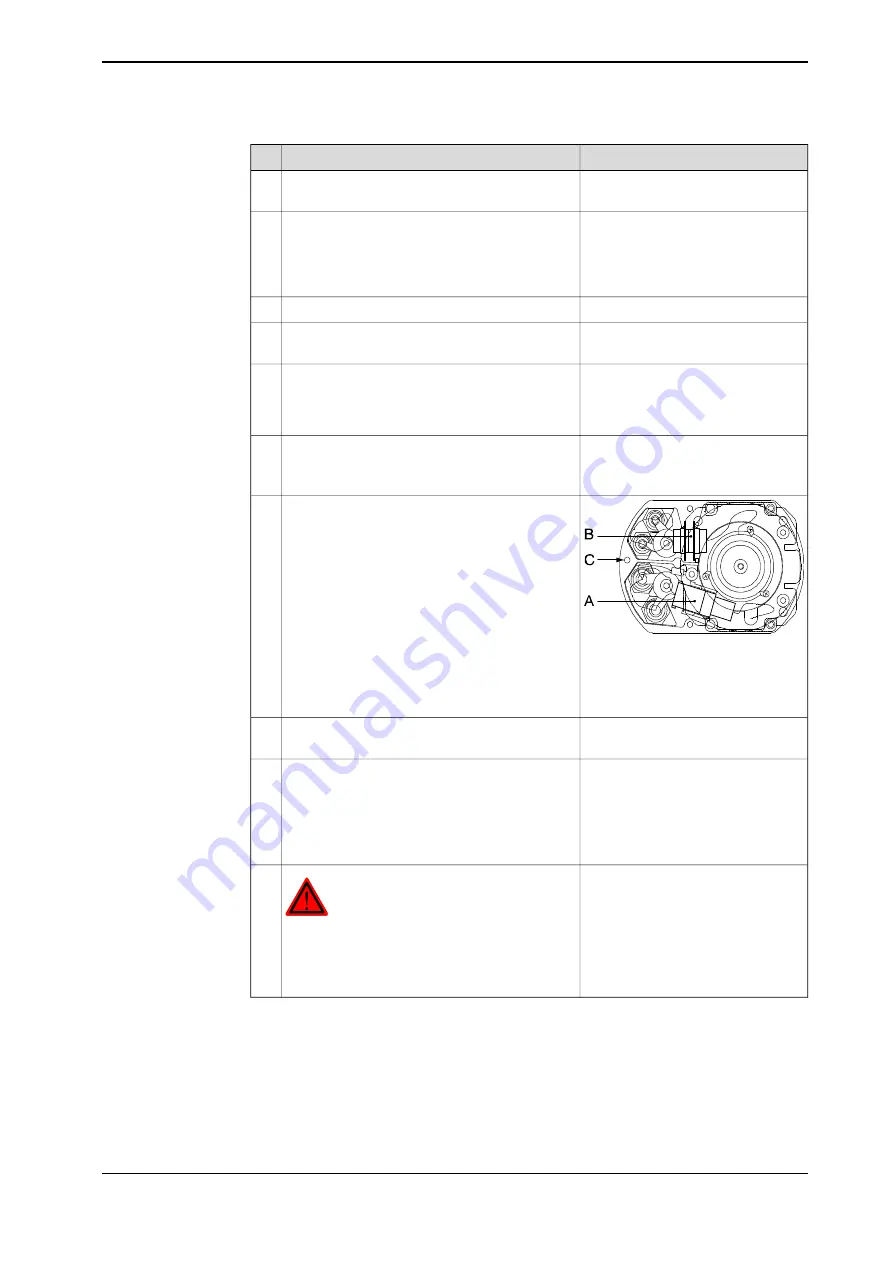
Note/Illustration
Action
See the figure above.
Pull gently in one direction. Note the reading.
(The gear must not turn.)
11
See the figure above.
Then gently knock on the tool in the other direc-
tion and note the reading. The difference in
reading = gear play. The gear play should be
0.02 mm which corresponds to a reading on the
dial indicator of 0.13 mm.
12
4 pcs. Tightening torque: 35 Nm.
Tighten the four attachment screws.
13
Detailed in section
.
Perform a leak-down test.
14
Where to find type of oil and total
amount is detailed in
amount of oil in gearboxes on
page 92
Fill the gearbox with oil.
15
Shown in the figure
.
Refit the
connection box
and secure with the
three attachment screws and plain washers.
Make sure that the gasket is fitted properly!
16
xx0200000401
Reconnect connectors R3.MP2 and R3.FB2.
17
•
A: R3.MP2
•
B: R3.FB2
•
C: Connection box
Shown in the figure
.
Refit the
cover
of the connection box.
18
Calibration is detailed in a separate
calibration manual enclosed with the
calibration tools.
Re-calibrate the robot.
19
General calibration information is in-
cluded in the section
DANGER
Make sure all safety requirements are met when
performing the first test run. These are further
detailed in the section
20
Product manual - IRB 2400
177
3HAC022031-001 Revision: P
© Copyright 2004-2018 ABB. All rights reserved.
4 Repair
4.7.2 Replacement of motor, axis 2
Continued
Summary of Contents for IRB 2400 Series
Page 1: ...ROBOTICS Product manual IRB 2400 ...
Page 8: ...This page is intentionally left blank ...
Page 18: ...This page is intentionally left blank ...
Page 204: ...This page is intentionally left blank ...
Page 220: ...This page is intentionally left blank ...
Page 232: ...This page is intentionally left blank ...
Page 234: ...This page is intentionally left blank ...
Page 240: ......
Page 241: ......