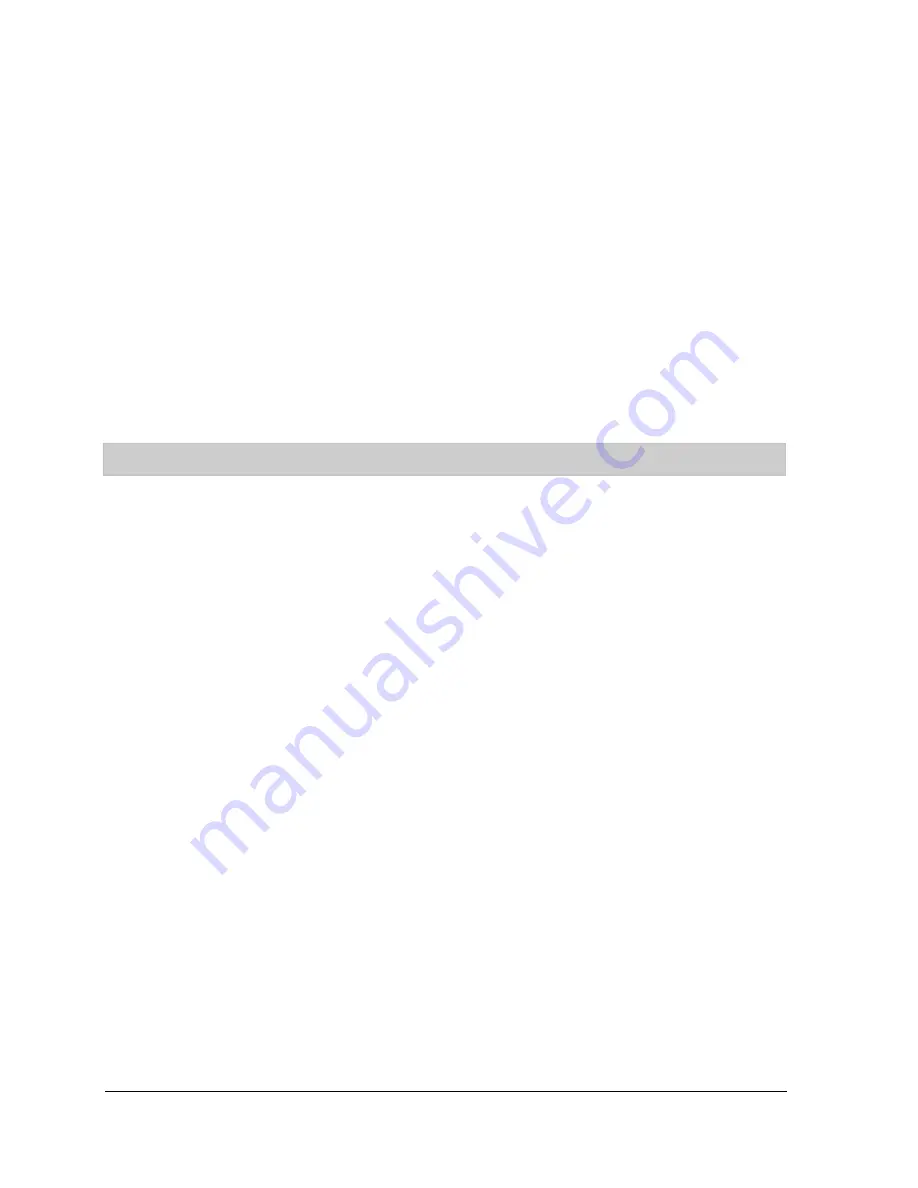
Chapter 7 - Parameter Settings
ABB
42 (of 62)
3BHS135824 ZAB E01Rev. D ACS 6000 Commissioning Manual
Parameter Group 77: System Configuration:
Parameter group 77 defines the drive configuration, e.g. asynchronous
or synchronous drive, the type of line rectifier, the number of inverter
units etc.,
Parameter
77.9
Drive Type
activates the control and monitoring
functions related to the excitation unit.
Parameter Groups 81-84: Optional I/O
These groups provide settings for optional S800 I/O modules of
Cluster
3
in the WCU. Refer to the wiring diagramsto see if I/O modules are
installed and set the parameters accordingly.
Parameter Group 98: Real Time Clock
The local time is set manually (98.07 "SET") unless there is automatic
time synchronization from the overriding system.
7.2
Communication Parameters
This section provides information on parameters related to
communication interfaces.
Communication to an overriding control system is typically
accomplished via a fieldbus adapter (FBA) or an ABB Advant controller
(e.g. AC110). Both are connected to channel 0 of the AMC board.
If an AC 80 Advant controller is part of the converter (CIU option) the
overriding system can communicate via this controller which is linked to
channel 4 of the AMC board.
A possible configuration an be that FBA and AC 80 controller (option:
CIU) are both present in the converter. The task of the FBA is to
communicate with the overriding control system and the AC 80 is used
to control and monitor external equipment.
7.2.1
Fieldbus Adapters
Parameter
75.1 Comm Module
defines if FBA or ABB Advant
Controller is used to communicate an overriding control system.
After setting parameter 75.1 the ACS 6000 identifies the type of
communication interface and opens parameter group
51
. Group 51
becomes visible after the signal and parameter table has been
uploaded again. The content of this group depends on the type of
communication interface in use. Changes to the group do not come into
effect immediately, but only after the power of the fieldbus adapter has
been switched off and on again.
Parameter
groups 90 and 91
define the dataset communication of the
FBA. Refer to the customer / automation supplier for information on the
dataset communication.