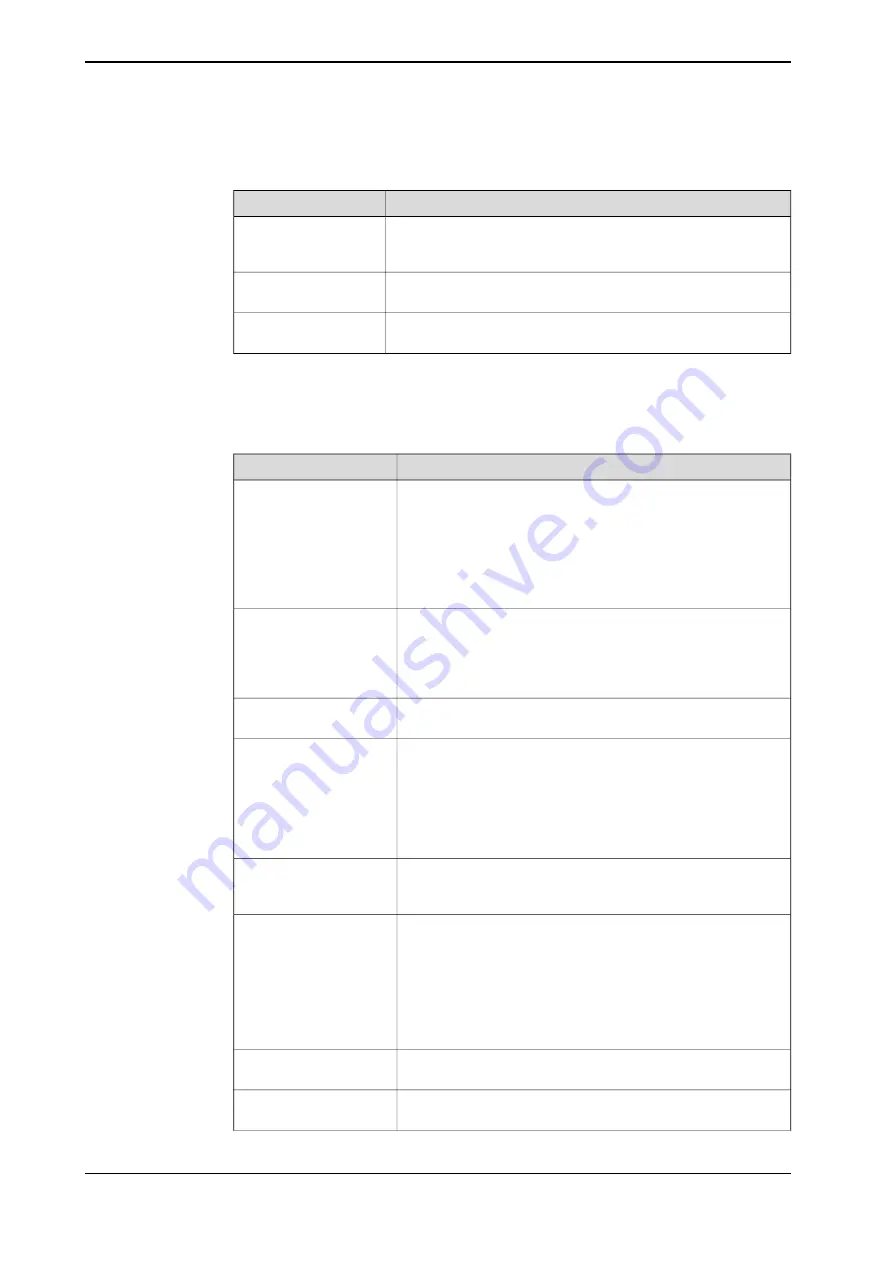
Routines that most probably need to be changed according to the specific
application are listed below:
Description
Routine
This is the main routine for
FlexLoader Vision Lite
. It checks for
entry request, maintenance request and other production breaking
conditions. Then it calls the state logic to decide what to do next.
PROC MainRoutine()
Operations that shall be done with the part after unloading from
machine tool. Change according application.
PROC PerformFinishin-
gOptions()
Operations that shall be done with the part prior to loading into
the machine tool. Change according application.
PROC PerformPrepare-
Options()
Machine tool handling procedures and functions
Note that the GLOBAL procedures (like LoadMachine_MAIN) are called from the
MainRoutine and perform logical work, whereas the LOCAL routines (like LoadMAIN)
perform the actual movement work.
Description
Name
This procedure is for moving the robot into the machine. Add
positions here if necessary.
LOCAL PROC EnterMa-
chine(\switch Grip-
per1FaceMAIN|switch
Gripper1FaceSUB)
In this example code, pViaMachine1/pViaMachine2 is a position
inside the machine where both chucks are reachable and the
gripper could turn around without crashing.
pViaMachine1 is placed with gripper 1 facing the main chuck.
pViaMachine2 is placed with gripper 1 facing the sub chuck.
This procedure is for moving the robot out of the machine. Add
positions here if necessary.
LOCAL PROC ExitMa-
chine(\switch Grip-
per1FaceMAIN|switch
Gripper1FaceSUB)
pViaMachine1/pViaMachine1 see above. In this example code,
pViaMachine is a position just outside the machine tool where
the robot can request the machine to close its door.
This procedure is for loading the main chuck in the machine
tool.
PROC LoadMa-
chine_MAIN()
This procedure loads the detail in the main chuck. Make sure
to use EnterMachine before all loading/unloading and ExitMa-
chine after all loading/unloading.
LOCAL PROC Load-
MAIN()
The load position is always calculated. X and Y is set to 0 and
Z is calculated with the help from FlexLoader Vision values. To
change the leave position, adjust wMainChuckM1 by running
the procedure CalibMainChuck.
This procedure unloads the sub chuck and then waits for the
machine to be ready before loading the main chuck and leaving
on the out belt.
PROC Synchroneous-
Mode()
This procedure unloads left over detail in main chuck. Make sure
to use EnterMachine before all loading/unloading and ExitMa-
chine after all loading/unloading.
LOCAL PROC Unloa-
dLeftOverPart()
The unload position is always calculated. X and Y is set to 0 and
Z is calculated with help from FlexLoader Vision values. To
change the unload position, the work object has to be adjusted
until the position is correct. In this case adjust wMainChuckM1
by running the procedure CalibMainChuck.
This procedure is for unloading the LeftOverPart from the ma-
chine tool.
PROC UnloadMa-
chine_LeftOverPart()
This procedure is for unloading the main chuck in the machine
tool.
PROC UnLoadMa-
chine_MAIN()
Continues on next page
266
Product manual - FlexLoader Vision
3HAC051771-001 Revision: B
© Copyright 2014-2018 ABB. All rights reserved.
B FlexLoader RAPID reference
B.3 FlexLoader application functionality
Continued
Summary of Contents for FlexLoader Vision
Page 1: ...ROBOTICS Product manual FlexLoader Vision ...
Page 8: ...This page is intentionally left blank ...
Page 12: ...This page is intentionally left blank ...
Page 14: ...This page is intentionally left blank ...
Page 16: ...This page is intentionally left blank ...
Page 62: ...This page is intentionally left blank ...
Page 96: ...This page is intentionally left blank ...
Page 180: ...This page is intentionally left blank ...
Page 218: ...This page is intentionally left blank ...
Page 286: ......
Page 287: ......