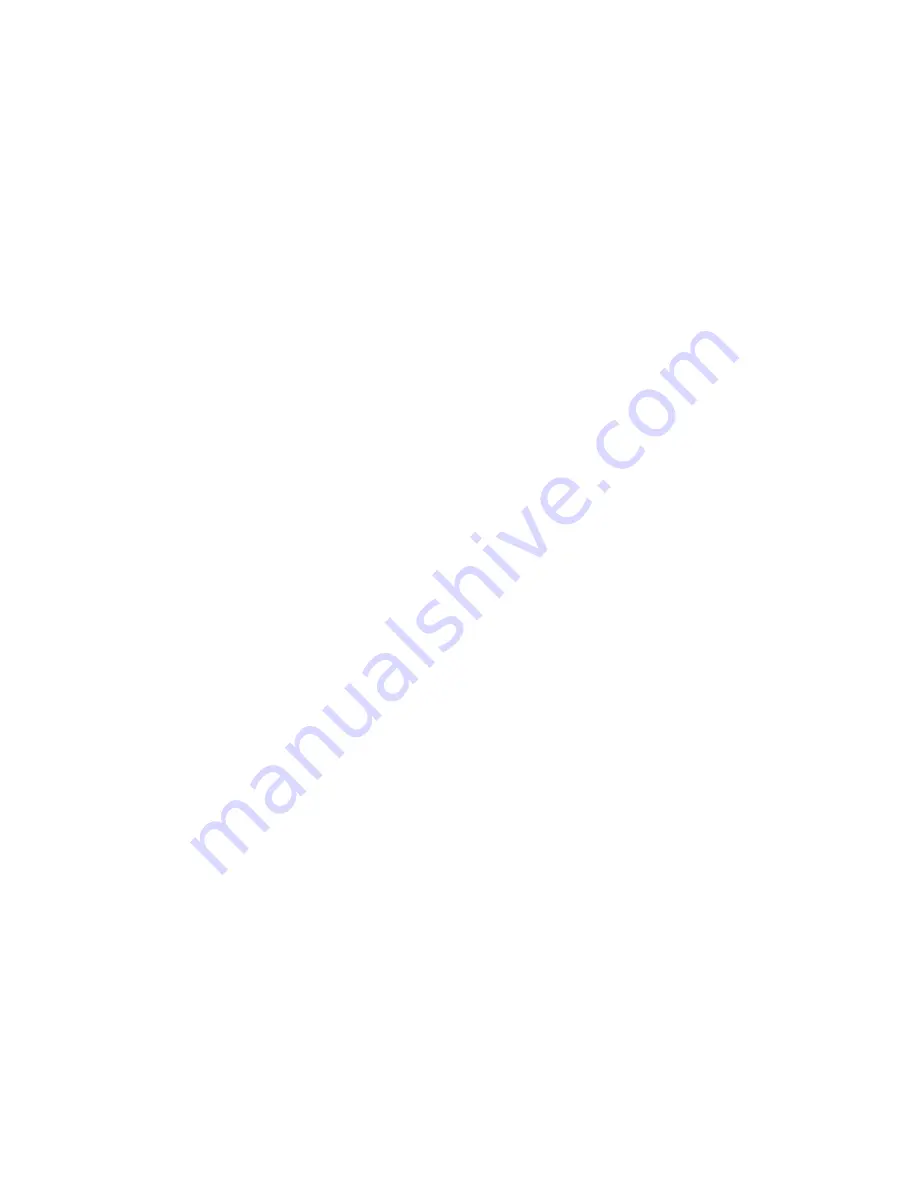
88
The flow rates from the unit are designed for
makeup rates. It is therefore suggested that
the system is back-filled with due precautions
taken to avoid contamination.
Glycol is sometimes subject to bacterial
attack and can become slimy as a result.
AAON recommend the addition of a suitable
biocide. The dosage should be calculated on
the amount of water glycol mixture added
and not the total tank contents. If bacterial
attack occurs on untreated mixtures the unit
should be drained, flushed and refilled with
fresh mixture and dosed with biocide.
Check that the supply voltage and overload
protection is correct.
Guards and covers must not be removed
during operation.
The pipework from the system to the
expansion vessels should not be insulated.
For systems operating above 200°F (93°C),
an anti-gravity loop with a minimum height
of 6 feet, (or an intermediate vessel) should
be installed to provide thermal protection to
the expansion tanks.
The ball float valve is fitted with a low-
pressure seat; a high-pressure seat is attached
to the float valve and should be fitted if
required.
Pressure Switch Adjustment
Low system pressure – PS1
High system pressure – PS2
Duty pump control switch – PS3
Standby pump control switch (where fitted) –
PS4
For each switch, set the delivery to the
required pressure. Then very slowly turn the
adjusting screw on the switch until the
contacts change.
The high system pressure switch should first
be set higher than the required pressure by
turning the screw clockwise and the setting
then made by turning the screw counter-
clockwise
until
the
switch
contacts
changeover.
The other switches should first be set lower
than the required pressure by turning the
screw counter-clockwise and the setting then
made by turning the screw clockwise until the
switch contacts changeover.
A pipe plug is provided on the outlet to allow
connection of a test pump to simulate
differing system pressures to check switch
settings.
The Ultra versions of the GLA have the
capability of controlling duty and standby
pumps from a single pressure switch.
GLA Ultra Settings
The extra functionality of Ultra units is
integral. The only selectable option is Manual
or Automatic reset of alarm conditions. DIP
switch 1, on the display board should be set
to OFF for auto reset (Factory setting), and
ON for manual reset. On alarm conditions,
the MUTE switch will mute the buzzer. In
manual reset mode this MUTE switch will
reset the alarms after the fault condition has
been cleared. Other switches change the
mode of the printed circuit board for use with
other products. For GLA application, all
switches except 1 and 7 must be set to OFF.
Priming the makeup pumps:
1.
Close suction isolating valve.
2.
Fill the glycol-mixing tank.
3.
Remove the upper vent plug from the
makeup pump.
4.
Open suction isolation valve until water
flows out of this tapping.
5.
Close valve and replace plug.
6.
Repeat for standby pump (where fitted).
Summary of Contents for LZ Series
Page 2: ......
Page 27: ...27 Figure 6 Concrete Pad Mounting with Dimensions Figure 7 LZ Base ...
Page 36: ...36 Figure 17 Typical Flue Vent Piping ...
Page 83: ...83 ...
Page 84: ...84 ...
Page 95: ...95 Flo Trex Cross Section ...