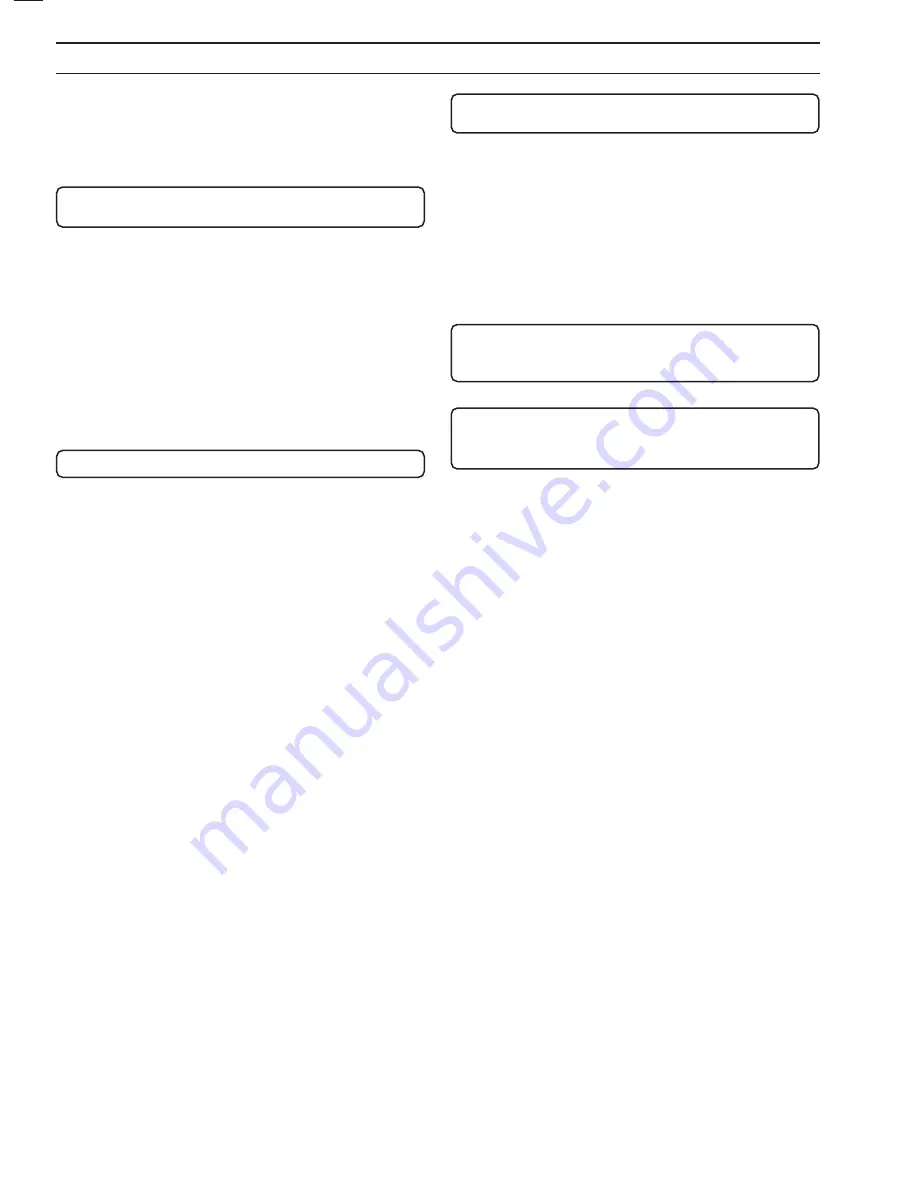
30
…8 MAINTENANCE
d) Check liquid levels in the reagent and standard solution
containers.
e) Check for malfunction indications on the instrument
display.
Note.
The mains and pump/heater switches are situated
on the right hand side of the User Junction Box.
8.2.2
Four Weekly
a) Inspect all tubing and flowcell for leaks or deterioration,
and for signs of accumulation of solid deposits.
b) Clean monitor pipework if there are signs of algae visible.
c)
Check the level of the filling solution in the probe and
top-up if necessary.
d)
Discard old reagent and standard solutions. Clean
containers thoroughly before refilling with fresh solutions –
see Section 8.1.
Note.
It is vital that the containers are not topped up.
e) Examine the sample input pipe for leaks and deterioration.
f)
Ensure the drain is in good order and free from obstruction.
8.2.3
Two Monthly
Refurbish the probe – see Section 8.2.7.
8.2.4
Twelve Monthly
a) Service pump, tubing and capstans – see Section 8.2.8.
b) Replace all internal plumbing tubing – see Section 8.2.9.
c) Carry out the normal 4 weekly schedule not already
covered above.
8.2.5
Cleaning Sample Pipework
A common problem in measuring water samples from rivers,
treatment works, etc., is the presence of bacteriological
growth in the sample.
In the form of algae it creates a problem by growing inside
tubing supplying sample to analysers, as well as in the
monitors and associated ABB Kent-Taylor Ultrafilters, if used.
If severe, this growth may cause blockages in tubing or valves
and/or fouling of flowcells and sensors.
In addition, the algae may affect the concentration of the
measured parameter in the sample. This is particularly severe
in ammonia monitors, where algal growth in supply lines
causes 'ammonia stripping' and a reduction in the measured
concentration. Other parameters, however, may also be
affected.
It is therefore essential to maintain sterile conditions. This
requires periodic cleaning, at a frequency dependent on
sample conditions. It is suggested that a regular maintenance
programme is introduced, rather than wait for visible signs of
the presence of algal growth.
Note.
Once growth is visible the problem is already
serious.
The recommended agent for cleaning tubing and pipework is
sodium hypochlorite solution containing about 0.1%
(1000 mg l
–1
) available chlorine.
Cleaning Solution
To prepare 500 ml of cleaning solution, dilute 5 ml of
concentrated sodium hypochlorite (NaOCl) solution
(containing approximately 10% available chlorine) with de-
ionised water and make up to 500 ml with more de-ionised
water.
Note.
The solution is unstable. Make only enough for
immediate requirements and discard any surplus after
use.
Warning.
Sodium hypochrorite is an irritant. Contact with
acids liberates toxic gas. Avoid contact with skin and eyes.
If contact occurs, wash with plenty of clean water.
Method
Where an Ultrafilter is used, clean according to the manual
with a 0.05% (500 mg l
–1
) chlorine solution (i.e. half the
concentration of the above solution). Tubing between the
Ultrafilter and the analyser should also be flushed through,
along with the constant head tank.
a) Remove sensors for short-term storage before cleaning –
see Section 8.3.1
b) Remove the reagent and calibration solution take-up tubes
from their respective containers. Fill a calibration container
with the sodium hypochlorite cleaning solution, place it in
the calibration container recess and immerse the take-up
tubes in the solution.
c) Operate 'Cal' to initiate a calibration sequence to draw the
solution through the solenoid valves tubing and flowcell.
d) Remove any dislodged debris from the flowcell and clean
the constant-head unit with the cleaning solution using the
bottle brush provided. The tube between the constant-
head unit and SV1 can be cleaned with the cleaning
solution using the syringe.
e) Repeat the process using high purity water to flush out the
sodium hypochlorite solution.
If, after cleaning, there are still signs of discoloration or
deposits in the monitor tubing, it should be discarded and
replaced with new tubing throughout. In cases where the
monitor tubing is blocked or very heavy deposits are found, it
may be necessary to simply replace the tubing without
attempting to clean it.