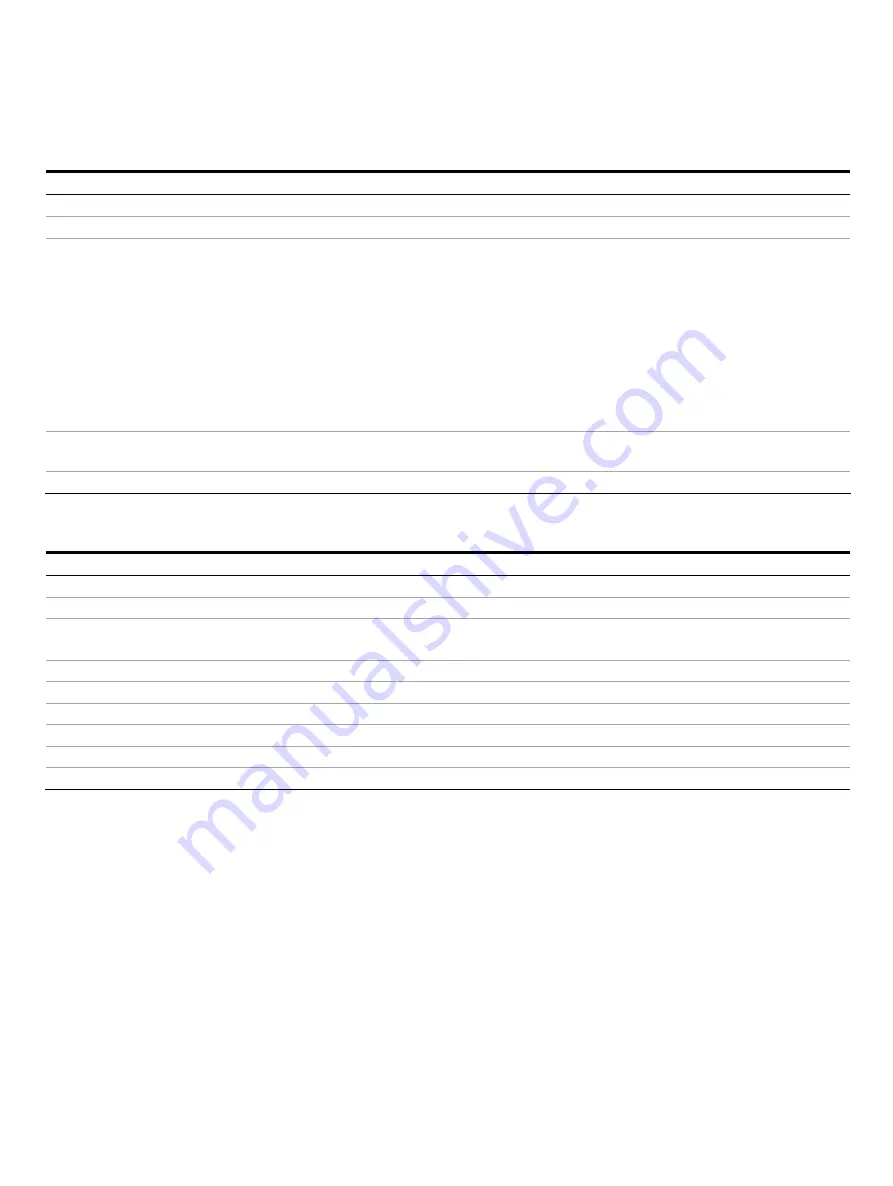
26
EAS822, EBS852, EBS862
ELECTRONIC UNIT | OI/EAS822/EBS852/EBS862-EN REV. D
… 6 Electrical connections
… Electrical data for inputs and outputs
EBS862
Supply voltage (standard actuators)
230 V AC (190 to 260 V); 47.5 to 63 Hz; single-phase
Supply voltage (Ex actuators)
230 V AC (190 to 253 V); 47.5 to 63 Hz; single-phase
Average power loss P
avg
and power consumption I
max
of the electronic unit
Actuator
P
avg
l
max
at 230 V
l
pos
(230 V):
approx. 40 to 50 % of l
max
RHD(E)2500-10
80 W
5.3 A
RHD(E)4000-10
100 W
10.0 A
RHD8000-12
115 W
8.0 A
RHDE8000-15
115 W
8.0 A
RHD(E)16000-30
115 W
12.5 A
RSD(E)50-10,0
100 W
6.4 A
RSD100-10.0
115 W
12.5 A
External fuse for electronic unit
Safety fuse 35 A (Lindner) + thermal circuit breaker 16 A (ETA)
(fuses are in the scope of delivery)
External fuse for heating (dewing protection)
2 to 6 A, medium time-lag
Binary inputs and outputs - communication
Conventional communication
Analog input
0 / 4 to 20 mA, internal load: 300
Ω
Analog output
0 / 4 to 20 mA, electrically isolated, maximum load: 500
Ω
3 digital inputs, 1 to 3
Digital
0: −3
to 5 V or open, electrically isolated
Digital 1: 12 to 35 V, electrically isolated
3 digital outputs, 1 to 3
Potential-free relay contact, max. 60 V, 150 mA
Digital communication
RS232 for commissioning and service, optionally FSK / HART®
Default settings
Conventional communication
on page 11
Voltage output U
V
24 V, 15 mA, electrically isolated, for scanning external contacts, or similar applications
Connection for transmitter (optional)
Supply for two-wire transmitter with activated process controller in Contrac
Individual settings
See data sheet ‘DS/CONTRAC/SETTING’ or available upon request.
Change from one to two columns