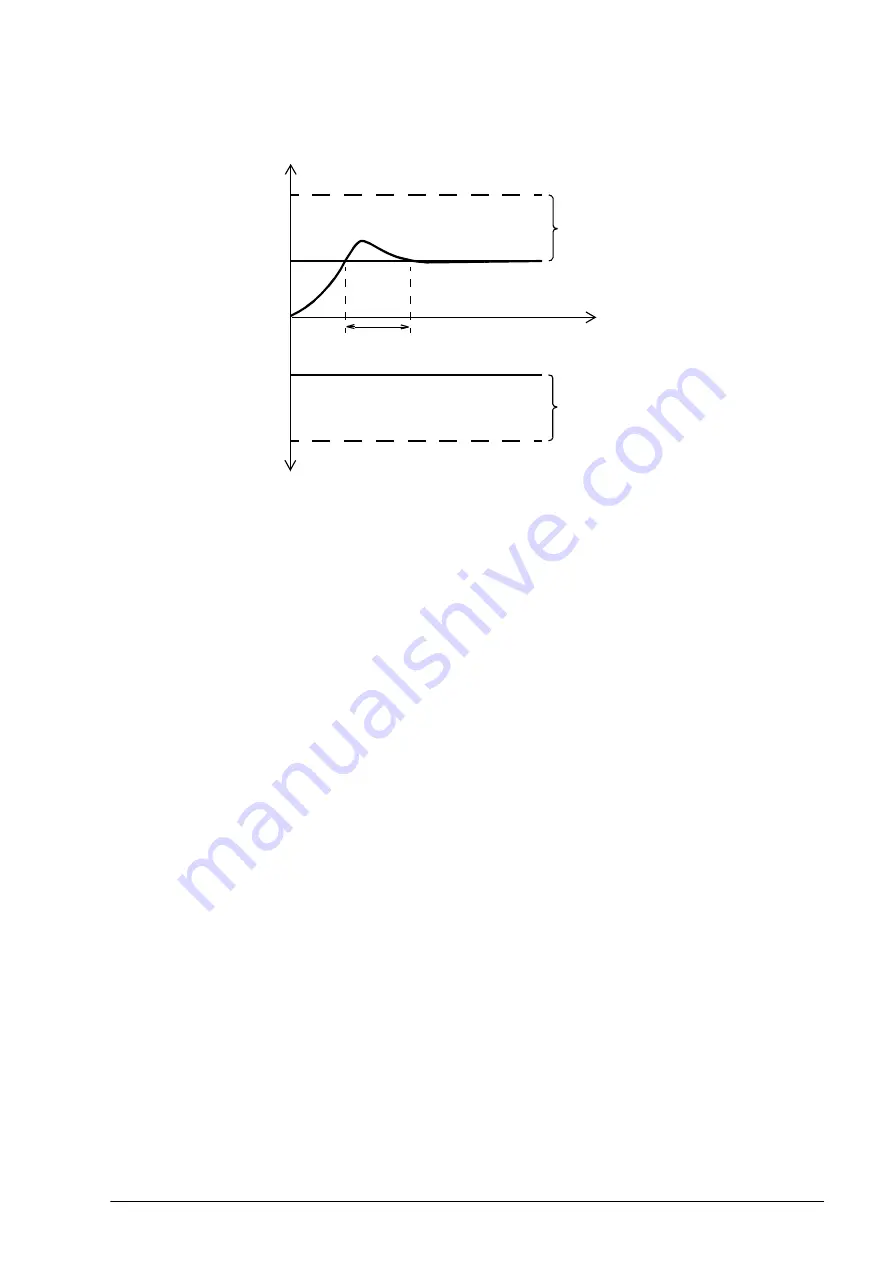
Program features 43
The function is based on a PI controller. The proportional gain and integration time
can be defined by parameters. Setting these to zero disables rush control.
Settings
Parameters
(page
).
Encoder support
The following optional interface modules are available:
• TTL encoder interface FEN-01: two TTL inputs
• HTL encoder interface FEN-31: HTL encoder input
The interface module is to be installed onto slot 1 on the drive control unit.
Load and motor feedback
Three different sources can be used as speed and position feedback: encoder 1,
motor position estimate. Any of these can be used for load position calculation or
motor control. The load position calculation makes it possible, for example, to
determine the position of a conveyor belt or the height of the load on a crane. The
feedback sources are selected by parameters
90.41 Motor feedback selection
and
For detailed parameter connections of the motor and load feedback functions, see
the block diagrams on pages
and
. For more information on load position
calculation, see section
).
Motor speed
Time
Overspeed trip level
Overspeed trip level
0
Rush control active
Summary of Contents for ACS860
Page 1: ... ABB INDUSTRIAL DRIVES ACS860 primary control program Firmware manual ...
Page 4: ......
Page 10: ...10 Table of contents ...
Page 18: ...18 Using the control panel ...
Page 24: ...24 Control locations and operating modes ...
Page 54: ...54 Program features ...
Page 78: ...78 Program features ...
Page 90: ...90 Application macros ...
Page 342: ...342 Additional parameter data ...
Page 380: ...380 Fault tracing ...
Page 381: ...Fault tracing 381 ...
Page 382: ...382 Fault tracing ...
Page 436: ...436 Control chain diagrams ...