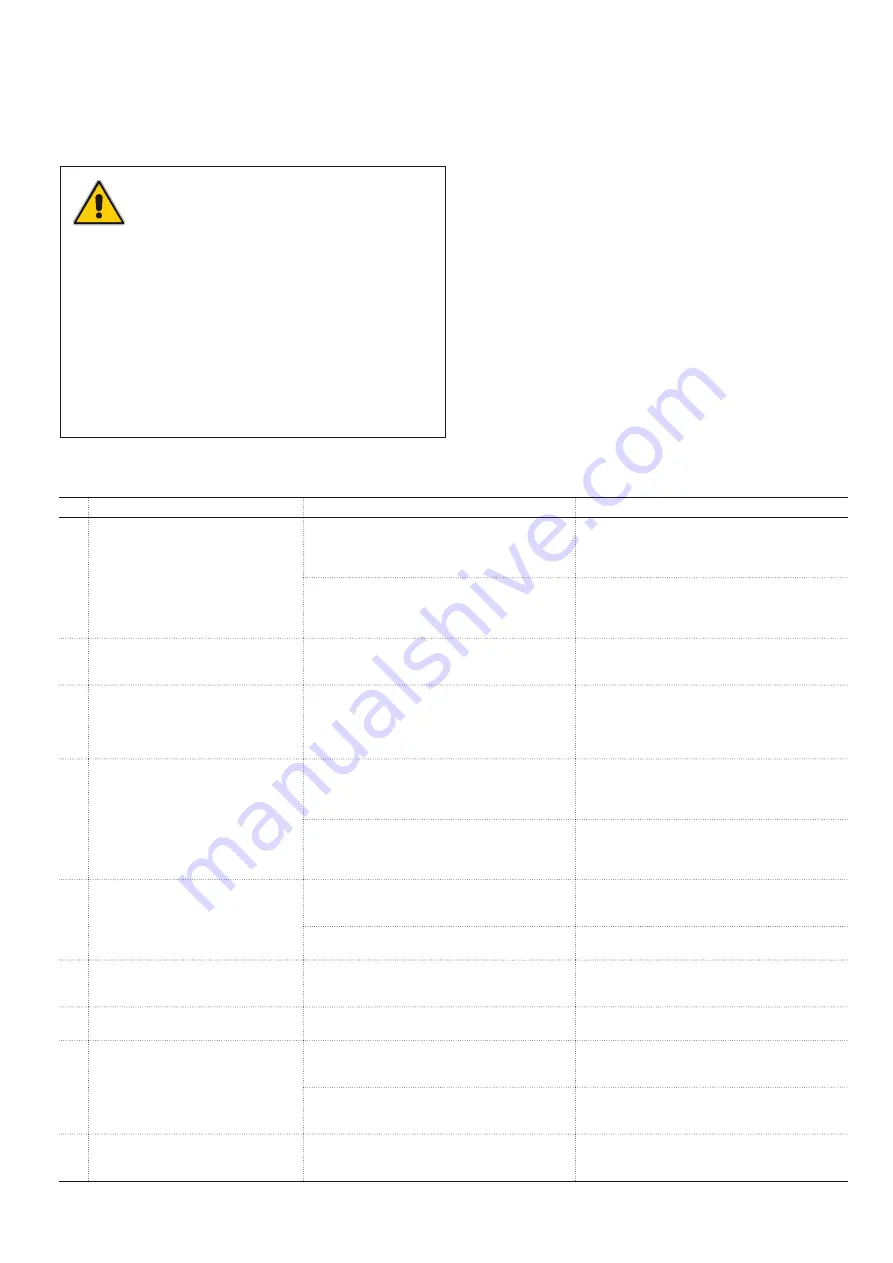
31
Carry out the following operations before putting the circuit-
breaker into service:
– make sure that the power connections to the circuit-break-
er terminals are tight;
– establish the setting of the primary electronic overcurrent
release (if provided);
– make sure that the value of the power supply voltage of the
auxiliary circuits is between 85% and 110% of the rated
voltage of the electrical applications;
– make sure that there are no foreign bodies, such as bits of
packing, in the moving parts;
– to avoid overtemperatures, make sure that there is a suf-
ficient exchange of air in the place of installation;
– also perform the inspections indicated in the following ta-
ble:
8. Putting into service
All the operations for putting into service
must be carried out by ABB personnel or by
the customer’s qualified personnel.
