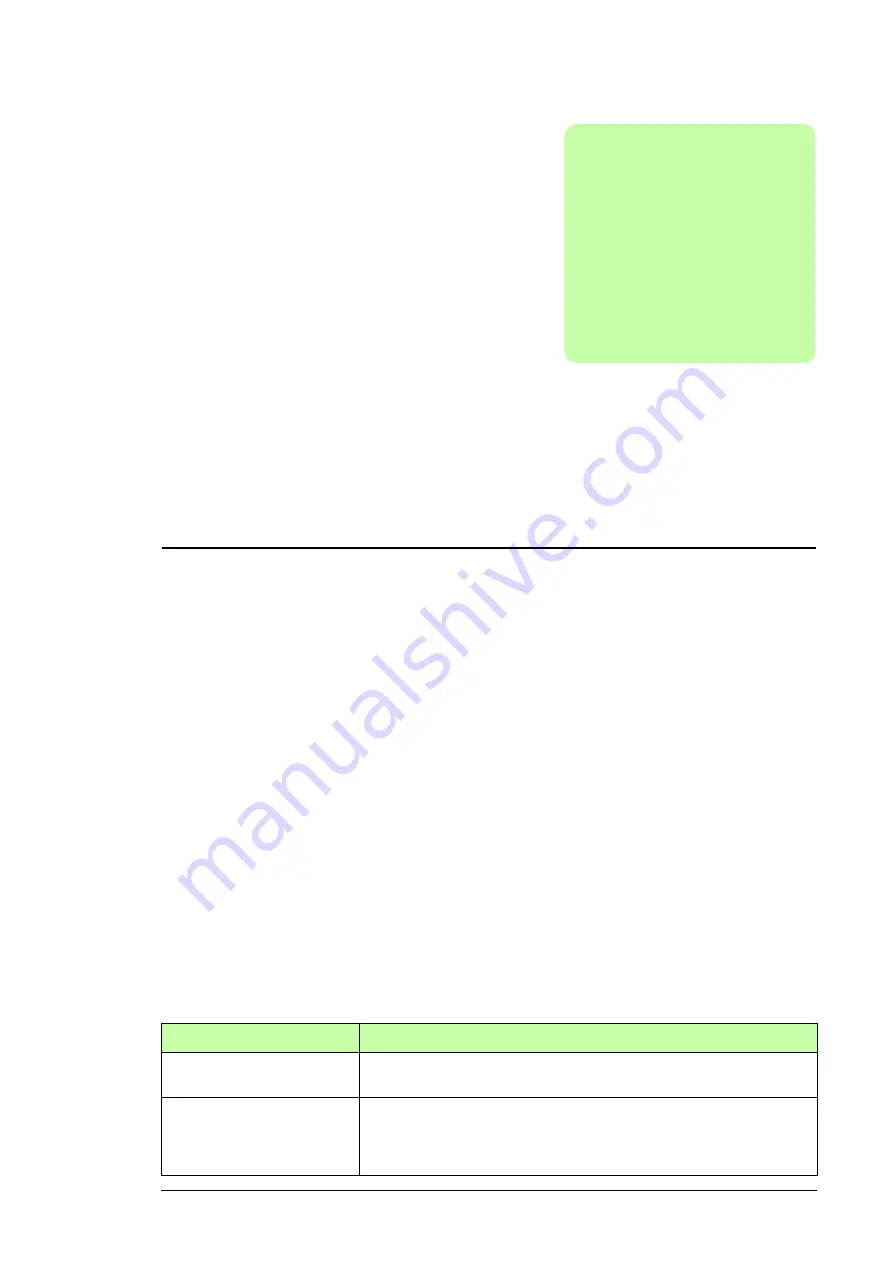
The Safe torque off function 223
14
The Safe torque off function
What this chapter contains
This chapter describes the Safe torque off (STO) function of the inverter (ie. the inverter
unit of the drive) and gives instructions for its use.
Description
The Safe torque off function can be used, for example, to construct safety or supervision
circuits that stop the inverter in case of danger (such as an emergency stop circuit).
Another possible application is a prevention of unexpected start-up switch that enables
short-time maintenance operations like cleaning or work on non-electrical parts of the
machinery without switching off the power supply to the inverter.
