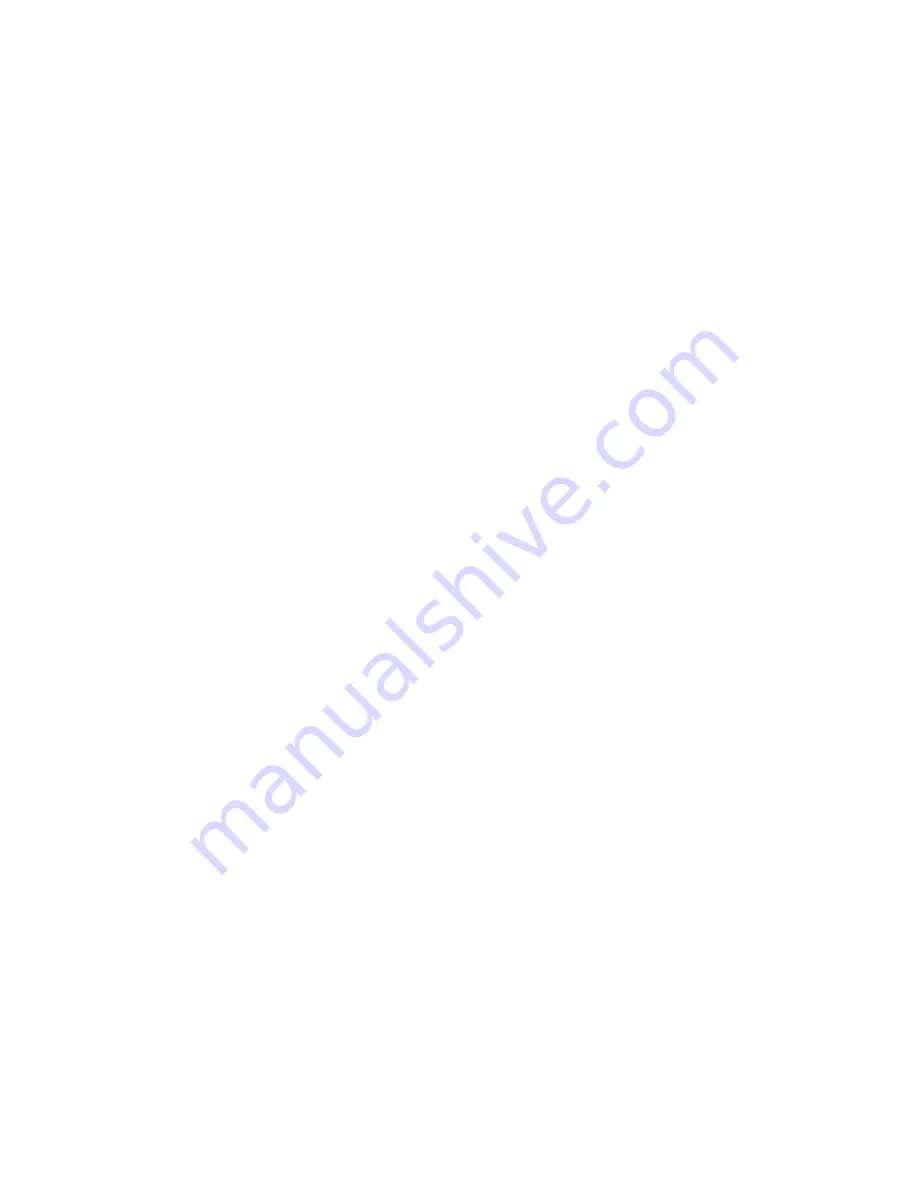
13
1.
Startup and service must be performed by
a Factory Trained Service Technician.
2.
Use only with type of the gas approved
for the furnace. Refer to the furnace rating
plate.
3.
The unit is for outdoor use only. See
General Information section for more
information.
4.
Provide adequate combustion ventilation
air to the furnace. If a vent duct extension
is used, a class III approved vent is
required. See the Locating Units and Gas
Heating sections of the Installation
section of the manual.
5.
Always install and operate furnace within
the intended temperature rise range and
duct system external static pressure (ESP)
as specified on the unit nameplate.
6.
The supply and return air ducts must be
derived from the same space. It is
recommended ducts be provided with
access panels to allow inspection for duct
tightness. When a down flow duct is used
with electric heat, the exhaust duct must
be an L shaped duct.
7.
Clean furnace, duct and components
upon completion of the construction
setup. Verify furnace operating
conditions including input rate,
temperature rise and ESP.
8.
Every unit has a unique equipment
nameplate with electrical, operational,
and unit clearance specifications. Always
refer to the unit nameplate for specific
ratings unique to the model you have
purchased.
9.
READ THE ENTIRE INSTALLATION,
OPERATION AND MAINTENANCE
MANUAL. OTHER IMPORTANT
SAFETY PRECAUTIONS ARE
PROVIDED THROUGHOUT THIS
MANUAL.
10.
Keep this manual and all literature
safeguarded near or on the unit.
Summary of Contents for RQ NextGen Series
Page 2: ......
Page 26: ...26 Figure 3 RQ Cabinet Standard and Power Exhaust Gasket Locations...
Page 40: ...40 Figure 23 Post Corner Hole Piping Figure 24 Post Back Hole Piping...
Page 88: ...88 Gas Heater Operating Instructions Figure 36 Gas Heater Instructions...
Page 95: ...95...
Page 96: ...96...
Page 105: ...105 Maintenance Log E Coated Coil...
Page 107: ...107...