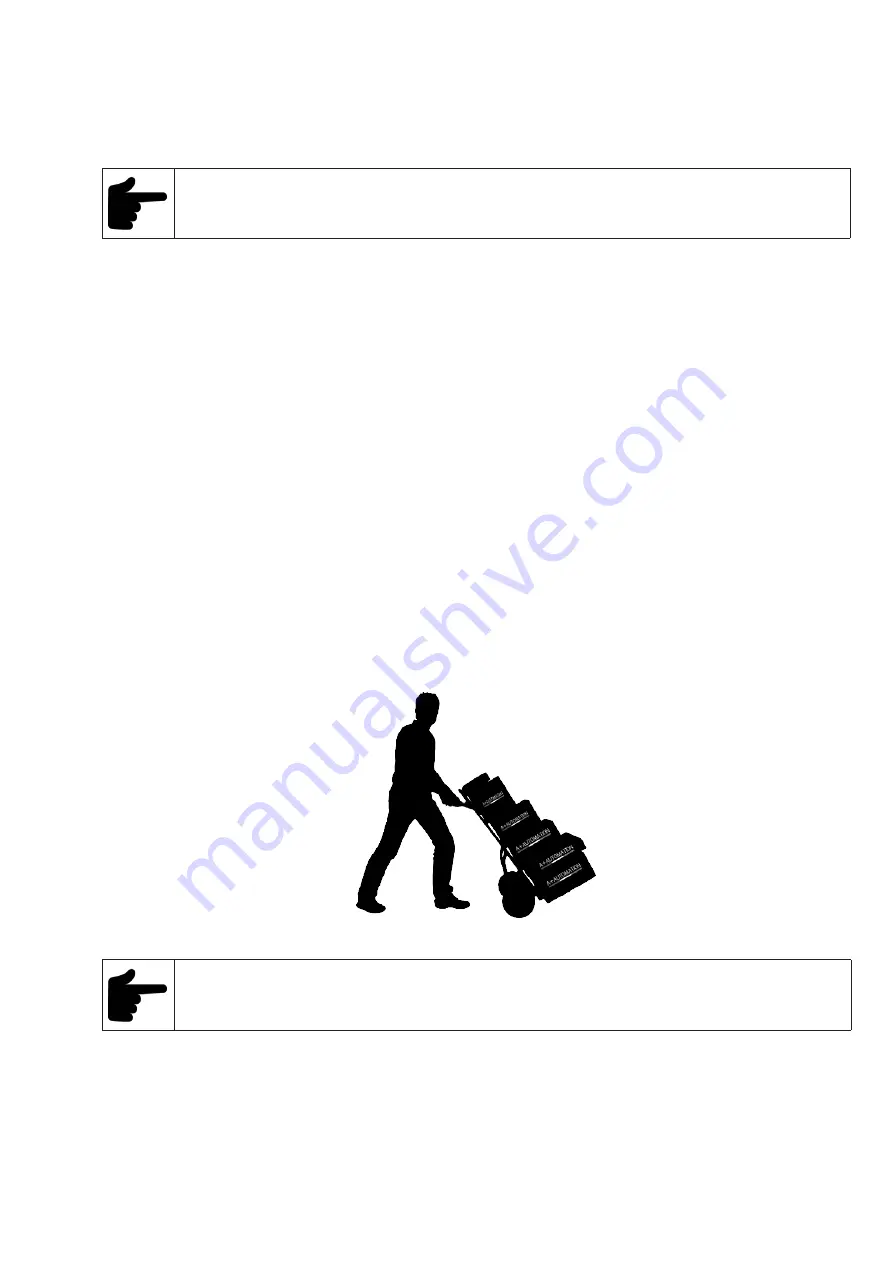
9
A1-M-XL
3.5 SAFE WORKING PROCEDURES
The machine is projected and realized to eliminate any risk connected with its use.
The user is requested to achieve an adequate training to be instructed by their distributor.
The other risks related with working are:
• Finger crushing in the vertical clamp working area
It is necessary to carefully adhere to the following instructions:
• Keep the fingers away from vertical clamp working area
• Keep the foot away from the pedal during machine maintenance.
3.5 RESIDUAL RISKS
During the normal working cycle and while maintenance, the operators are exposed to several residual risks that,
because of operations own nature, can not be totally eliminated.
• Risk of finger crushing due to the presence of vertical clamping
4. INSTALLATION
4.1 HANDLING AND INSTALLATION
The personnel in charge of loading, unloading and moving the machinery must possess the skills and experience
acquired and acknowledged in the specific sector, and must thoroughly know the lifting means to be employed.
The machine has to be shipped in a safe way to avoid any damage to its parts.
• All the protections and guard devices must be properly closed and locked.
• According to the type of shipment, it is necessary to protect the machine from any jarring impact or stress
Picture 4.1A – machine handling indications
Machine total weight: about 50 Kilos / 110 lbs
Lifting must be done by using a specific device.
4.2 WAREHOUSING AND STORAGE PROCEDURES
• In order to avoid that the components cause dangers or are damaged, the storage area must be covered
(preferably a closed area) and accessible only for authorised personnel.
• Avoid corrosive materials that could touch the machine
• Lubricate the parts which are not painted
Summary of Contents for A1-M-XL
Page 3: ...3 A1 M XL...
Page 20: ...20 A1 M XL SCHEMES B Mechanic Schemes A1 M XL P R E L I M I N A R Y...
Page 21: ...21 A1 M XL SCHEMES B Mechanic Schemes A1 M...
Page 22: ...22 A1 M XL...
Page 23: ...23 A1 M XL...
Page 24: ......