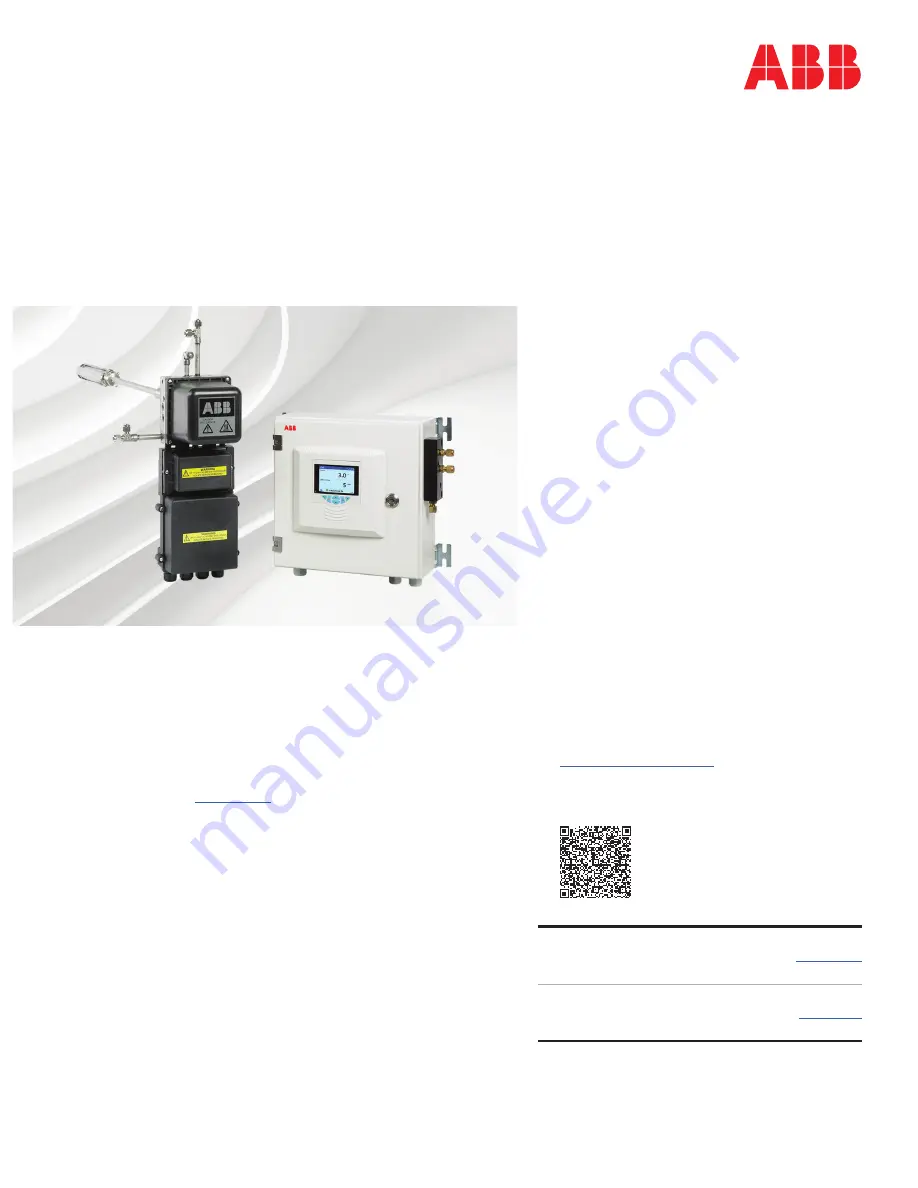
—
A B B ME A SUR EMENT & A N A LY TIC S | COMMISSIONING INSTRUC TION | CI/A Z4 0 - EN R E V. A
Endura AZ40
Oxygen and carbon monoxide equivalent (COe) analyzer
Measurement made easy
Introduction
This document provides unpacking, installation,
connection, setup and basic operation details for
the AZ40-EN analyzer system. For comprehensive
product details, refer to Operating instruction
OI/AZ40-EN
.
Contents
1 Overview / system dimensions .............................5
2 Environmental requirements .................................6
3 Mechanical installation ...........................................7
4 Electrical installation ............................................12
5 Pneumatic installation ..........................................18
6 System setup ..........................................................21
7 Calibration and sensor setup .............................. 28
8 Operation ............................................................... 30
9 Configuration (Advanced access level) ............. 34
For more information
Further publications for the Endura AZ40 analyzer
are available for free download from:
www.abb.com/analytical
(see links and reference numbers below) or by
scanning this code:
Search for or click on
Data Sheet
Endura AZ40
Oxygen and carbon monoxide
equivalent (COe) analyzer
DS/AZ40-EN
Operating Instruction
Endura AZ40
Oxygen and carbon monoxide
equivalent (COe) analyzer
OI/AZ40-EN
—
Oxygen and carbon
monoxide equivalent
analyzer