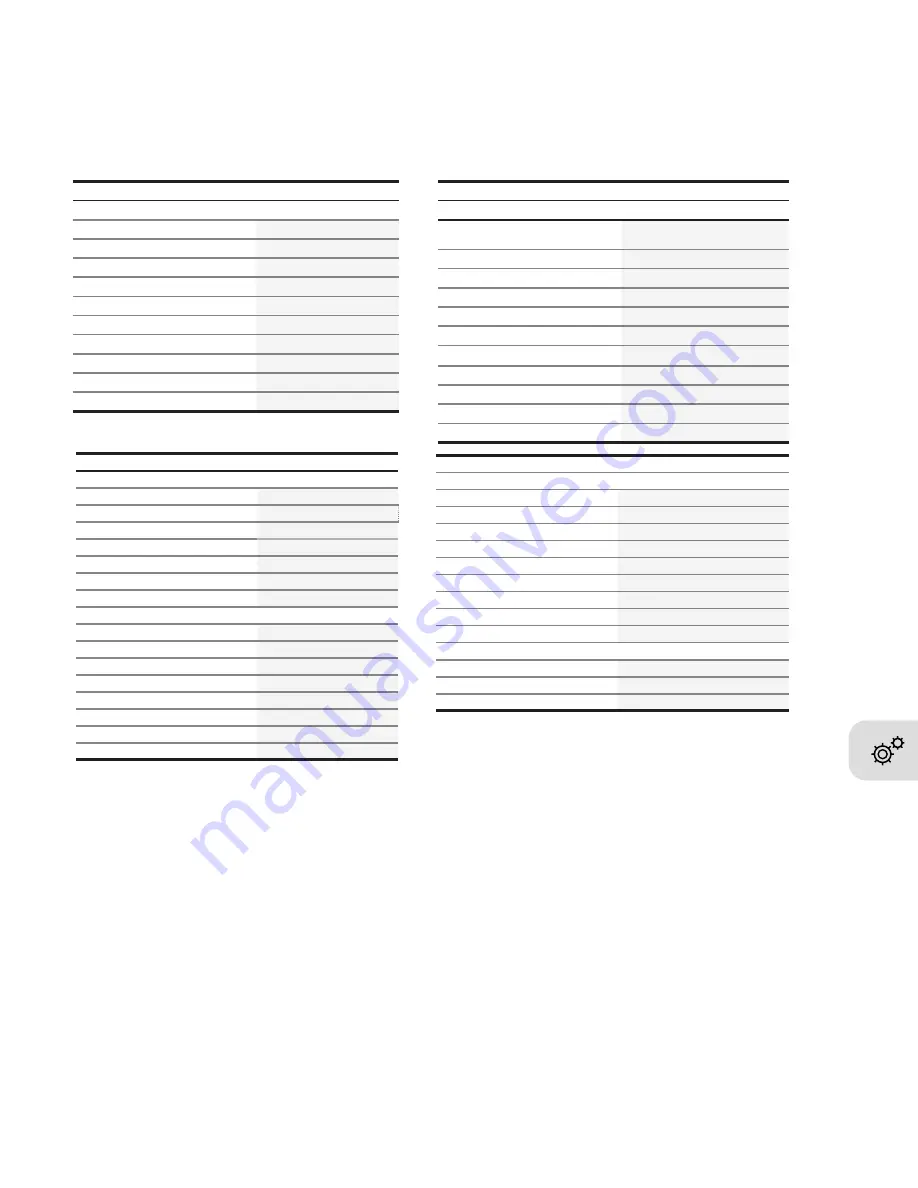
LVD-EOMU02U-EN REVD 11/2022
13
3.5 Setup, data mapping and typical parameters for ACH580 and ACH580 E-Clipse bypass
ACH580
ACH580 E-Clipse
Drive Parameter
ACH580 E-Clipse
Setup parameters
16.01 Start/Stop
(bypass parameter)
Comm
20.01 Start/Stop EXT 1
Embedded fieldbus
22.11 Vector Speed Ref
EFB ref1
28.11 Scalar Speed Ref
EFB ref1
58.01 Comms Protocol
Modbus RTU***
58.03 Node Address
Drive 1,2..up to 5 *
58.04 Baud Rate
38.4 kbps***
58.05 Parity
8 EVEN 1***
58.14 Comm Loss Action
Warning
58.15 Comm Loss Mode
Any Message
58.17 Transmit Delay**
0
*58.03 Node Address corresponds to the VFD-GATEWAY Node Settings (see VFD-GATEWAY Settings Web Interface)
**It is recommended to set this to 0 to avoid adding delays to the data
***The VFD-GATEWAY only supports these default settings
**** 58.107 - 58.112 are set in Hex format in the E-Clipse. The drive parameter group number, and number in the group, make up two separate hex
numbers that are combined. Example: parameter 47.21: 47 (decimal) = 2F (Hex), 21 (decimal) = 15 (Hex). Combining 2F and 15 Hex together gives
2F15 that is entered into E-Clipse parameters 58.107 - 58.112.
