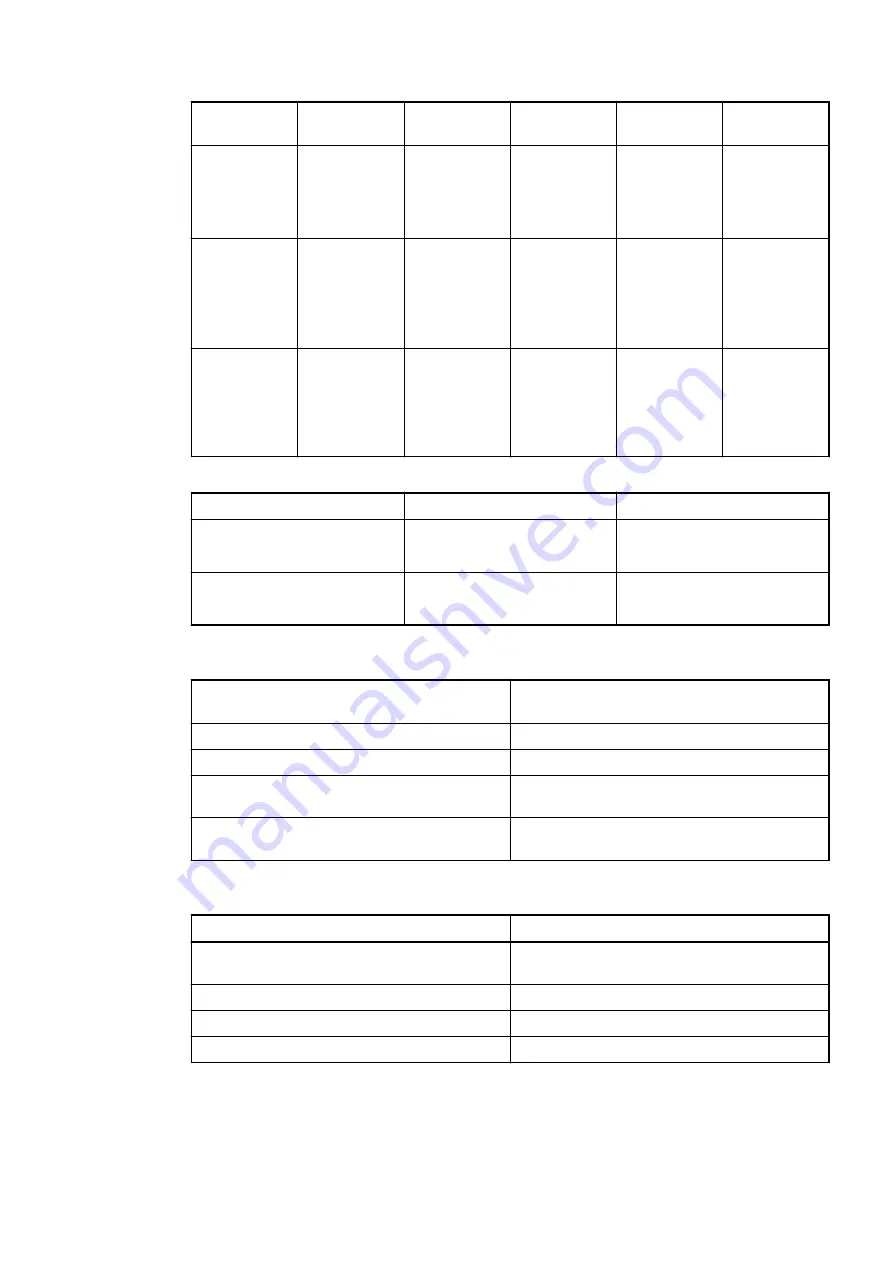
No.
Name
Value
Internal value Internal
value, type
Default
1
Channel con-
figuration
see below
see below
Byte
see below
2
Channel mon-
itoring
see below
see below
*
8)
Byte
see below
3
Substitute
value
0...65535
0...
0xffff
Word
0
No.
Name
Internal value, type
1
Channel configuration
see table
3
)
Byte
2
Channel monitoring
see table
4
)
Byte
Table 97: Channel configuration
3
)
Internal value
Operating modes of the analog outputs,
individually configurable
0
Unused (default)
128
Analog output -10 V...+10 V
129
Analog output 0 mA...20 mA (not with the
channels 4...7 and 12...15)
130
Analog output 4 mA...20 mA (not with the
channels 4...7 and 12...15)
Table 98: Channel monitoring
4
)
Internal value
Monitoring
0
Plausibility, open-circuit (broken wire) and
short circuit (default)
1
Open-circuit (broken wire) and short circuit
2
Plausibility
3
No monitoring
Output channels
0 and 8 (2 chan-
nels, AO523)
Output channels
1...7 and 9...15
(14 channels,
AO523)
Device specifications
I/O modules > Analog I/O modules
2022/01/31
3ADR010278, 3, en_US
494