If the operations are obstructed in any way,
do not force the mechanical interlocks and
check that the operating sequence is correct.
The operating forces which can be applied
are indicated in paragraph 6.3.
Discharge the closing springs (close and
open the circuit-breaker) to access the inside
of the operating mechanism.
Disconnect the PR521 release (if provided)
before conducting insulation tests on the
circuit-breaker.
8.1 General procedures
Subject of the inspection
Procedure
Positive check
1
Insulation resistance.
Medium voltage circuit
Using a 2500 V Megger, measure the insulation
resistance between the phases and between
phases and earth the circuit.
The insulation resistance should be at least 50 M
Ω
and must remain constant over time.
Auxiliary circuits
Using a 500 V Megger (installed equipment
permitting), measure the insulation resistance
between the auxiliary circuits and the earth.
The insulation resistance should be several M
Ω
and
must remain constant over time.
2
Auxiliary circuits.
Make sure that the connections to the control
circuit are correct: proceed with the relative power
supply.
Normal operations and signals.
3
Manual operating mechanism.
Perform a few closing and opening operations (see
chap. 6).
NOTE.
Power the undervoltage release and the
locking magnet on the operating mechanism at the
relative rated voltage (if provided).
The operations and relative signals occur correctly.
4
Motor operator (if provided)
Power the spring loading gearmotor at the relative
rated voltage.
The springs are loaded correctly.
The signals are correct.
The gearmotor stops when the springs have been
loaded.
Perform a few closing and opening operations.
NOTE.
Power the undervoltage release and the
locking magnet on the operating mechanism at the
relative rated voltage (if provided).
The gearmotor reloads the springs after each
closing operation.
5
Undervoltage release (if provided).
Power the undervoltage release at the relative rated
voltage and perform the circuit-breaker closing
operation.
The circuit-breaker closes correctly.
The signals are correct.
Disconnect the power supply to the release.
The circuit-breaker opens.
The signal changes over.
6
Opening release.
Close the circuit-breaker.
Power the shunt opening release at the relative
rated voltage.
The circuit-breaker opens correctly.
The signals are correct.
7
Shunt closing release (if provided).
Open the circuit-breaker. Power the shunt closing
release at the relative rated voltage.
The circuit-breaker closes correctly.
The signals are correct.
8
Key lock.
Open the circuit-breaker.
Turn the key and remove it.
Attempt the circuit-breaker closing operation.
Neither manual nor electric closing takes place.
Insert the key again and turn it through 90°.
Perform the closing operation.
Both electric and manual closing take place
correctly; in this position the key cannot be
removed.
9
Auxiliary contacts in the operating
mechanism
Insert the auxiliary contacts into suitable signalling
circuits.
Perform a few closing and opening operations.
The signals occur correctly.
Summary of Contents for HD4/R
Page 2: ......
Page 21: ...21 7 9 Overall dimensions 7 9 1 Fixed HD4 R 12 24 kV 630 1250 A TN 7237 Figure 9 ...
Page 22: ...22 7 9 2 Fixed HD4 R 12 24 kV 630 1250 A TN 7234 Figure 10 ...
Page 24: ...24 7 9 4 Plug in HD4 S 12 24 kV 630 1250 A TN 7236 Figure 12 ...
Page 25: ...25 7 9 5 HD4 Uniair 12 24 kV 630 1250 A TN 7235 Figure 13 ...
Page 26: ...26 7 9 6 HD4 Uniair F 12 24 kV 630 A TN 7275 Figure 14 ...
Page 27: ...27 7 9 7 HD4 Uniair 2R 12 24 kV 630 1250 A TN 7274 Figure 15 ...
Page 28: ...28 7 9 8 HD4 Uniair A 12 24 kV 630 1250 A TN 7273 Figure 16 ...
Page 29: ...29 7 9 9 HD4 UniMix F 12 24 kV 630 1250 A TN 7366 Figure 17 ...
Page 30: ...30 7 9 10 HD4 R SEC 12 24 kV 630 800 A 1VCD003536 Figure 18 ...
Page 37: ......