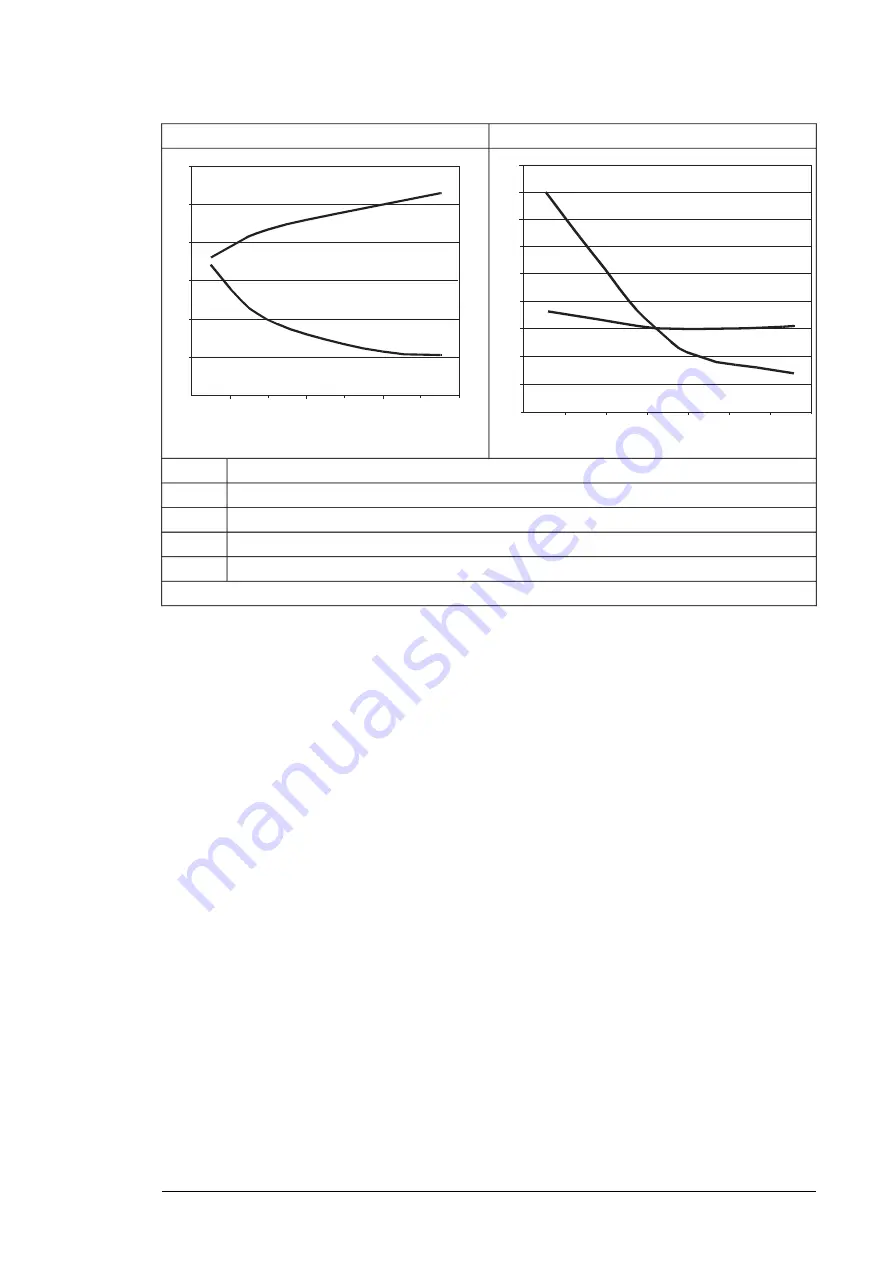
B
A
Û
LL
/
U
N
l
(m)
du/dt
UN
-------------(1/
μ
s)
1.0
2.0
5.0
4.0
3.0
1.5
2.5
3.5
4.5
100
200
300
5.5
100
200
300
0.0
0.5
1.0
1.5
2.0
2.5
3.0
l
(m)
du/dt
U
N
-------------(1/
μ
s)
Û
LL
/
U
N
Drive with d
u
/d
t
filter
A
Drive without d
u
/d
t
filter
B
Motor cable length
I
Relative peak line-to-line voltage
Û
LL
/
U
N
Relative d
u
/d
t
value
(d
u
/d
t
)/
U
N
Note: Û
LL
and d
u
/d
t
values are approximately 20% higher during the resistor braking.
