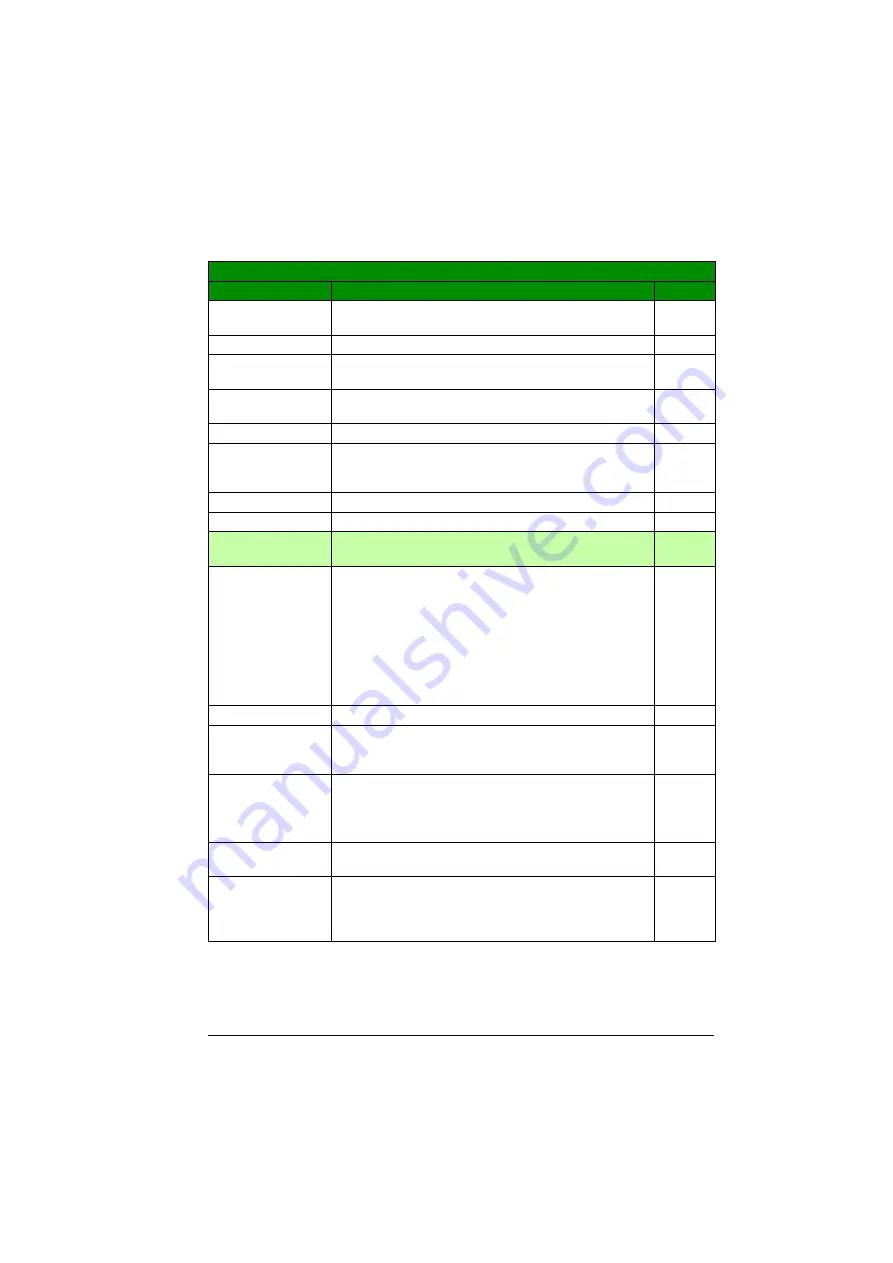
Actual signals and parameters 285
4231 TRIM SCALE
Defines the multiplier for the trimming function. See section
on page
.
0.0%
-100.0…100.0% Multiplier
1 = 0.1%
4232 CORRECTION
SRC
Selects the trim reference. See section
.
PID2REF
PID2 reference selected by parameter
(ie, signal
value)
1
PID2OUTPUT
PID2 output, ie, signal
value
2
4233 TRIM
SELECTION
Selects whether the trimming is used for correcting the
speed or torque reference. See section
.
SPEED/FREQ Speed reference trimming
0
TORQUE
Torque reference trimming (only for REF2 (%))
1
43 MECH BRK
CONTROL
Control of a mechanical brake. See section
on page
.
4301 BRAKE OPEN
DLY
Defines the brake open delay (= the delay between the
internal open brake command and the release of the motor
speed control). The delay counter starts when the motor
current/torque/speed has risen to the level required at brake
release (parameter
) and the motor has been magnetized.
Simultaneously with the start of the counter, the brake
function energizes the relay output controlling the brake and
the brake starts opening.
0.20 s
0.00…2.50 s
Delay time
1 = 0.01 s
4302 BRAKE OPEN
LVL
Defines the motor starting torque/current at brake release.
After start the drive current/torque is frozen to the set value,
until the motor is magnetized.
100%
0.0…180.0%
Value as a percentage of the nominal torque
T
N
(in vector
control) or the nominal current
I
2N
(in scalar control).
The control mode is selected by parameter
1 = 0.1%
4303 BRAKE
CLOSE LVL
Defines the brake close speed. After stop the brake is
closed when drive speed falls below the set value.
4.0%
0.0…100.0%
Value as a percentage of the nominal speed (in vector
control) or the nominal frequency (in scalar control). The
control mode is selected by parameter
.
1 = 0.1%
All parameters
No.
Name/Value
Description
Def/FbEq
Summary of Contents for ACS355 series
Page 1: ...ABB machinery drives User s manual ACS355 drives ...
Page 4: ......
Page 16: ...16 ...
Page 32: ...32 Operation principle and hardware description ...
Page 58: ...58 Electrical installation ...
Page 74: ...74 Start up control with I O and ID run ...
Page 106: ...106 Control panels ...
Page 120: ...120 Application macros ...
Page 178: ...178 Program features ...
Page 338: ...338 Fieldbus control with embedded fieldbus ...
Page 368: ...368 Fault tracing ...
Page 404: ...404 Dimension drawings ...
Page 410: ...410 Appendix Resistor braking ...
Page 434: ...434 Appendix Permanent magnet synchronous motors PMSMs ...