When activated, the Safe torque off function disables the control voltage of the power
semiconductors of the inverter output stage (A, see diagram below), thus preventing the
inverter from generating the torque required to rotate the motor. If the motor is running
when Safe torque off is activated, it coasts to a stop.
The Safe torque off function has a redundant architecture, that is, both channels must be
used in the safety function implementation. The safety data given in this manual is
calculated for redundant use, and does not apply if both channels are not used.
The Safe torque off function of the inverter complies with these standards:
Standard
Name
EN 60204-1:2006 + AC:2010
Safety of machinery – Electrical equipment of machines – Part 1: General
requirements
IEC 61326-3-1:2008
Electrical equipment for measurement, control and laboratory use – EMC
requirements – Part 3-1: Immunity requirements for safety-related
systems and for equipment intended to perform safety-related functions
(functional safety) – General industrial applications
Summary of Contents for ACS880-17
Page 1: ...ABB industrial drives Hardware manual ACS880 37 drives ...
Page 3: ......
Page 4: ......
Page 6: ......
Page 16: ...16 ...
Page 30: ...30 Introduction to the manual ...
Page 70: ...70 Mechanical installation ...
Page 105: ...Electrical installation 105 4 5 3 6 7 ...
Page 107: ...Electrical installation 107 5 6 4 3 ...
Page 108: ...108 Electrical installation 7 8 8 ...
Page 109: ...Electrical installation 109 9 10 ...
Page 111: ...Electrical installation 111 2 360 grounding detail a b b 1 5 a 11 b a PE 10 7 5 6 8 ...
Page 117: ...Electrical installation 117 PE 11 8 4 9 11 ...
Page 134: ...134 Control units of the drive ...
Page 140: ...140 Start up ...
Page 142: ...142 Fault tracing ...
Page 154: ...154 Maintenance 4 5 6 7 8 6 10 10 ...
Page 162: ...162 Maintenance 5 6 3 4 7 ...
Page 163: ...Maintenance 163 6 8 7 11 10 9 ...
Page 167: ...Maintenance 167 3 4b 4a 4b 8 ...
Page 185: ...Technical data 185 Declaration of Conformity ...
Page 186: ...186 Technical data ...
Page 196: ...196 Dimensions Dimension drawing examples Frame 1 R8i 1 R8i ...
Page 197: ...Dimensions 197 Frame 1 R8i 1 R8i top cable entry exit H351 H353 ...
Page 198: ...198 Dimensions Frame 1 R8i 1 R8i with brake choppers and resistors D150 D151 ...
Page 199: ...Dimensions 199 Frame 1 R8i 1 R8i with sine output filter E206 ...
Page 200: ...200 Dimensions Frame 2 R8i 2 R8i eg ACS880 37 1110A 3 IP22 ...
Page 201: ...Dimensions 201 Frame 2 R8i 2 R8i eg ACS880 37 1210A 3 IP54 ...
Page 204: ...204 Dimensions Frame 2 R8i 2 R8i with main breaker F255 and top entry top exit H351 H353 1 2 ...
Page 205: ...Dimensions 205 Frame 2 R8i 2 R8i with main breaker F255 and top entry top exit H351 H353 2 2 ...
Page 206: ...206 Dimensions Frame 3 R8i 3 R8i 1 2 ...
Page 207: ...Dimensions 207 Frame 3 R8i 3 R8i 2 2 ...
Page 208: ...208 Dimensions Frame 3 R8i 3 R8i with common motor terminal cubicle H359 1 2 ...
Page 209: ...Dimensions 209 Frame 3 R8i 3 R8i with common motor terminal cubicle H359 2 2 ...
Page 217: ...Dimensions 217 Sine filter E206 cubicle 1000 mm top cable exit ...
Page 221: ...Dimensions 221 Cubicle width 400 mm top cable exit Cubicle width 600 mm bottom cable exit ...
Page 222: ...222 Dimensions Cubicle width 600 mm top cable exit ...
Page 234: ...234 The Safe torque off function ...
Page 244: ...www abb com drives www abb com drivespartners 3AXD50000020437 Rev A EN 2015 02 06 Contact us ...