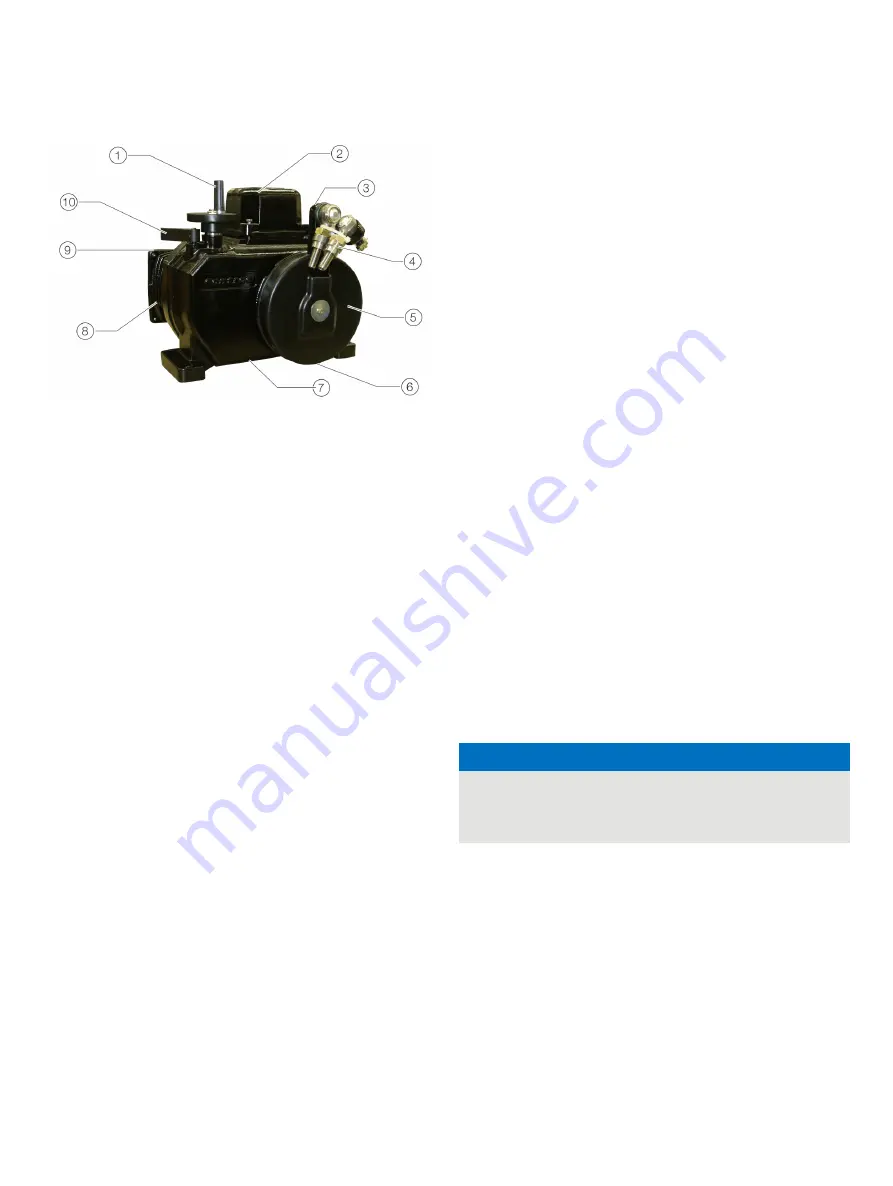
PME120-AI / PME120-AN (Contrac)
ELECTRICAL ROTARY ACTUATOR | SEI/PME120-EN REV. A
5
2
Introduction
1
Handwheel crank
2
Plug
3
Lever
4
Ball-and-socket joint
5
Lever cover
6
Adjustable stops
(under the lever cover)
7
Gear housing
8
Control motor
9
Cover (for PME120-AI incl.
electronic unit)
j
Handwheel release
Figure 1: PME120 (illustrations may differ from actual installation)
This service instruction refers to the ABB rotary actuators
PME120-AI (with integrated electronic unit) and PME120-AN (for
separate electronic unit).
It amends and deepens the routine maintenance description in
the standard instruction, which we strongly recommend being
also available for all maintenance work.
Safety and precautions
When mounting the actuator in areas which may be accessed by
unauthorized persons, take the required protective measures.
• The actuators perform movements for positioning vanes and
valves. Handle properly and with care. Otherwise, a hazard of
bruise injuries may arise.
• When changing the oil of the actuator, thoroughly remove
any oil that may have run down on the floor during the
procedure to avoid accidents.
• Dispose of the waste oil in compliance with the respective
local regulations. Make sure that no waste oil reaches the
water cycle.
• Only qualified specialists who have been trained for these
tasks are authorized to mount and adjust the control
actuator, and to make the electrical connection.
• When working on the actuator itself or the electronics always
observe the locally valid accident prevention regulations and
the regulations concerning the construction of technical
installations.
• Use the eye bolt at the actuator to lift or lower it. Only load it
vertically. Do not lift or lower the actuator when it is mounted
on a valve or similar final control element.
• Switch-off the voltage supply; make sure that unintentional
switching on is not possible.
• Make sure that switching off the power supply does not
affect the plant process.
• Make sure that the final control element is not exposed to
process forces.
Tools
NOTICE
Damage to the device due to improper tools!
Using improper tools may damage the actuator or its
components.
• Only use proper tools for maintenance work.
Note
• Maintenance at Contrac actuators requires tools which are
usually available in a workshop. Please consider that all
dimensions are based on the metrical system. This applies
also for the wrench sizes, threads etc.
• Use appropriate sleeves for the installation of the sealing
rings (see
Installation
on page 13 for details).