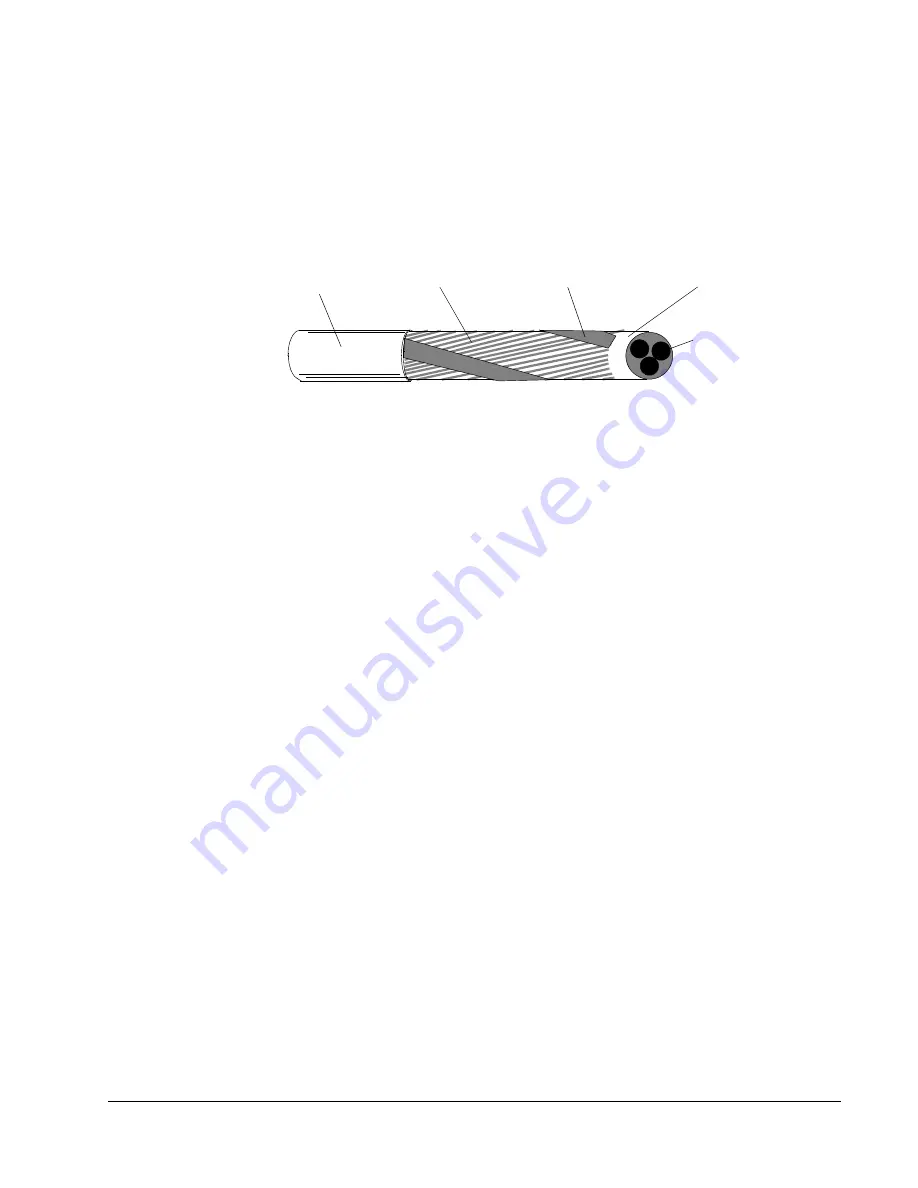
ACQ800-37 Hardware Manual
61
Planning the electrical installation
Motor cable shield
To effectively suppress radiated and conducted radio-frequency emissions, the
shield conductivity must be at least 1/10 of the phase conductor conductivity. The
requirements are easily met with a copper or aluminium shield. The minimum
requirement of the motor cable shield of the drive is shown below. It consists of a
concentric layer of copper wires with an open helix of copper tape. The better and
tighter the shield, the lower the emission level and the bearing currents.
Additional US requirements
Type MC continuous corrugated aluminum armor cable with symmetrical grounds or
shielded power cable must be used for the motor cables if metallic conduit is not
used. For the North American market, 600 V AC cable is accepted for up to
500 V AC. 1000 V AC cable is required above 500 V AC (below 600 V AC). For
drives rated over 100 amperes, the power cables must be rated for 75
°
C (167
°
F).
Conduit
Where conduits must be coupled together, bridge the joint with a ground conductor
bonded to the conduit on each side of the joint. Bond the conduits also to the drive
enclosure. Use separate conduits for input power, motor, brake resistors, and control
wiring. When conduit is employed, type MC continuous corrugated aluminum armor
cable or shielded cable is not required. A dedicated ground cable is always required.
Note:
Do not run motor wiring from more than one drive in the same conduit.
Armored cable / shielded power cable
6-conductor (3 phases and 3 ground) type MC continuous corrugated aluminum
armor cable with symmetrical grounds is available from the following suppliers (trade
names in parentheses):
• Anixter Wire & Cable (Philsheath)
• BICC General Corp (Philsheath)
• Rockbestos Co. (Gardex)
• Oaknite (CLX).
Shielded power cables are available from Belden, Lapp Kabel (ÖLFLEX) and Pirelli,
among others.
Insulation jacket
Copper wire screen
Helix of copper tape
Cable core
Inner insulation
Summary of Contents for ACQ800 Series
Page 1: ...Hardware Manual ACQ800 37 Drives 55 to 450 kW 75 to 550 hp ACQ800 ...
Page 4: ......
Page 12: ...12 ACQ800 37 Hardware Manual Safety instructions ...
Page 24: ...24 ACQ800 37 Hardware Manual About this manual ...
Page 52: ...52 ACQ800 37 Hardware Manual Mechanical installation ...
Page 78: ...78 ACQ800 37 Hardware Manual Electrical installation ...
Page 84: ...84 ACQ800 37 Hardware Manual Motor control and I O board RMIO ...
Page 92: ...92 ACQ800 37 Hardware Manual Installation checklist and start up ...
Page 106: ...106 ACQ800 37 Hardware Manual Maintenance 3 4 5 6 8 7b 7a ...
Page 107: ...ACQ800 37 Hardware Manual 107 Maintenance 9 10 11 View from back ...
Page 123: ...ACQ800 37 Hardware Manual 123 Technical data Declaration of Conformity ...
Page 124: ...124 ACQ800 37 Hardware Manual Technical data ...
Page 128: ...128 ACQ800 37 Hardware Manual Dimensions Frame R6 ...
Page 129: ...ACQ800 37 Hardware Manual 129 Dimensions Frame R6 continued ...
Page 130: ...130 ACQ800 37 Hardware Manual Dimensions Frame R7i ...
Page 131: ...ACQ800 37 Hardware Manual 131 Dimensions Frame R7i continued ...
Page 132: ...132 ACQ800 37 Hardware Manual Dimensions Frame R7i continued ...
Page 133: ...ACQ800 37 Hardware Manual 133 Dimensions Frame R7i continued ...
Page 134: ...134 ACQ800 37 Hardware Manual Dimensions Frame R8i ...
Page 135: ...ACQ800 37 Hardware Manual 135 Dimensions Frame R8i continued ...
Page 136: ...136 ACQ800 37 Hardware Manual Dimensions Frame R8i continued ...
Page 137: ...ACQ800 37 Hardware Manual 137 Dimensions Frame R8i continued ...