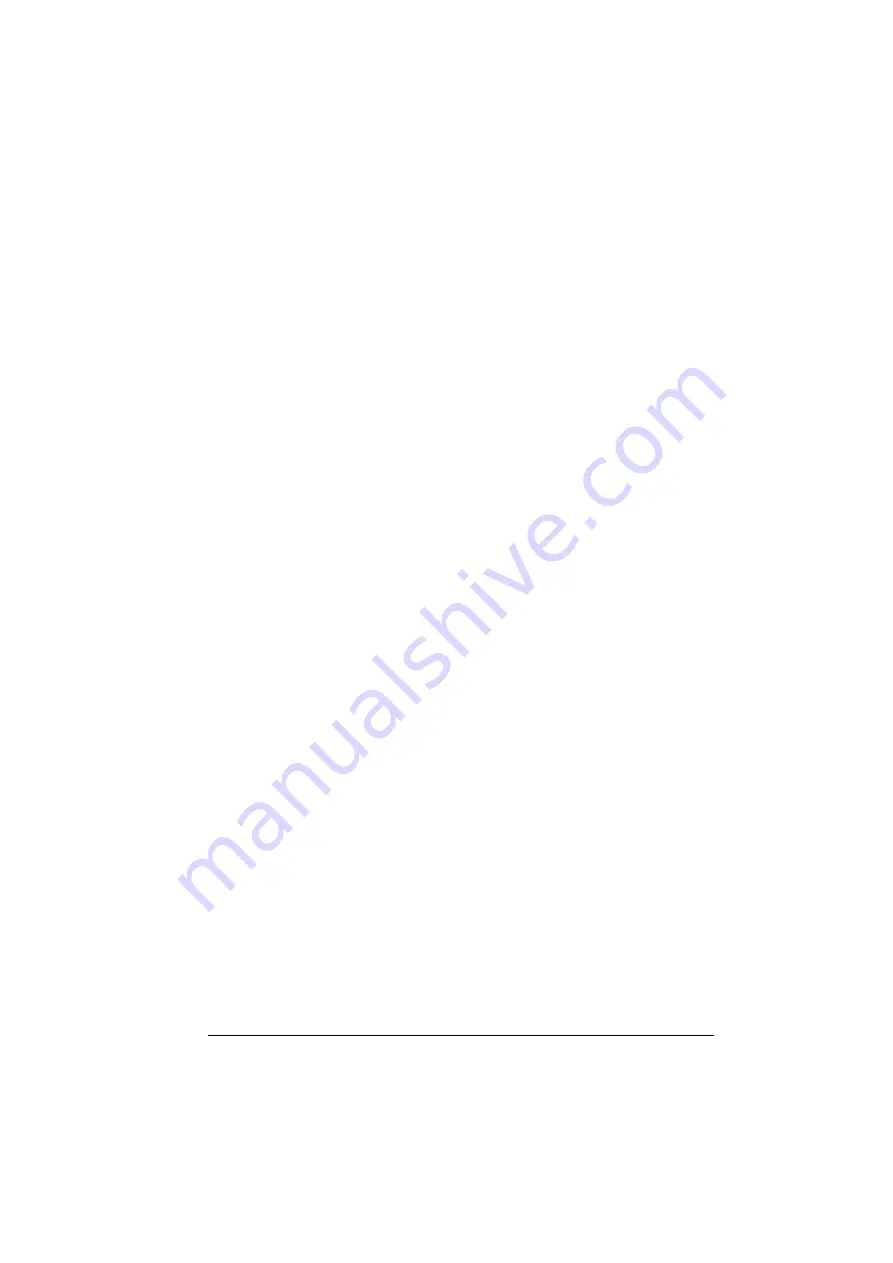
Technical data 375
1)
E = EMC filter connected (metal EMC filter screw installed),
U = EMC filter disconnected (plastic EMC filter screw installed), US parametrization.
2)
Overloading not allowed through Common DC connection.
3)
Input current is based on the rated motor nominal power (
P
N
), supply network, line
inductance and load motor.
Input values with choke can be met with ABB CHK-xx or typical 5% chokes.
4)
480 V values are based on the fact that the motor load current is lower with the same output
power.
Definitions
Sizing
Drive sizing is based on the rated motor current and power. To achieve the rated
motor power given in the table, the rated current of the drive must be higher than or
equal to the rated motor current. Also the rated power of the drive must be higher
than or equal to compared to the rated motor power. The power ratings are the same
regardless of the supply voltage within one voltage range.
Note 1:
The maximum allowed motor shaft power is limited to 1.5 ·
P
N
. If the limit is
exceeded, motor torque and current are automatically restricted. The function
protects the input bridge of the drive against overload.
Note 2:
The ratings apply at ambient temperature of 40 °C (104 °F) for
I
2N
.
Note 3:
It is important to check that in Common DC systems the power flowing
through the common DC connection does not exceed
P
N
.
Input
I
1N
continuous rms input current (for dimensioning cables and fuses)
I
1N
(480 V)
continuous rms input current (for dimensioning cables and fuses) for drives
with 480 V input voltage
Output
I
2N
continuous rms current. 50% overload is allowed for one minute every ten
minutes.
I
2,1 min/10 min
maximum (50% overload) current allowed for one minute every ten minutes
I
2max
maximum output current. Available for two seconds at start, otherwise as long
as allowed by the drive temperature.
P
N
typical motor power. The kilowatt ratings apply to most IEC 4-pole motors. The
horsepower ratings apply to most NEMA 4-pole motors. This is also the
maximum load through the Common DC connection and must not be
exceeded.
R0…R4
ACS355 is manufactured in frame sizes R0…R4. Some instructions and other
information that only concern certain frame sizes are marked with the symbol
of the frame size (R0…R4).
Summary of Contents for ACS355 series
Page 1: ...ABB machinery drives User s manual ACS355 drives ...
Page 4: ......
Page 16: ...16 ...
Page 32: ...32 Operation principle and hardware description ...
Page 58: ...58 Electrical installation ...
Page 74: ...74 Start up control with I O and ID run ...
Page 106: ...106 Control panels ...
Page 120: ...120 Application macros ...
Page 178: ...178 Program features ...
Page 338: ...338 Fieldbus control with embedded fieldbus ...
Page 368: ...368 Fault tracing ...
Page 404: ...404 Dimension drawings ...
Page 410: ...410 Appendix Resistor braking ...
Page 434: ...434 Appendix Permanent magnet synchronous motors PMSMs ...