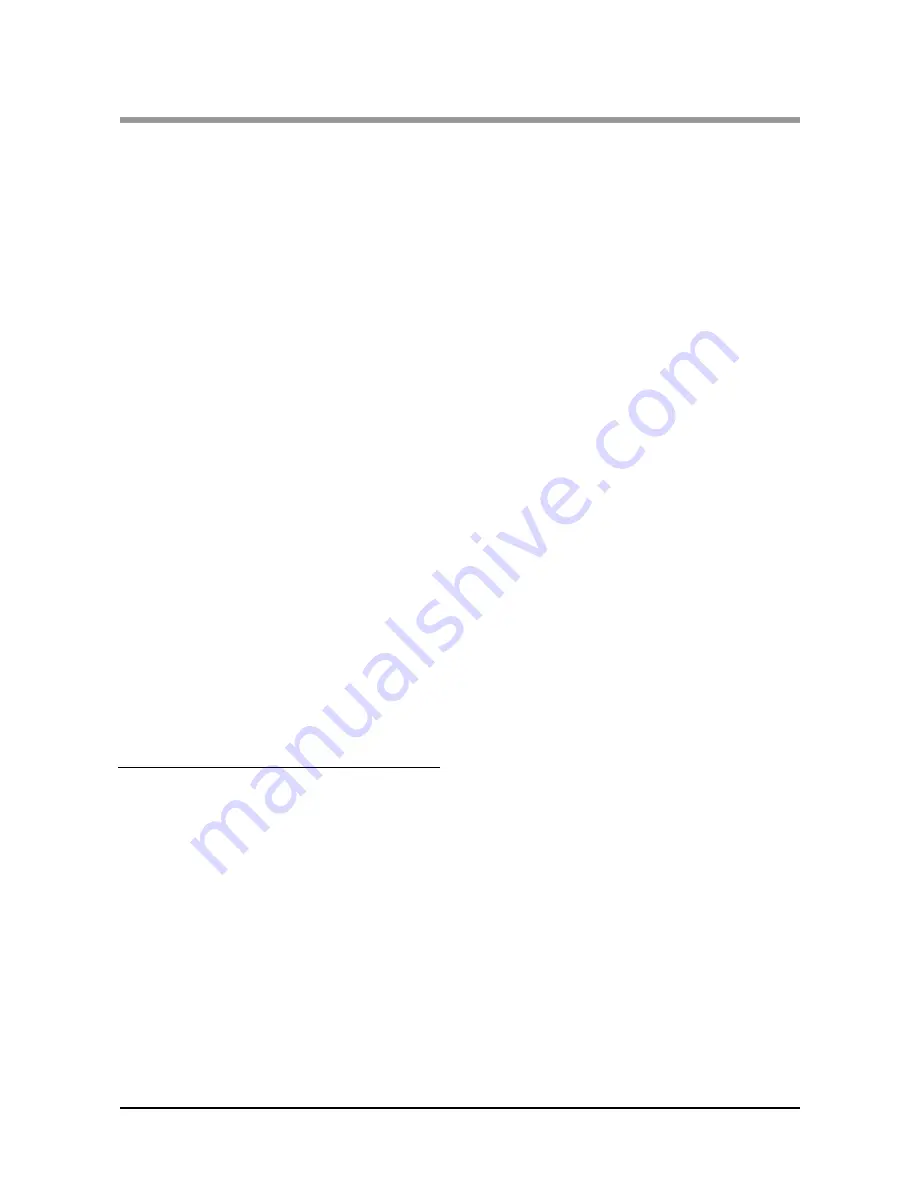
Stratford Tf & Ti Boiler Multifuel Stoves
19
INSTALLATION
INTEGRAL BOILERS
Integral boilers should be connected, with flow and
return connection of any circuit on opposite sides
of the appliance, (cross flowed), to an indirect hot
water tank/system, adding Fernox or similar
corrosion inhibitor to prevent corrosion and the
formation of lime scale.
It is also essential that the return water temperature
remains in excess of 45 degrees centigrade
(Celsius). The gravity return should be fitted with a
thermostat, which will activate a cut-out on the
radiator circulating pump, should the temperature
drop below this level.
Connect pipe work to the boiler unit.
The connected pipes should be screwed to a
maximum depth of 15mm from the face of the
tapping, (female 1" B.S.R). Steel integral boilers
should be connected to an indirect hot water tank
system.
Note: the flow and return sections of any circuit
must always be opposite of appliance. Remember
to incorporate a draining plug/tap at the lowest
point to facilitate drainage & flushing.
Warning: if a pipe stat is not fitted then cold
water corrosion can occur.
FAILURE TO COMPLY WITH THESE
REQUIREMENTS WILL INVALIDATE THE
GUARANTEE
CHECKING THE THERMOSTAT
AND PRESETTING
TO THE
CORRECT DAMPER PRESSURES
PLEASE NOTE:
THE THERMOSTAT HAS
BEEN FITTED AND CORRECTLY SET AT
MANUFACTURE. SO THE FOLLOWING
PROCEDURES WILL ONLY BE REQUIRED
WHEN REPLACING OR RE SETTING THE
THERMOSTAT.
To fit/remove thermostat on Tf models
For fitting/removal of thermostat on Ti models
please see page 20.
1. Pull thermostat knob off of the shaft.
2. Remove access cover plate, use a No. 2 Pozi
screw driver and remove the 2no. CSK M5 screws.
3. Remove the 2no. M5 screws that secure the
thermostat housing. The thermostat is now free, and
you will be able to remove the spacer bracket.
4. On the rear of the stove, remove the thermostat
sensor from its pocket and push this carefully
through the hole in the corner cut-out of the stove.
Take care not to kink the copper tube.
5. Withdraw the thermostat from the apperture.
6. If you are fitting a new thermostat you will need
to remove the knob extension shaft. Use a 7mm
spanner. To remove the M4 Grub screw.
7. Re-fit is the reverse of the above process. Please
ensure the spacer bracket is secured beneath the
thermostat as in point 3.
See below if adjustment is required.
ADJUSTMENT OF THE
THERMOSTAT
However, it is advisable to check the cold setting
distance prior to lighting a fire in it. With the
control set at maximum there should be a gap of
23mm between the fire and the edge of the damper
plate furthest from the control shaft. If this is not
the case adjust by slackening off the lock nut and
turning the adjusting nut on the damper plate.
When the cold setting distance has been correctly
set re-tighten the lock nut.