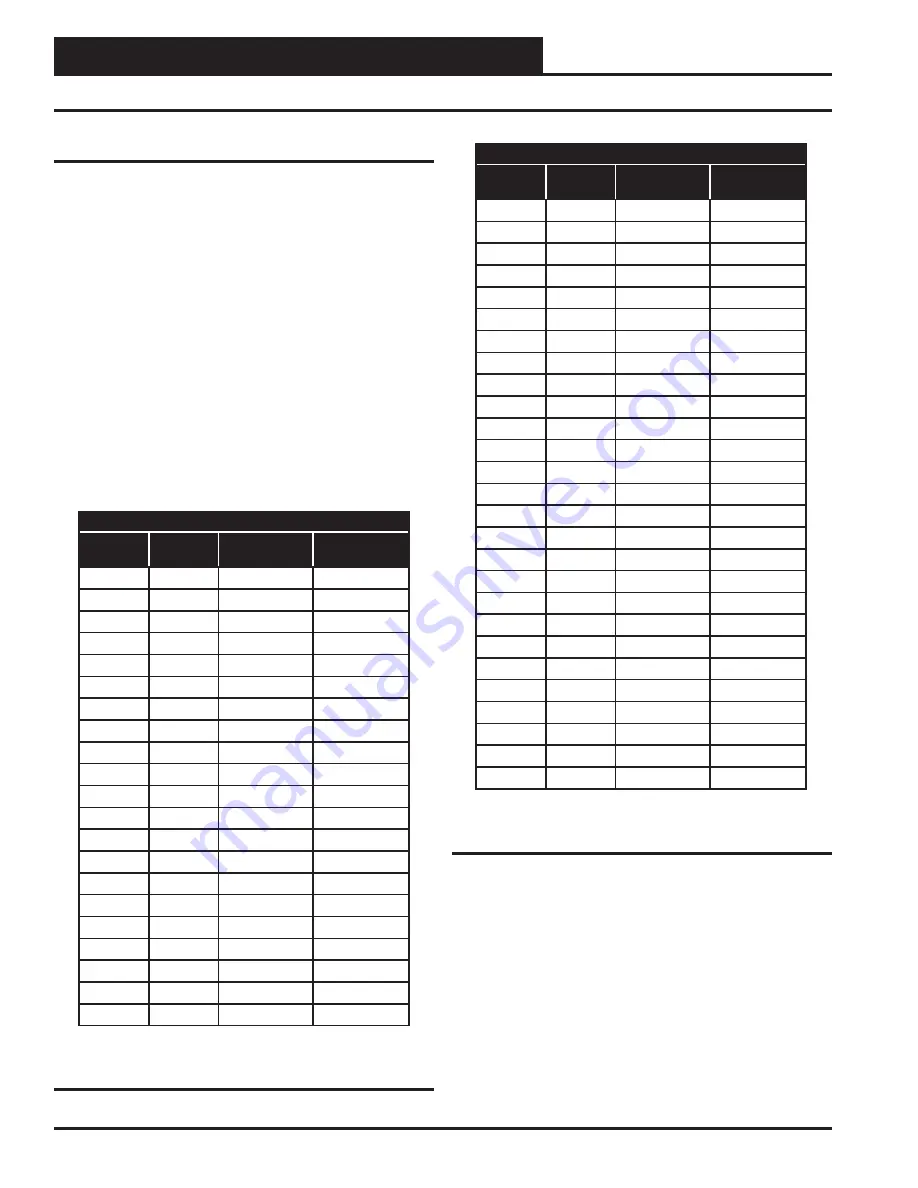
TROUBLESHOOTING
MODGAS-XWR-1 Technical Guide
32
Temperature Sensor Resistance/Voltage Chart
Other Checks
0-3.3V (SAT OPTIONS Jumper Setting 1) &
0-5V (SAT OPTIONS Jumper Setting 2) Supply
Air Temperature Sensor
If you suspect the Supply Air Temperature Sensor is not reading cor-
rectly, make sure the wiring terminal connections are tight and that any
wiring splices are properly connected. You can check the operation of the
Supply Air Temperature Sensor by measuring the resistance or voltage
using a digital multimeter. Set the meter to DC Volts. Place the positive
probe on the AIN terminal and the negative probe on the GND terminal.
Read the DC Volts and fi nd that voltage in
Tables 5 & 6
.
Read the temperature corresponding with that voltage and determine
if this is close to the actual temperature the sensor is exposed to. If the
temperature from the chart is diff erent by more than a few degrees, you
probably have a defective or damaged sensor. You can also check the
sensor resistance to determine correct operation. To read the resistance,
set the meter to Ohms. Unplug the sensor connector from the board and
measure the resistance across the disconnected wires. This resistance
should match the corresponding temperature from
Tables 5 & 6
.
Temperature to Resistance/Voltage Chart
Temp
(
°
F)
Temp
(
°
C)
Resistance
(Ohms)
Voltage @
Input (VDC)
-10
-23.3
93333
2.98
-5
-20.6
80531
2.94
0
-17.8
69822
2.89
5
-15.0
60552
2.83
10
-12.2
52500
2.77
15
-9.4
45902
2.71
20
-6.7
40147
2.64
25
-3.9
35165
2.57
30
-1.1
30805
2.49
35
1.6
27140
2.41
40
4.4
23874
2.33
45
7.2
21094
2.24
50
10.0
18655
2.15
52
11.1
17799
2.11
54
12.2
16956
2.08
56
13.3
16164
2.04
58
14.4
15385
2.00
60
15.6
14681
1.96
62
16.7
14014
1.93
64
17.8
13382
1.89
66
18.9
12758
1.85
Temperature to Resistance/Voltage Chart
Temp
(
°
F)
Temp
(
°
C)
Resistance
(Ohms)
Voltage @
Input (VDC)
68
20.0
12191
1.81
69
20.6
11906
1.79
70
21.1
11652
1.78
71
21.7
11379
1.76
72
22.2
11136
1.74
73
22.7
10878
1.72
74
23.3
10625
1.70
75
23.9
10398
1.68
76
24.4
10158
1.66
78
25.6
9711
1.63
80
27.8
9302
1.59
82
27.8
8893
1.55
84
28.9
8514
1.52
86
30.0
8153
1.48
88
31.1
7805
1.45
90
32.2
7472
1.41
95
35.0
6716
1.33
100
37.8
6047
1.24
105
40.6
5453
1.16
110
43.3
4923
1.09
115
46.1
4449
1.02
120
48.9
4030
.95
125
51.7
3656
.88
130
54.4
3317
.82
135
57.2
3015
.76
140
60.0
2743
.71
145
62.8
2502
.66
Table 5: 0-3.3 V Temperature Sensor - Voltage &
Resistance for Type III Sensors
Table 5, continued: 0-3.3 V Temperature Sensor -
Voltage & Resistance for Type III Sensors
Thermistor Sensor Testing Instructions
1.) Use the resistance column to check the thermistor sensor while dis-
connected from the controllers (not powered).
2.) Use the voltage column to check sensors while connected to powered
controllers. Read voltage with meter set on DC volts. Place the “-” (mi-
nus) lead on GND terminal and the “+” (plus) lead on the sensor input
terminal being investigated.
If the voltage is above 3.3 VDC, the sensor or wiring is “open.” If the
voltage is less than 0.05 VDC, the sensor or wiring is shorted.