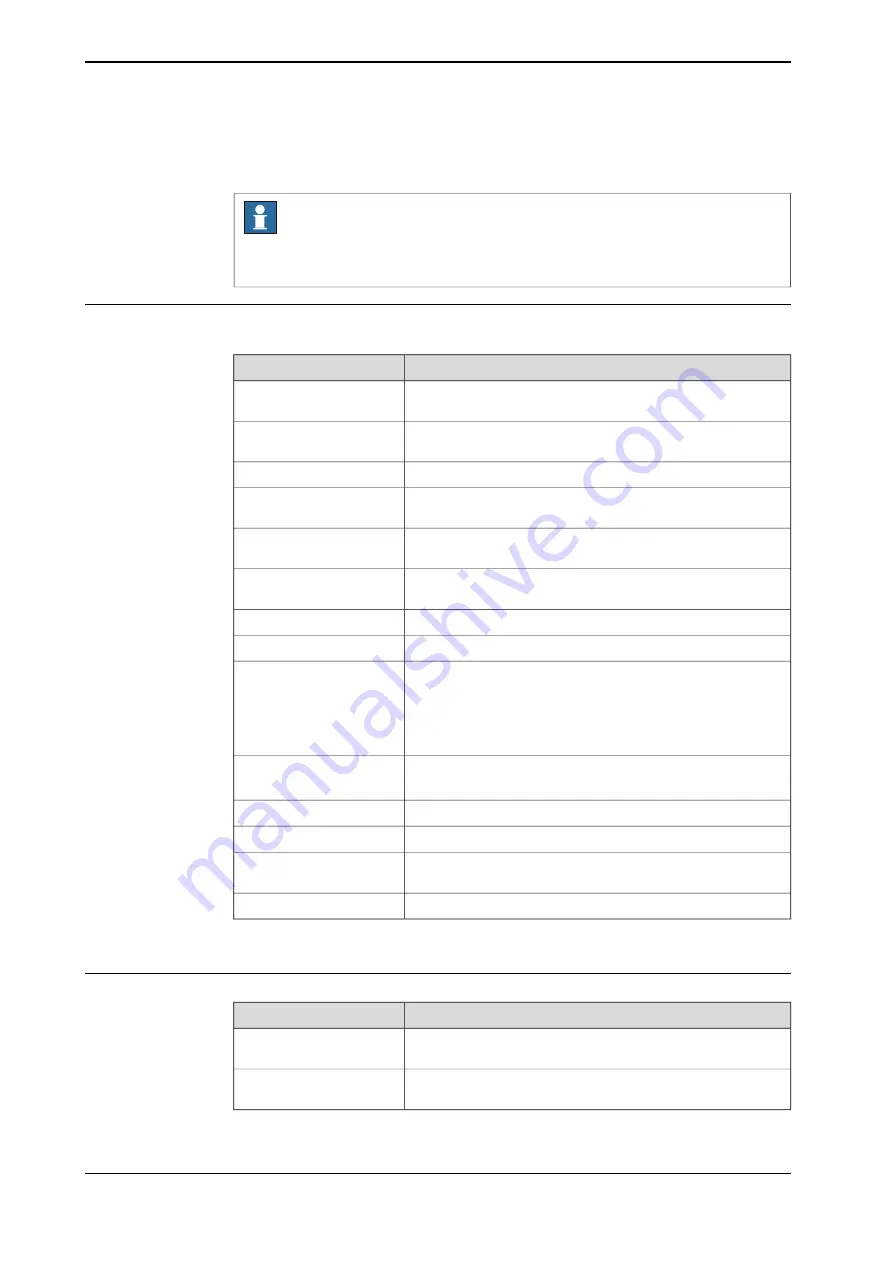
8.2 Applicable standards
Note
The listed standards are valid at the time of the release of this document. Phased
out or replaced standards are removed from the list when needed.
Standards, EN ISO
The product is designed in accordance with the requirements of:
Description
Standard
Safety of machinery - General principles for design - Risk as-
sessment and risk reduction
EN ISO 12100:2010
Safety of machinery, safety related parts of control systems -
Part 1: General principles for design
EN ISO 13849-1:2015
Safety of machinery - Emergency stop - Principles for design
EN ISO 13850:2015
Robots for industrial environments - Safety requirements -Part
1 Robot
EN ISO 10218-1:2011
Robots and robotic devices -- Coordinate systems and motion
nomenclatures
ISO 9787:2013
Manipulating industrial robots, performance criteria, and related
test methods
ISO 9283:1998
Classification of air cleanliness
EN ISO 14644-1:2015
i
Ergonomics of the thermal environment - Part 1
EN ISO 13732-1:2008
EMC, Generic emission
EN 61000-6-4:2007 +
A1:2011
IEC 61000-6-4:2006 +
A1:2010
(option 129-1)
EMC, Generic immunity
EN 61000-6-2:2005
IEC 61000-6-2:2005
Arc welding equipment - Part 1: Welding power sources
EN IEC 60974-1:2012
ii
Arc welding equipment - Part 10: EMC requirements
EN IEC 60974-10:2014
Safety of machinery - Electrical equipment of machines - Part
1 General requirements
EN IEC 60204-1:2006
Degrees of protection provided by enclosures (IP code)
IEC 60529:1989 + A2:2013
i
Only robots with protection Clean Room.
ii
Only valid for arc welding robots. Replaces EN IEC 61000-6-4 for arc welding robots.
European standards
Description
Standard
Safety of machinery - Ergonomic design principles - Part 1:
Terminology and general principles
EN 614-1:2006 + A1:2009
Safety of machinery - Two-hand control devices - Functional
aspects - Principles for design
EN 574:1996 + A1:2008
Continues on next page
376
Product manual - IRB 1600/1660
3HAC026660-001 Revision: W
© Copyright 2006-2018 ABB. All rights reserved.
8 Reference information
8.2 Applicable standards
Summary of Contents for IRB 1600
Page 1: ...ROBOTICS Product manual IRB 1600 1660 ...
Page 8: ...This page is intentionally left blank ...
Page 18: ...This page is intentionally left blank ...
Page 48: ...This page is intentionally left blank ...
Page 152: ...This page is intentionally left blank ...
Page 336: ...This page is intentionally left blank ...
Page 372: ...This page is intentionally left blank ...
Page 388: ...This page is intentionally left blank ...
Page 396: ......
Page 397: ......