be installed in
the vent. Be sure that the vent connector does not extend beyond
the inside wall of the chimney.
Where a continuous or intermittent back draft is found to exist the
cause must be determined and corrected. A special vent cap may
be required. If the back draft cannot be corrected by the normal
methods or if a suitable draft cannot be obtained, a blower type
flue gas exhauster may be employed to ensure proper venting and
correct combustion (where permitted by local code). Contact your
A. O. Smith dealer for power vent instructions.