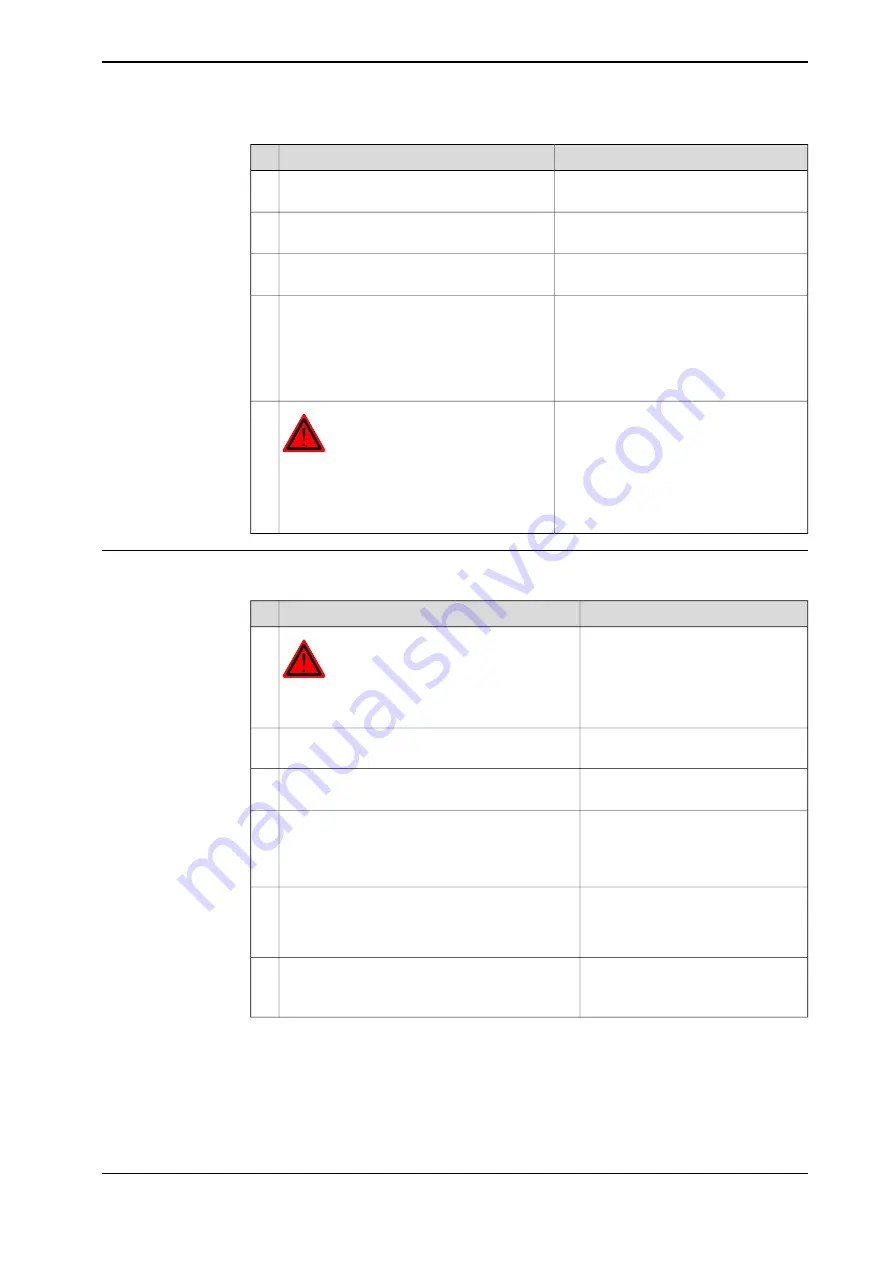
Note/Illustration
Action
Detailed in section
Perform a leak-down test.
11
Art. no. and amount is specified in
.
Refill the axis 4 gearbox with
lubricating oil
.
12
Detailed in section
Reconnect the cabling.
13
Calibration is detailed in a separate calib-
ration manual enclosed with the calibra-
tion tools.
Recalibrate the robot.
14
General calibration information is in-
cluded in the section
DANGER
Make sure all safety requirements are met
when performing the first test run. These are
further detailed in the section
may cause injury or damage on page 29
15
Refitting, motor axis 5
The procedure below details how to refit the motor, axis 5.
Note
Action
DANGER
Turn off all electric power, hydraulic and pneu-
matic pressure supplies to the robot!
1
Check that the assembly surfaces are clean and
the motor unscratched.
2
Spare part no. is specified in
Fit a new
o-ring
on the motor.
3
Look at the figure in the procedure
Refitting, motor axis 4 on page 186
Fit the
measuring tool
at the rear of the motor.
4
Art. no. is specified in
.
The motor’s fixing screws shall be fastened, but
do not tighten them, to ensure that the motor will
be able to move parallel to the gear when the
adjustment is done.
5
Connector to connector R3.MP5:
•
+ : pin 7
•
-: pin 8
In order to release the brakes, connect the 24
VDC power supply to the motor.
6
Continues on next page
Product manual - IRB 2400
187
3HAC022031-001 Revision: P
© Copyright 2004-2018 ABB. All rights reserved.
4 Repair
4.7.4 Replacement of motors, axes 4-6, IRB 2400L
Continued
Summary of Contents for IRB 2400 Series
Page 1: ...ROBOTICS Product manual IRB 2400 ...
Page 8: ...This page is intentionally left blank ...
Page 18: ...This page is intentionally left blank ...
Page 204: ...This page is intentionally left blank ...
Page 220: ...This page is intentionally left blank ...
Page 232: ...This page is intentionally left blank ...
Page 234: ...This page is intentionally left blank ...
Page 240: ......
Page 241: ......