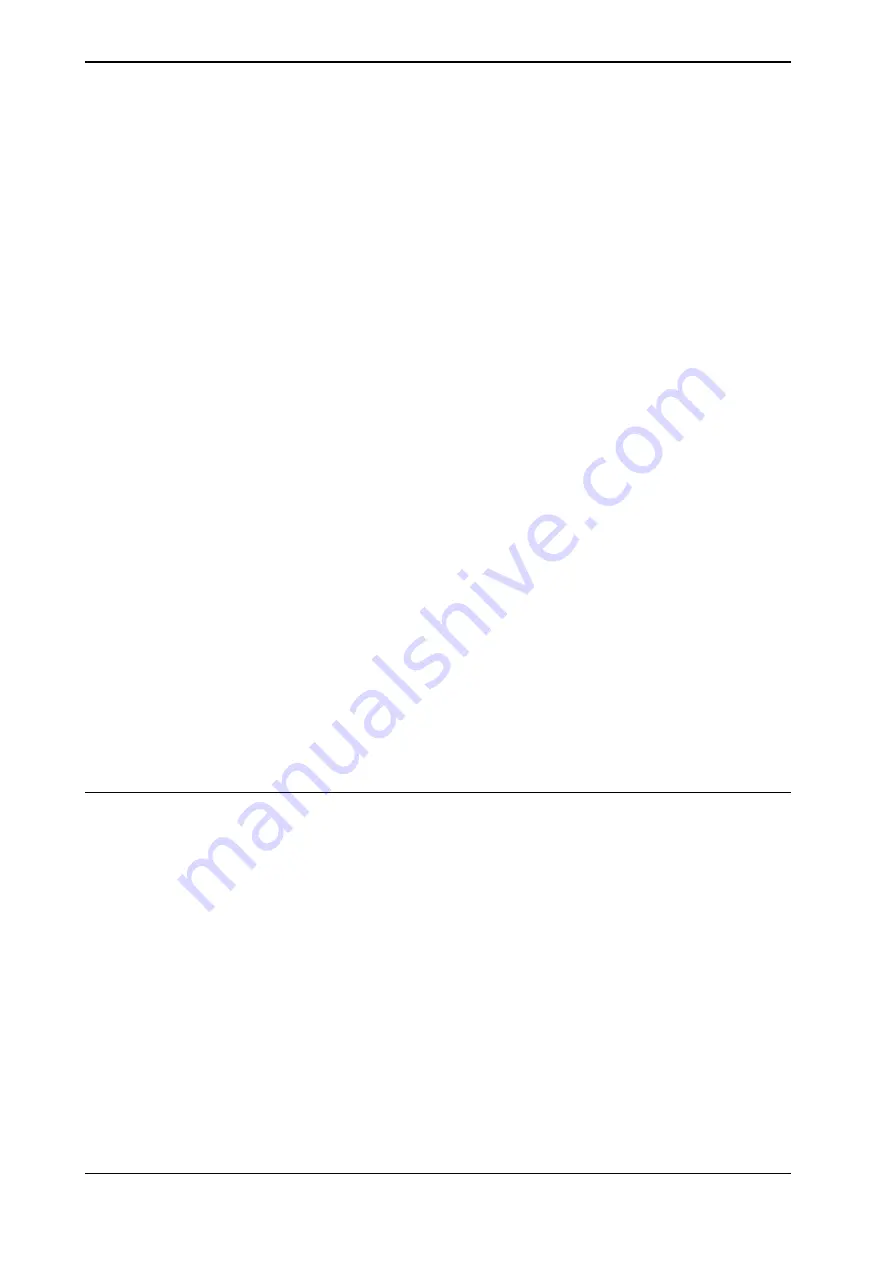
The image shows an example in which the result of filling the inner holes gives a
defective collision detection image for the detail.
Dirt suppression
The
Dirt suppression
setting filters out black marks on the conveyor, as these
often are only just dirt. Dirt suppression can thus improve the reliability of the
collision detection even on dirty conveyors. The higher dirt suppression level you
set, the stronger filter you get. However, note that if the value is set too high it may
also reject details, which may lead to collisions with the robot during gripping.
Gripper out-of-image control
If a position is close to the edge of the image it can often mean that the location
of the gripper would fall outside the field of view. If the gripper moves outside the
field of view this is normally regarded as a collision, since the system does not
know what is beyond the field of view. In some cases, however, it can be perfectly
safe to move the gripper outside certain areas of the field of view, as long as the
operator knows that there is no collision risk there.
The
Gripper out-of-image control
can be used to set dimensional tolerances for
positioning of the gripper outside the edges of the image. These tolerances can
be activated on the chosen edges. To do so, select the concerned
Tolerate outside
boxes and enter the required tolerance dimensions. The designations of the edges
(right, left, upper, lower) refer to the camera image that is seen on the screen.
Allowed overlap
If
Allowed overlap
is activated, the gripper is allowed to collide with objects in the
image to a certain extent. The degree of collision permitted is specified in square
millimetres. When tool collision is detected, FlexLoader Vision will compare the
collision area with the specified, permitted overlap area.
If the collision covers less than the overlap area, the robot is permitted to pick the
detail. For example, this can be used if the grip fingers are permitted to knock away
nearby details when picking.
Advanced parameter settings for secondary search
Click
Advanced
under
Detail supervision
>
Secondary search
on the
Supervision
tab to open and edit the advanced parameter settings for secondary searches.
Enter lower agreement values for the teachin model in order to find more details
than those approved for picking.
88
Product manual - FlexLoader Vision
3HAC051771-001 Revision: B
© Copyright 2014-2018 ABB. All rights reserved.
5 Advanced teachin settings
5.5 Advanced supervision settings
Continued
Summary of Contents for FlexLoader Vision
Page 1: ...ROBOTICS Product manual FlexLoader Vision ...
Page 8: ...This page is intentionally left blank ...
Page 12: ...This page is intentionally left blank ...
Page 14: ...This page is intentionally left blank ...
Page 16: ...This page is intentionally left blank ...
Page 62: ...This page is intentionally left blank ...
Page 96: ...This page is intentionally left blank ...
Page 180: ...This page is intentionally left blank ...
Page 218: ...This page is intentionally left blank ...
Page 286: ......
Page 287: ......