Additional note for sine filters
A sine filter also protects the motor insulation system. The peak phase-to-phase voltage
with a sine filter is approximately 1.5 ·
U
N
.
Selecting the power cables
■
General guidelines
Select the input power and motor cables according to local regulations.
•
Current:
Select a cable capable of carrying the maximum load current.
•
Temperature:
For an IEC installation, select a cable rated for at least 70 °C (158 °F)
maximum permissible temperature of conductor in continuous use. For North America,
select a cable rated for at least 75 °C (167 °F).
•
Voltage:
600 V AC cable is accepted for up to 500 V AC. 750 V AC cable is accepted
for up to 600 V AC. 1000 V AC cable is accepted for up to 690 V AC.
To comply with the EMC requirements of the CE mark, use one of the preferred cable types.
See
Preferred power cable types (page 92)
Symmetrical shielded cable reduces electromagnetic emission of the whole drive system
as well as the stress on motor insulation, bearing currents and wear.
Metal conduit reduces electromagnetic emission of the whole drive system.
The protective conductor must always have an adequate conductivity.
Unless local wiring regulations state otherwise, the cross-sectional area of the protective
conductor must agree with the conditions that require automatic disconnection of the supply
required in 411.3.2. of IEC 60364-4-41:2005 and be capable of withstanding the prospective
Guidelines for planning the electrical installation 91
Summary of Contents for ACS880-37
Page 1: ... ABB INDUSTRIAL DRIVES ACS880 37 drives 45 400 kW 60 450 hp Hardware manual ...
Page 2: ......
Page 4: ......
Page 26: ...26 ...
Page 83: ...Mechanical installation 83 10 ...
Page 84: ...84 ...
Page 126: ... B055 a X504 126 Electrical installation ...
Page 144: ...144 ...
Page 150: ...150 ...
Page 152: ...152 ...
Page 160: ... 160 Maintenance ...
Page 196: ... 196 Maintenance ...
Page 232: ...R8 IP22 UL Type 1 and option B054 IP42 UL Type 1 Filtered 232 Dimension drawings ...
Page 233: ...R8 IP54 UL Type 12 option B055 option C129 Dimension drawings 233 ...
Page 235: ...R8 IP22 UL Type 1 and IP42 UL Type 1 Filtered option B054 option E206 Dimension drawings 235 ...
Page 236: ...R8 IP22 UL Type 1 option E202 236 Dimension drawings ...
Page 237: ...R11 IP22 UL Type 1 and IP42 UL Type 1 Filtered option B054 Dimension drawings 237 ...
Page 238: ...R11 IP54 UL Type 12 option B055 238 Dimension drawings ...
Page 240: ...R11 IP54 UL Type 12 option B055 option C128 240 Dimension drawings ...
Page 241: ...R11 IP54 UL Type 12 option B055 option C129 Dimension drawings 241 ...
Page 242: ...R11 IP54 UL Type 12 option B055 options C129 H350 H352 242 Dimension drawings ...
Page 243: ...R11 IP22 UL Type 1 and IP42 UL Type 1 Filtered option B054 option D150 Dimension drawings 243 ...
Page 245: ...R11 IP22 UL Type 1 and IP42 UL Type 1 Filtered option B054 option E206 Dimension drawings 245 ...
Page 246: ...R11 IP22 UL Type 1 option E202 246 Dimension drawings ...
Page 267: ... Declaration of conformity The Safe torque off function 267 ...
Page 268: ...268 The Safe torque off function ...
Page 280: ...280 ...