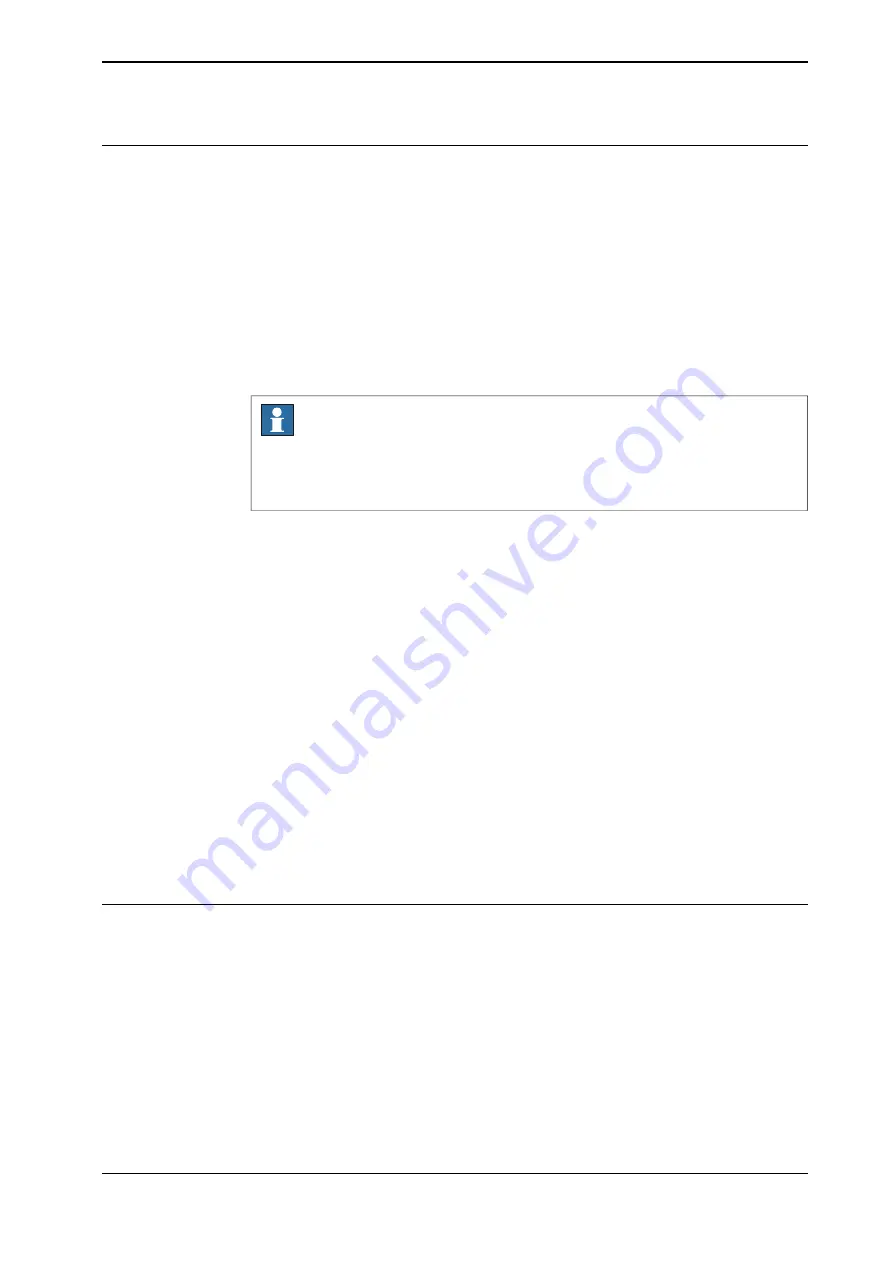
Routines in the calibration procedure
The following routines are available in the Axis Calibration procedure, given at the
beginning of the procedure on the FlexPendant.
Fine calibration routine
Choose this routine to calibrate the robot when there are no tools, process cabling
or equipment fitted to the robot.
Reference calibration routine
Choose this routine to create reference values and to calibrate the robot when the
robot is dressed with tools, process cabling or other equipment.
Also choose this routine if the robot is suspended.
Note
When calibrating the robot with the reference calibration routine, the robot must
be dressed with the same tools, process cabling and any other equipment as
when the reference values were created.
If calibrating the robot with reference calibration there must be reference values
created before repair is made to the robot, if values are not already available.
Creating new values requires possibility to move the robot. The reference values
contain positions of all axes, torque of axes and technical data about the tool
installed. A benefit with reference calibration is that the current state of the robot
is stored and not the state when the robot left the ABB factory. The reference value
will be named according to tool name, date etc.
Follow the instructions given in the reference calibration routine on the FlexPendant
to create reference values.
When reference calibration is performed, the robot is restored to the status given
by the reference values.
Update revolution counters
Choose this routine to make a rough calibration of each manipulator axis by
updating the revolution counter for each axis, using the FlexPendant.
Validation
In the mentioned routines, it is also possible to validate the calibration data.
System containing SafeMove/EPS
SafeMove/EPS
SafeMove will lose its synchronization to the controller if a new calibration is done.
New calibration values have to be downloaded to SafeMove, and a new
SafeMove/EPS calibration has to be done. Make sure that the user rights admit to
change the safety settings and to synchronize SafeMove/EPS.
Continues on next page
Product manual - IRB 4600
349
3HAC033453-001 Revision: Y
© Copyright 2009-2021 ABB. All rights reserved.
5 Calibration
5.4.1 Description of Axis Calibration
Continued
Summary of Contents for IRB 4600
Page 1: ...ROBOTICS Product manual IRB 4600 ...
Page 8: ...This page is intentionally left blank ...
Page 334: ...This page is intentionally left blank ...
Page 368: ...This page is intentionally left blank ...
Page 376: ...This page is intentionally left blank ...
Page 390: ...This page is intentionally left blank ...
Page 392: ...This page is intentionally left blank ...
Page 398: ......
Page 399: ......