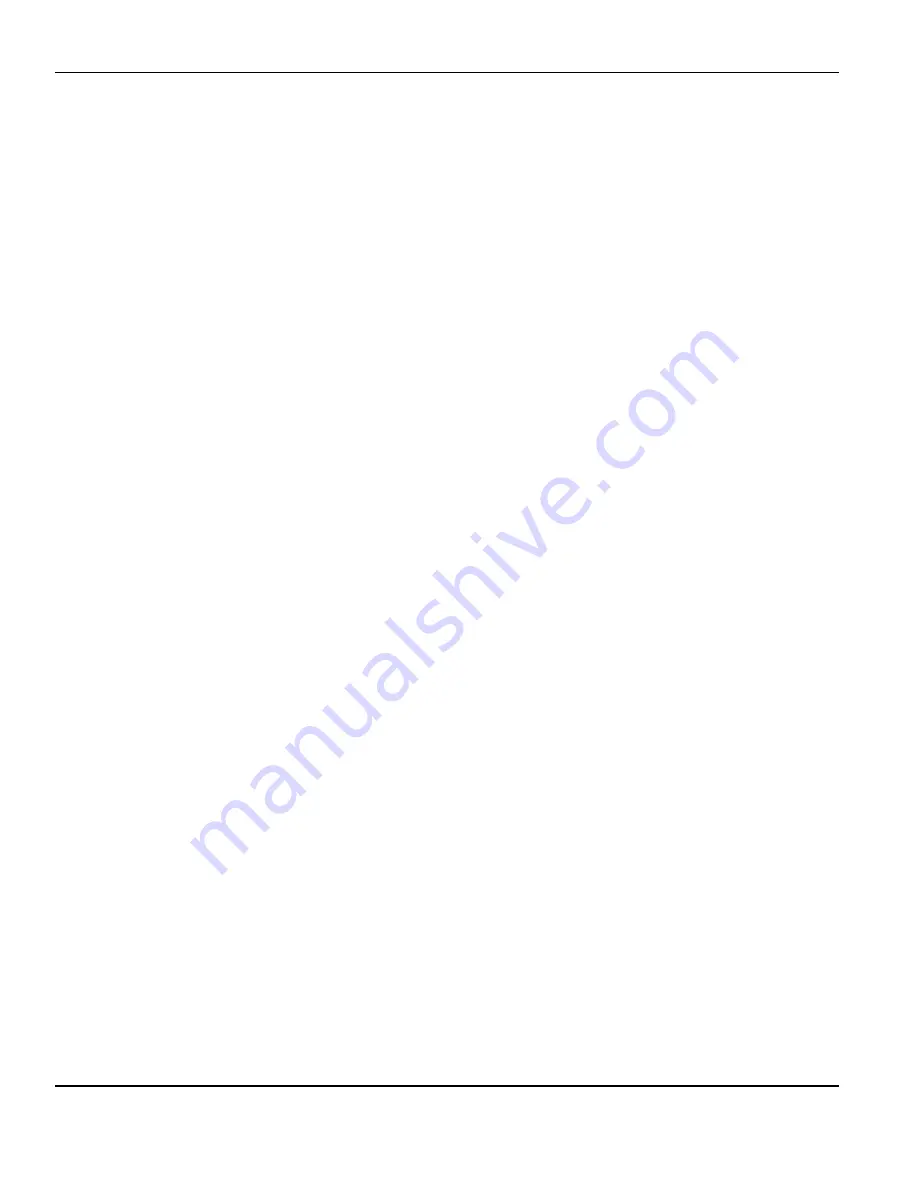
VF BOILER SERVICE MANUAL
AOS WPC - Tech Training
4 of 72
Ashland City, TN © 2007
Servicing should only be performed by a Qualified Service Agent
EMC 5000 MODULATION CONTROL SYSTEM
This portion of the service manual will cover the
EMC 5000
Modulation Control
system
(EMC - Energy Management Control). The EMC 5000 control system includes several
components: a
UIM
(User Interface Module), a
MCB
(Modulation Control Board), and a
PDB
(Power Distribution Board). The EMC 5000 Control System can control single stage,
multiple stage, and modulating boilers and water heaters. This service manual should be
used as a reference for A. O. Smith VW/VB 500-1000 Series 100-101 boilers only.
Features Include:
•
EMI / RFI filtering
- built into all circuit boards. (EMI = Electro Magnetic Interference, RFI
= Radio Frequency Interference) Helps prevent or eliminate erratic operation caused by
EMI/RFI.
•
Help screens
- text based operational information to help the user understand how to
change settings and navigate the menu screens.
•
Self diagnostics
- text based diagnostic information (error and fault messages) on board
to help service technicians quickly and accurately service the boiler.
•
Error message log
- will retain a 9 event history (plus the current event) of error
messages with a time stamp. This will help diagnose load and/or environmental conditions
that may be contributing to a problem with operation or a lock-out.
•
Short cycling protection
- if any stage logs more than 30 cycles in one hour the control
enters a short cycle prevention condition. The boiler will continue to operate in this mode.
The UIM will display and log a “Short Cycle Cond” error message with the yellow Standby
system status LED flashing. The MCB will add a 180 second delay before activating any
stage’s call for heat after the last call for heat during this operating mode.
The short cycle protection mode can be ended (reset) by touching the Select button on the
UIM while the error message is displayed.
•
Temperature probe filtering
- The inlet, outlet, and remote Tank/Loop temperature
probes are read twice per second by the MCB and are filtered for 4 seconds. This filtering
will help prevent rapid short cycling caused by momentary fluctuations in temperature.
•
Pressure/flow switch filtering
- input switches such as air pressure switches are read
every second by the MCB and are filtered (de-bounced) for 6 seconds. This desensitizes
the input signal and will help prevent nuisance error/fault conditions due to momentary
fluctuations caused by wind gusts or blower speed changes. The flow switch is filtered for
4 seconds.
•
Network capability
- multiple boilers can be networked together (daisy chained) with
standard Category 5/6 network cable and given individual network addresses.
•
Access/monitoring with future A. O. Smith EMS
(Energy Management System)
controller.