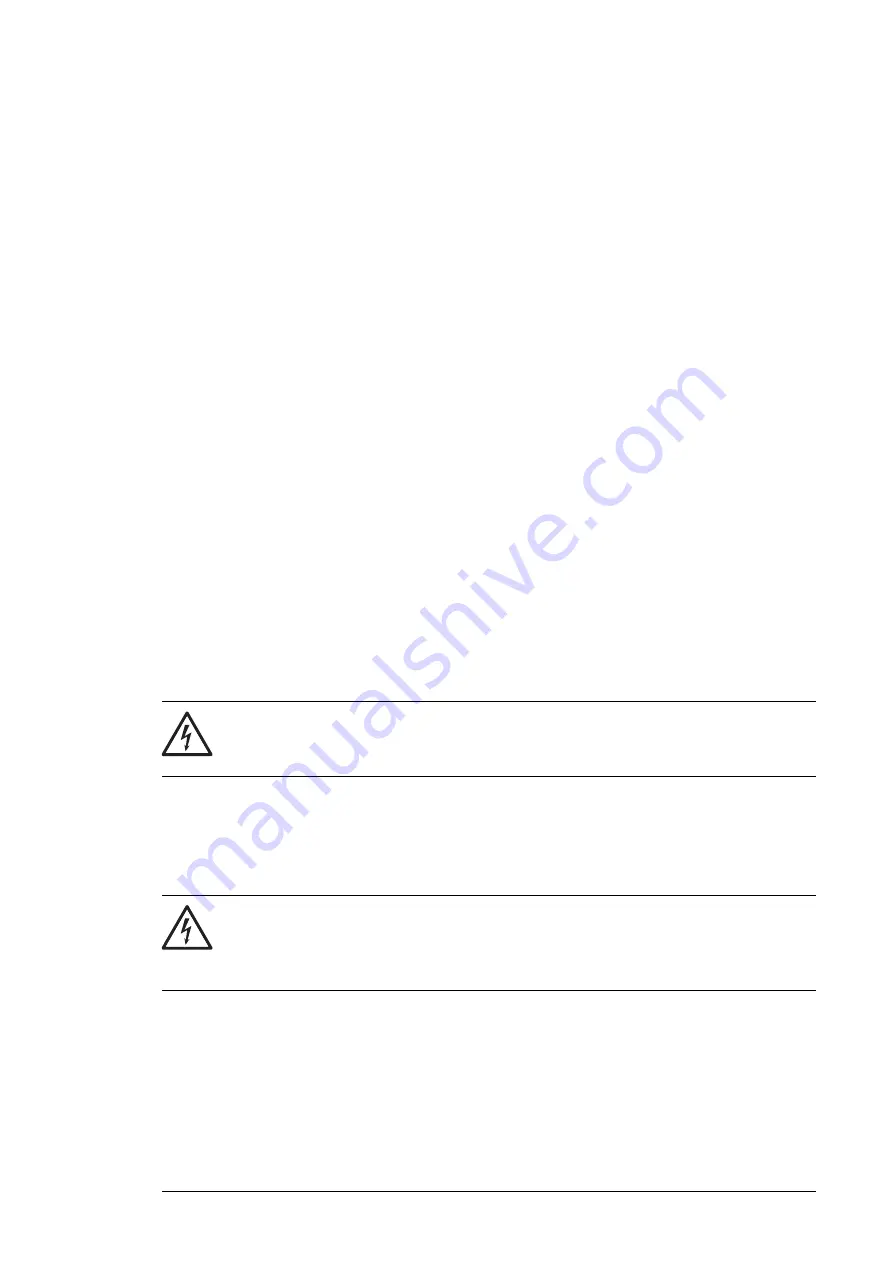
Note:
As standard, the drive contains capacitors connected between the main circuit and
the frame. These capacitors and long motor cables increase the ground leakage current
and may cause nuisance faults in residual current devices.
Implementing the emergency stop function
For safety reasons, install the emergency stop devices at each operator control station and
at other operating stations where emergency stop may be needed. Implement the emergency
stop according to relevant standards.
Note:
You can use the Safe torque off function of the drive to implement the Emergency
stop function.
Implementing the Safe torque off function
See
The Safe torque off function (page 171)
.
Implementing the undervoltage control (power-loss
ride-through)
Implement the power-loss ride-through function as follows:
•
Check that the power-loss ride-through function of the drive is enabled with parameter
30.31 Undervoltage control
.
•
Set parameter
21.01 Vector start mode
to Automatic (in vector mode) or parameter
21.19 Scalar start mode
to Automatic (in scalar mode) to make flying start (starting into
a rotating motor) possible. If the installation is equipped with a main contactor, prevent
its tripping at the input power break. For example, use a time delay relay (hold) in the
contactor control circuit.
WARNING!
Make sure that the flying restart of the motor will not cause any danger. If you are
in doubt, do not implement the Power-loss ride-through function.
Using power factor compensation capacitors with the drive
Power factor compensation is not needed with AC drives. However, if a drive is to be
connected in a system with compensation capacitors installed, note the following restrictions.
WARNING!
Do not connect power factor compensation capacitors or harmonic filters to the
motor cables (between the drive and the motor). They are not meant to be used
with AC drives and can cause permanent damage to the drive or themselves.
If there are power factor compensation capacitors in parallel with the input of the drive:
Guidelines for planning the electrical installation 81
Summary of Contents for ACH580-04
Page 1: ... ABB DRIVES FOR HVAC ACH580 04 drive modules Hardware manual ...
Page 2: ......
Page 4: ......
Page 54: ...54 ...
Page 88: ...88 ...
Page 100: ...100 ...
Page 118: ...118 ...
Page 122: ...122 ...
Page 124: ...124 ...
Page 128: ...3 6 5 5 128 Maintenance ...
Page 134: ...134 ...
Page 156: ...R10 standard configuration 156 Dimension drawings ...
Page 157: ...R10 with E208 0H354 H356 H370 0H371 Dimension drawings 157 ...
Page 158: ...R10 with option B051 158 Dimension drawings ...
Page 159: ...R10 with option E208 H356 P906 192 Tools R10 3 1 Dimension drawings 159 ...
Page 160: ...R10 with option E208 0H371 H356 0H354 H370 P906 Tools 191 R10 2 1 160 Dimension drawings ...
Page 161: ...R10 with option B051 P906 190 Tools R10 1 1 Dimension drawings 161 ...
Page 162: ...R11 standard configuration 162 Dimension drawings ...
Page 163: ...R11 with option E208 0H371 H356 0H354 H370 Dimension drawings 163 ...
Page 164: ...R11 with option B051 164 Dimension drawings ...
Page 165: ...R11 with option E208 H356 P906 Dimension drawings 165 ...
Page 166: ...R11 with option E208 0H371 H356 0H354 H370 P906 166 Dimension drawings ...
Page 167: ...R11 with option B051 P906 Dimension drawings 167 ...
Page 186: ... Declaration of conformity 186 The Safe torque off function ...
Page 206: ...Dimension drawing 206 External control unit option P906 ...
Page 212: ...212 ...
Page 224: ...224 ...
Page 226: ...226 ...
Page 234: ...234 ...