For ACH580 the write data starts at 58.108 and First 7 registers must be reads (58.101-58.107)
For ACH580 E-Clipse the first 4 registers are pre-mapped as CW, Ref 1, Ref 2, and SW. The next 8 registers are all reads. The first 2 of those reads are
fixed at Speed or Frequency (dictated by scalar vs vector selection). The next 6 are customizable. The 3 words out are (CW, Ref 1, and Ref 2). The 9
words in are (1: SW, 2: output frequency, 3: output frequency, 4 - 9: E-Clipse parameters 58.107 - 58.112 settings).
Note: You MUST set 58.06 to refresh settings after all parameters in group 58 are set.
Note: ACH580
E-Clipse power must be cycled for changes to take effect
ACH580 E-Clipse typical parameters
READ from VFD
Fixed word 4
Status Word
Fixed word 5
Speed or Freq
Fixed word 6
Speed or Freq
58.107 Data I/O 7****
107 Motor Current (107 Hex)
58.108 Data I/O 8****
111 DC Bus Voltage (10B Hex)
58.109 Data I/O 9****
103 Output Freq (103 Hex)
58.11 Data I/O 10****
114 Motor Power (10F Hex)
58.111 Data I/O 11****
47.21 Data Storage (2F15 Hex)
58.112 Data I/O 12****
47.22 Data Storage (2F16 Hex)
WRITE to VFD
Fixed word 1
Control Word
Fixed word 2
REF 1
Fixed word 3
REF 2
Drive Parameter
Example for ACH580
Setup parameters
20.01 Start/Stop EXT 1
Embedded fieldbus
22.11 Vector Speed Ref
EFB ref1
28.11 Scalar Speed Ref
EFB ref1
58.01 Comms Protocol
Modbus RTU***
58.03 Node Address
Drive 1,2..up to 5 *
58.04 Baud Rate
38.4 kbps***
58.05 Parity
8 EVEN 1***
58.14 Comm Loss Action
Warning
58.15 Comm Loss Mode
Any Message
58.17 Transmit Delay**
0
ACH580 typical parameters
READ from VFD
58.101 Data I/O 1
Status Word 16 bit
58.102 Data I/O 2
Act 1 16 bit
58.103 Data I/O 3
Act 2 16 bit
58.104 Data I/O 4
1.07 Motor Current
58.105 Data I/O 5
1.11 DC Bus Voltage
58.106 Data I/O 6
1.01 Motor Speed
58.107 Data I/O 7
1.14 Motor Power
Write to VFD
58.108 Data I/O 8
Control Word 16 bit
58.109 Data I/O 9
Ref 1 16 bit
58.11 Data I/O 10
Ref 2 16 bit
58.111 Data I/O 11
47.21 Data Storage
58.112 Data I/O 12
47.22 Data Storage
58.113 Data I/O 13
47.23 Data Storage
58.114 Data I/O 14
47.24 Data Storage
58.06 Comm Control
Refresh Settings