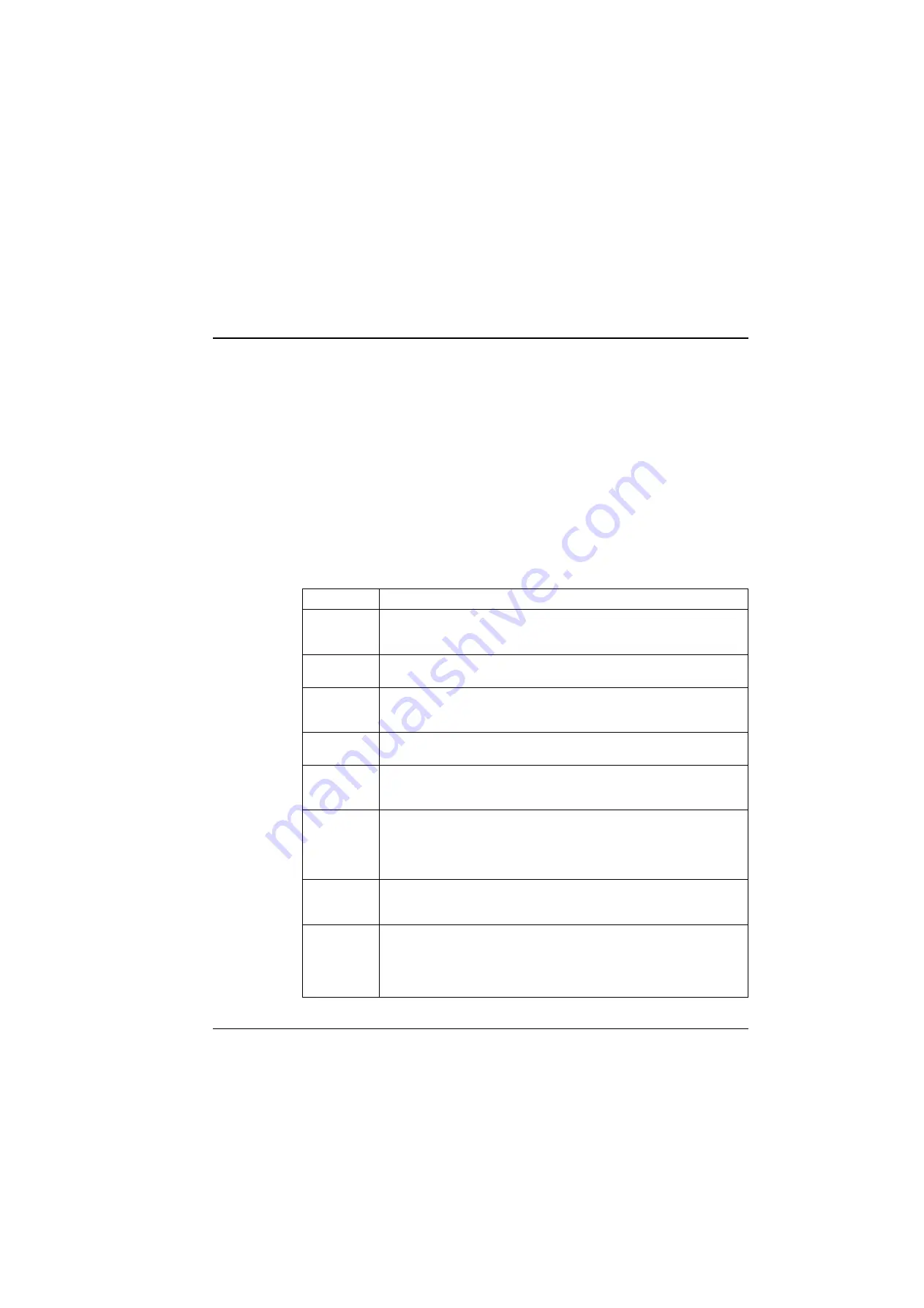
Application macros
85
Application macros
What this chapter contains
The chapter describes the application macros. For each macro, there is a wiring
diagram showing the default control connections (digital and analog I/O). The
chapter also explains how to save a user macro and how to recall it.
Overview of macros
Application macros are preprogrammed parameter sets. While starting up the drive,
the user typically selects one of the macros - the one that is best suited for the
purpose - with parameter
APPLIC MACRO, makes the essential changes and
saves the result as a user macro.
The ACS350 has seven standard macros and three user macros. The table below
contains a summary of the macros and describes suitable applications.
Macro
Suitable applications
ABB Standard
Ordinary speed control applications where no, one, two or three constant speeds
are used. Start/stop is controlled with one digital input (level start and stop). It is
possible to switch between two acceleration and deceleration times.
3-wire
Ordinary speed control applications where no, one, two or three constant speeds
are used. The drive is started and stopped with push buttons.
Alternate
Speed control applications where no, one, two or three constant speeds are used.
Start, stop and direction are controlled by two digital inputs (combination of the
input states determines the operation).
Motor
Potentiometer
Speed control applications where no or one constant speed is used. The speed is
controlled by two digital inputs (increase / decrease / keep unchanged).
Hand/Auto
Speed control applications where switching between two control devices is
needed. Some control signal terminals are reserved to one device, the rest for the
other. One digital input selects between the terminals (devices) in use.
PID Control
Process control applications, e.g. different closed loop control systems such as
pressure control, level control and flow control. It is possible to switch between
process and speed control: Some control signal terminals are reserved for
process control, others for speed control. One digital input selects between
process and speed control.
Torque
Control
Torque control applications. It is possible to switch between torque and speed
control: Some control signal terminals are reserved to torque control, others for
speed control. One digital input selects between torque and speed control.
User
The user can save the customised standard macro, i.e. the parameter settings
including group
, and the results of the motor identification run
into the permanent memory, and recall the data at a later time.
For example, three user macros can be used when switching between three
different motors is required.
Summary of Contents for ACS350 Series
Page 1: ...ACS350 User s Manual ACS350 Drives 0 37 22 kW 0 5 30 HP ...
Page 4: ......
Page 8: ...Safety 8 ...
Page 18: ...Table of contents 18 ...
Page 24: ...Hardware description 24 ...
Page 44: ...Installation checklist 44 ...
Page 56: ...Start up control with I O and ID Run 56 ...
Page 140: ...Program features 140 ...
Page 242: ...Actual signals and parameters 242 ...
Page 266: ...Fieldbus control with embedded fieldbus 266 ...
Page 284: ...Fault tracing 284 ...
Page 288: ...Maintenance and hardware diagnostics 288 ...
Page 309: ...Dimensions 309 Frame size R2 IP20 NEMA 1 3AFE68586658 A Frame size R2 IP20 NEMA 1 VAR EMC ...
Page 311: ...Dimensions 311 Frame size R3 IP20 NEMA 1 3AFE68579872 B Frame size R3 IP20 NEMA 1 VAR EMC ...
Page 313: ......