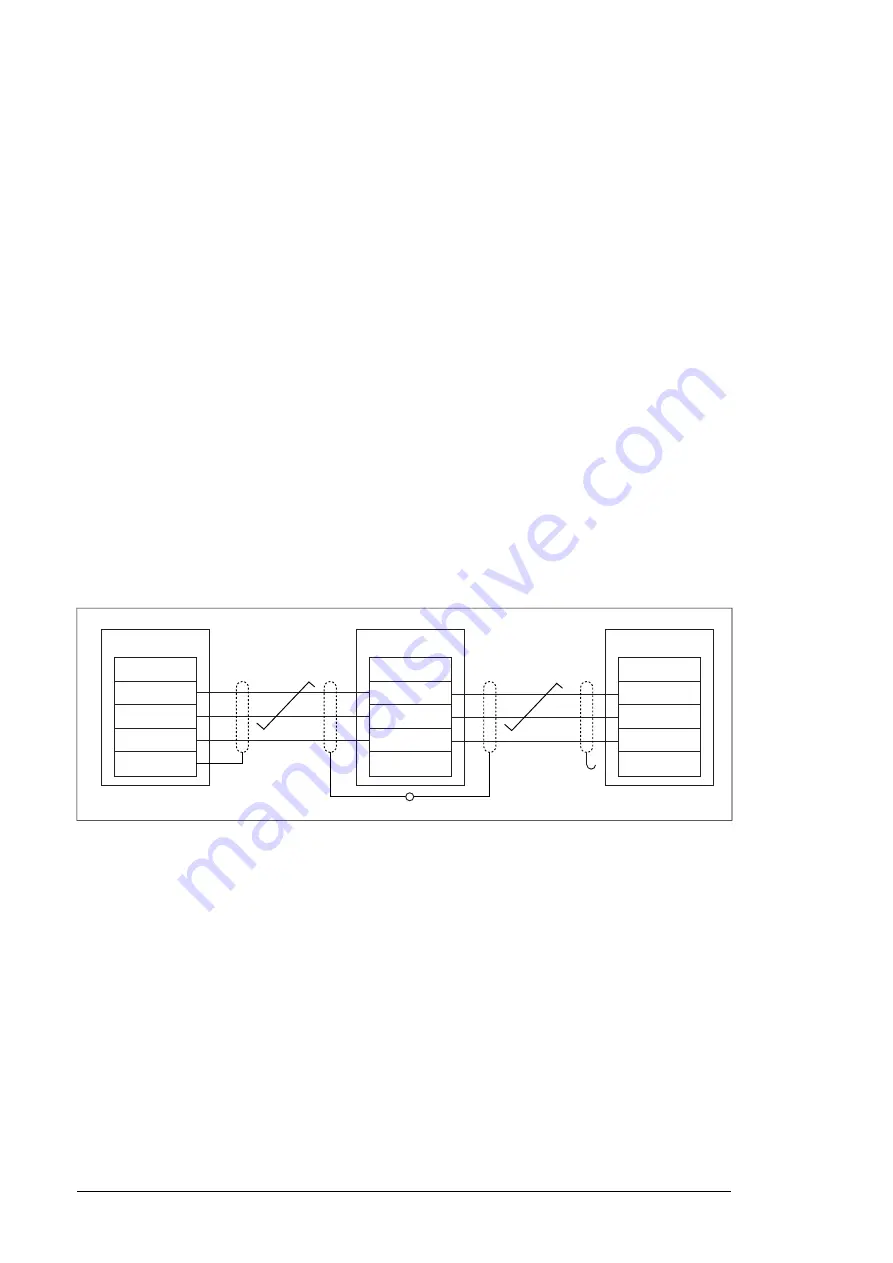
2) This input only acts as a true Safe torque off input in inverter control units. In other applications (such as a supply or brake
unit), de-energizing the IN1 and/or IN2 terminal will stop the unit but not constitute a true safety function.
3) Total load capacity of these outputs is 4.8 W (200 mA at 24 V) minus the power taken by DIO1 and DIO2.
4) Determines whether DICOM is separated from DIOGND (ie, common reference for digital inputs floats). ON: DICOM
connected to DIOGND. OFF: DICOM and DIOGND separate.
5) Current [0(4)…20 mA,
R
in
= 100 ohm] or voltage [0(2)…10 V,
R
in
> 200 kohm] input selected by switch AI2. Change of
setting requires reboot of control unit.
6) Current [0(4)…20 mA,
R
in
= 100 ohm] or voltage [0(2)…10 V,
R
in
> 200 kohm] input selected by switch AI1. Change of
setting requires reboot of control unit.
External power supply for the control unit (XPOW)
The control unit is powered from a 24 V DC, 2 A supply through terminal block XPOW. With
a type BCU control unit, a second supply can be connected to the same terminal block for
redundancy.
Using an external supply is recommended if
• the control unit needs to be kept operational during input power breaks, for example,
because of continuous fieldbus communication
• immediate restart is needed after a power break (that is, no control unit power-up delay
is allowed).
The X485 connector
The X485 provides a connection for optional CIO-01 I/O module. The following diagram
shows the wiring for the CIO module.
BCU
CIO
CIO
X485
B
A
BGND
SHIELD
X485
B
A
GND
SHIELD
X485
B
A
GND
SHIELD
Safe torque off (XSTO, XSTO OUT)
Note:
The XSTO input only acts as a true Safe torque off input on the inverter control unit.
De-energizing the IN1 and/or IN2 terminals of other units (supply, DC/DC converter, or brake
unit) will stop the unit but not constitute a true safety function.
FSO-xx safety functions module connection (X12)
See the user manual of the FSO-xx module. Note that the FSO-xx safety functions module
is not in use in supply, DC/DC converter or brake units.
SDHC memory card slot
The BCU-x2 has an on-board data logger that collects real-time data from the power modules
to help fault tracing and analysis. The data is stored onto the SDHC memory card inserted
into the SD CARD slot and can be analyzed by ABB service personnel.
52 The control unit
Summary of Contents for ACS880-607LC
Page 1: ... ABB INDUSTRIAL DRIVES ACS880 607LC 3 phase dynamic brake units Hardware manual ...
Page 2: ......
Page 4: ......
Page 10: ...10 ...
Page 30: ...30 ...
Page 34: ...34 ...
Page 46: ...46 ...
Page 56: ...56 ...
Page 72: ...7 After the module has drained disconnect the piping from the module 72 Maintenance ...
Page 88: ...88 ...
Page 95: ... Bottom entry and exit of cables Dimensions in mm 1 mm 0 0394 in Technical data 95 ...
Page 96: ...Dimensions in mm 1 mm 0 0394 in 96 Technical data ...
Page 97: ... Top entry and exit of cables Dimensions in mm 1 mm 0 0394 in Technical data 97 ...
Page 104: ...Brake unit with bottom exit Dimensions in mm 1 mm 0 0394 in 104 Dimension drawings ...
Page 105: ...Brake unit with top exit Dimensions in mm 1 mm 0 0394 in Dimension drawings 105 ...
Page 106: ...Bottom Top Dimensions in mm 1 mm 0 0394 in 106 Dimension drawings ...