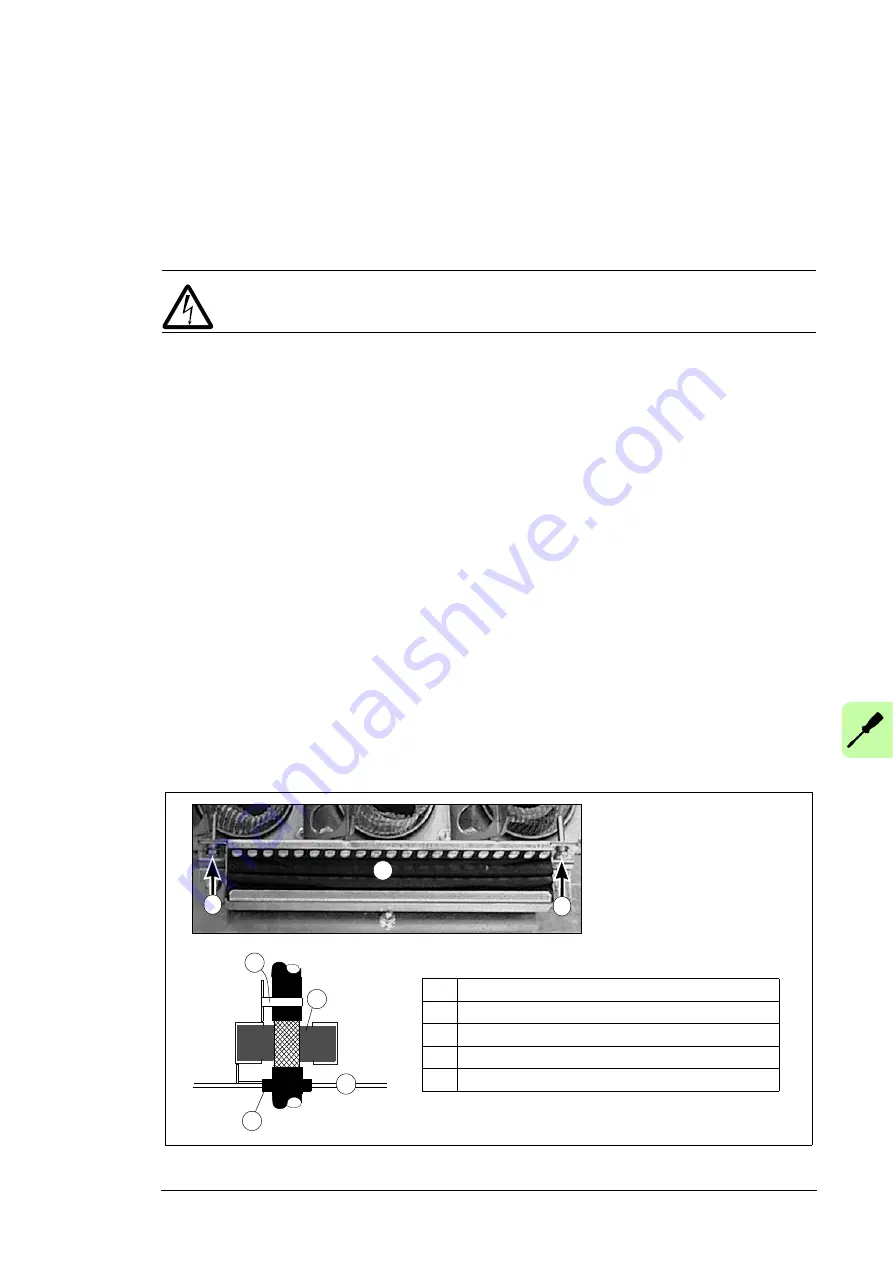
Electrical installation 77
Connecting the control cables
The default I/O connections can be different with some hardware options, see the circuit
diagrams delivered with the drive for the actual wiring. For other control programs, see
their firmware manuals.
Control cable connection procedure
WARNING!
Obey the instructions in chapter
. If you ignore
them, injury or death, or damage to the equipment can occur.
1. Stop the drive (if running) and do the steps in section
before you start the work.
2. Run the control cables into the auxiliary control cubicle (ACU) as described in section
Grounding the outer shields of the control cables at the cabinet lead-through
below.
3. Route the control cables as described in section
Routing the control cables inside the
.
4. Connect the control cables as described starting.
Grounding the outer shields of the control cables at the cabinet lead-through
Ground the outer shields of all control cables 360 degrees at the EMI conductive cushions
as follows:
1. Loosen the tightening screws of the EMI conductive cushions and pull the cushions
apart.
2. Cut adequate holes to the rubber grommets in the lead-through plate and lead the
cables through the grommets and the cushions into the cabinet.
3. Strip off the cable plastic sheath above the lead-through plate just enough to ensure
proper connection of the bare shield and the EMI conductive cushions.
4. Tighten the two tightening screws so that the EMI conductive cushions press tightly
round the bare shield.
View from above
1
Tightening screw
2
EMI conductive cushion
3
Strain relief
4
Grommet
5
Lead-through plate
2
3
4
5
1
2
1
Summary of Contents for ACS880-07XT Series
Page 1: ...ABB industrial drives Hardware manual ACS880 07XT drives 400 to 1200 kW ...
Page 4: ......
Page 12: ...12 ...
Page 20: ...20 Safety instructions ...
Page 26: ...26 Introduction to the manual ...
Page 54: ...54 Mechanical installation ...
Page 89: ...Electrical installation 89 PE 11 8 4 9 11 ...
Page 94: ...94 Electrical installation ...
Page 112: ...112 Fault tracing ...
Page 123: ...Maintenance 123 5 6 7 ...
Page 124: ...124 Maintenance 8 10 9 ...
Page 126: ...126 Maintenance 6 5 4 ...
Page 127: ...Maintenance 127 9 8 7 ...
Page 128: ...128 Maintenance 12 11 10 ...
Page 149: ...Dimensions 149 Dimension drawing examples Frame 2 R11 R10 with brake chopper ...
Page 150: ...150 Dimensions Frame 2 R11 R10 without brake chopper ...
Page 153: ...Dimensions 153 Location of input terminals ACS880 07XT 12 pulse ...
Page 154: ...154 Dimensions Location of output terminals ACS880 07XT R10 with du dt ...
Page 155: ...Dimensions 155 Location of output terminals ACS880 07XT R10 without du dt ...
Page 156: ...156 Dimensions Location of output terminals ACS880 07XT R11 with du dt ...
Page 157: ...Dimensions 157 Location of output terminals ACS880 07XT R11 without du dt ...
Page 158: ...158 Dimensions Location of PE terminals ACS880 07XT ...
Page 159: ...Dimensions 159 Location of resistor terminals ACS880 07XT R10 ...
Page 160: ...160 Dimensions Location of resistor terminals ACS880 07XT R11 ...
Page 168: ...www abb com drives www abb com drivespartners 3ABD00043579 Rev C EN 2018 01 01 Contact us ...