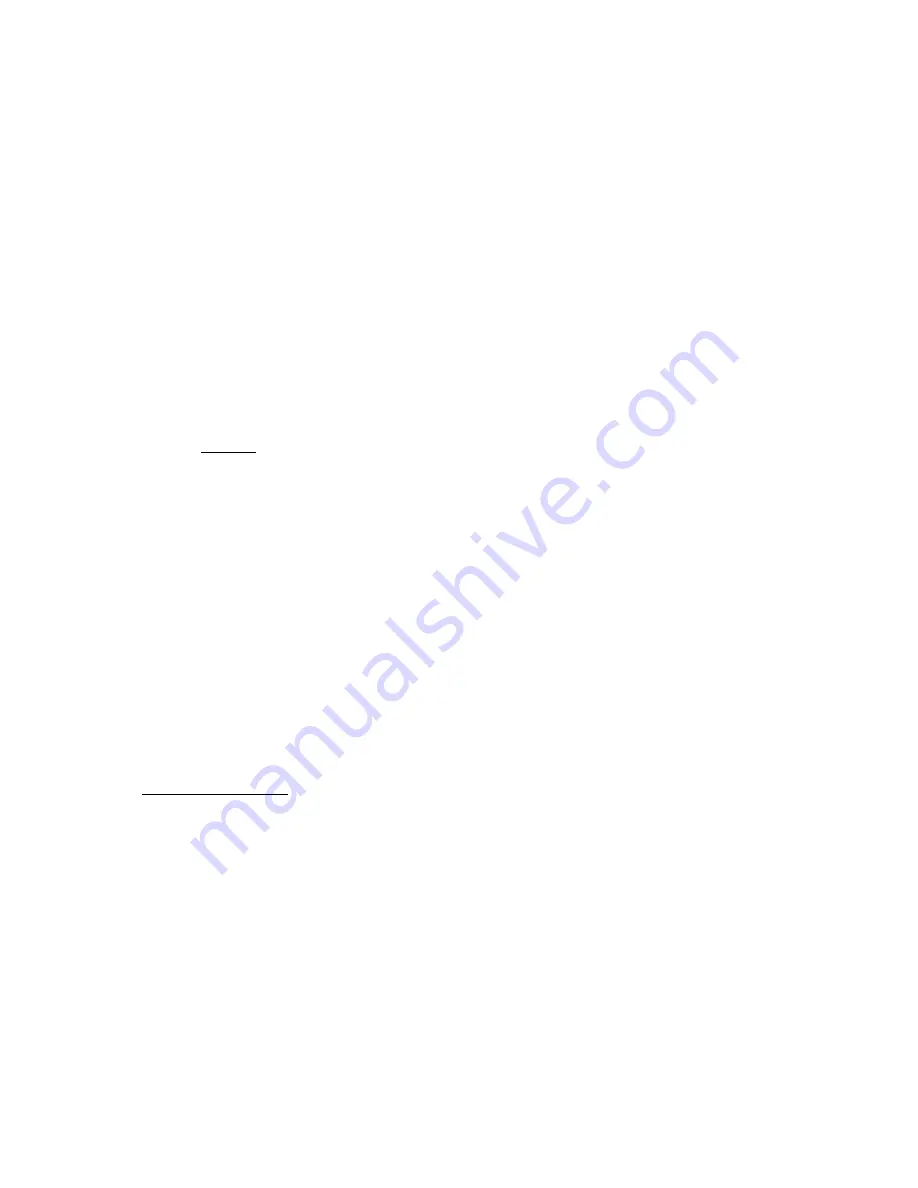
3
STANDARD AIR CLEANING STAGES (FILTERS SUPPLIED WITH THE UNIT)
The PRED750 and PRED750EC models come equipped with two progressively efficient pre-filters mounted in the
pre-filter compartment, and a final stage HEPA filter, located inside the cabinet:
•
The first-stage 1" deep, coarse particulate pre-filter (F621) is designed to capture particles 100 microns
or larger.
•
The second-stage 2" deep, particulate pleated pre-filter (H502) is designed to capture particles 10
microns or larger.
•
Each HEPA filter (H161606-99) is tested & certified to capture at least 99.97% (9,997 out of 10,000) 0.3-
micron particles.
Note: The particulate filters included with this unit do not remove odors, vapors or gases, including volatile
organic compounds.
ALTERNATE SECOND STAGE FILTER: VAPOR-LOCK® CARBON FILTER
(MUST BE PURCHASED SEPARATELY)
Vapor-Lock® pleated, high-capacity, carbon filters (part # VL1002) are available for capturing OVG. This 2"-deep
filter can be used in place of the second-stage H502 pleated pre-filter to reduce airborne OVG by chemically
bonding the OVG molecules to the surface area of the carbon granules, via a process known as adsorption. The
VL1002 filter also provides a similar level of particulate filtration efficiency to the H502 pre-filter.
Effective carbon adsorption is dependent upon the amount of carbon & exposed carbon granule surfaces, and
the dwell (contact) time the OVG molecules have with the carbon granules. Operating the unit at lower speed
settings to increase dwell time can therefore improve OVG adsorption, though it is highly unlikely that all of the
OVG will be removed in one pass of air through the unit. Operating the unit in the recirculation mode can
increase effectiveness, by exposing OVG particles to multiple– passes through the Vapor-Lock filter.
It is almost impossible to provide accurate estimates to two commonly asked questions: “how much time will it
take to capture all of the OVG?”, and “how do I know when a carbon filter should be replaced?” Unfortunately,
unknown factors, such as concentration levels, fresh-air intake volume, temperature, and humidity prevent
establishment of any more accurate ‘rule of thumb’ than one’s sense of smell. Since off-gassing of adsorbed
OVG can occur when the adsorption capacity of the filter is reached, replace the carbon filter as soon as odor
breakthrough is sensed. More detailed information on carbon adsorption can be found in an article titled:
“Activated Carbon: How Is It Used? How Does It Work?”
which can be found on the Abatement Technologies
website, www.abatement.com.
HOW TO DETERMINE THE REQUIRED NUMBER OF AIR FILTRATION DEVICES (AFD)
1.
Calculate the total air volume (V) in cubic meters (ft³) within the enclosed containment area by
multiplying the length (L) x the width (W) x the height (H), all in meters (V = L x W x H).
2.
Determine the minimum number of air changes per hour (ACH) specification. When no ACH number is
specified, most users target at least 6 ACH for construction areas. Building in a safety factor to
compensate for filter loading, duct losses, reduced voltage and other factors that can reduce actual
installed airflow is a good practice. For example, if 6 ACH is the objective, you might design for 8 ACH.
3.
Select an Abatement Technologies air filtration device (AFD) model and determine the peak airflow
rating for that model in cubic feet per minute (CFM).
4.
Determine the total number of AFD required using the following formula: Quantity = (V x Design ACH) /
(AFD Rating x 60)
5.
Always round up to the next whole number. For example, if the total number of AFD required is 2.13, 3
units are recommended, not 2.