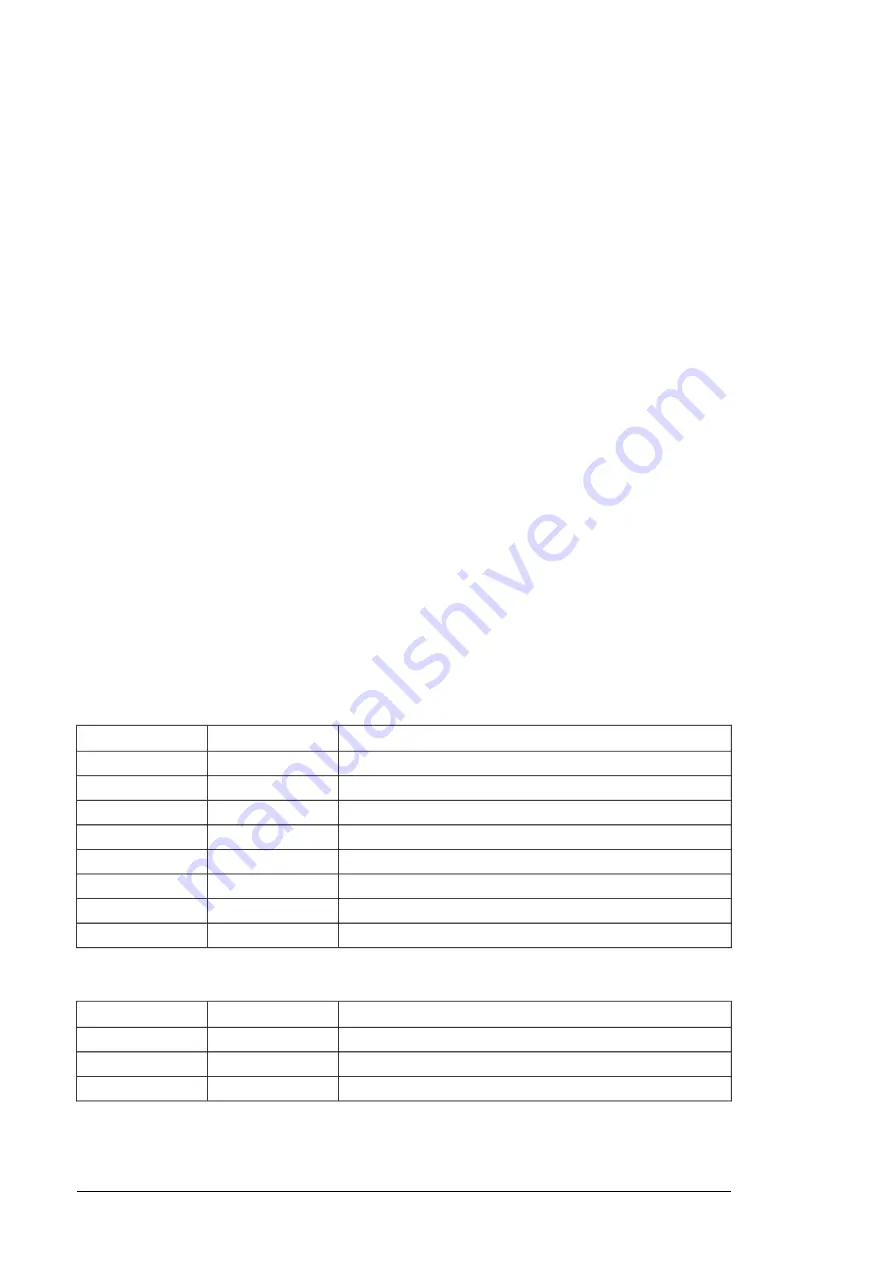
Place the control board(s) away from:
•
main circuit components such as contactors, switches and power cables
•
hot parts (heatsink, air outlet of the drive module).
■
Grounding of mounting structures
Arrange the grounding of the module by leaving the contact surfaces of the fastening points
unpainted (bare metal-to-metal contact). The module frame is grounded to the PE busbar
of the cabinet via the fastening surfaces, screws and the cabinet frame. Alternatively, use
a separate grounding conductor between the PE terminal of the module and the PE busbar
of the cabinet.
Ground also the other components in the cabinet according to the principle above.
■
Busbar material and joints
ABB recommends tin-plated copper but aluminum can also be used.
Note:
Before joining aluminum busbars, remove the oxide layer and apply suitable
anti-oxidant joint compound.
■
Shrouds
The installation of shrouds (touch protection) to fulfill applicable safety regulations is the
responsibility of the drive system builder.
Ready-made shrouding parts are available from ABB for some cabinet designs, see the
ordering information.
■
Tightening torques
Unless a tightening torque is specified in the text, the following torques can be used.
Electrical connections
Note
Torque
Size
Strength class 4.6...8.8
0.5 N·m (4.4 lbf·in)
M3
Strength class 4.6...8.8
1 N·m (9 lbf·in)
M4
Strength class 8.8
4 N·m (35 lbf·in)
M5
Strength class 8.8
9 N·m (6.6 lbf·ft)
M6
Strength class 8.8
22 N·m (16 lbf·ft)
M8
Strength class 8.8
42 N·m (31 lbf·ft)
M10
Strength class 8.8
70 N·m (52 lbf·ft)
M12
Strength class 8.8
120 N·m (90 lbf·ft)
M16
Mechanical connections
Note
Max. torque
Size
Strength class 8.8
6 N·m (53 lbf·in)
M5
Strength class 8.8
10 N·m (7.4 lbf·ft)
M6
Strength class 8.8
24 N·m (17.7 lbf·ft)
M8
38 Generic cabinet planning instructions
Summary of Contents for ACH580-04
Page 1: ... ABB DRIVES FOR HVAC ACH580 04 drive modules Hardware manual ...
Page 2: ......
Page 4: ......
Page 54: ...54 ...
Page 88: ...88 ...
Page 100: ...100 ...
Page 118: ...118 ...
Page 122: ...122 ...
Page 124: ...124 ...
Page 128: ...3 6 5 5 128 Maintenance ...
Page 134: ...134 ...
Page 156: ...R10 standard configuration 156 Dimension drawings ...
Page 157: ...R10 with E208 0H354 H356 H370 0H371 Dimension drawings 157 ...
Page 158: ...R10 with option B051 158 Dimension drawings ...
Page 159: ...R10 with option E208 H356 P906 192 Tools R10 3 1 Dimension drawings 159 ...
Page 160: ...R10 with option E208 0H371 H356 0H354 H370 P906 Tools 191 R10 2 1 160 Dimension drawings ...
Page 161: ...R10 with option B051 P906 190 Tools R10 1 1 Dimension drawings 161 ...
Page 162: ...R11 standard configuration 162 Dimension drawings ...
Page 163: ...R11 with option E208 0H371 H356 0H354 H370 Dimension drawings 163 ...
Page 164: ...R11 with option B051 164 Dimension drawings ...
Page 165: ...R11 with option E208 H356 P906 Dimension drawings 165 ...
Page 166: ...R11 with option E208 0H371 H356 0H354 H370 P906 166 Dimension drawings ...
Page 167: ...R11 with option B051 P906 Dimension drawings 167 ...
Page 186: ... Declaration of conformity 186 The Safe torque off function ...
Page 206: ...Dimension drawing 206 External control unit option P906 ...
Page 212: ...212 ...
Page 224: ...224 ...
Page 226: ...226 ...
Page 234: ...234 ...