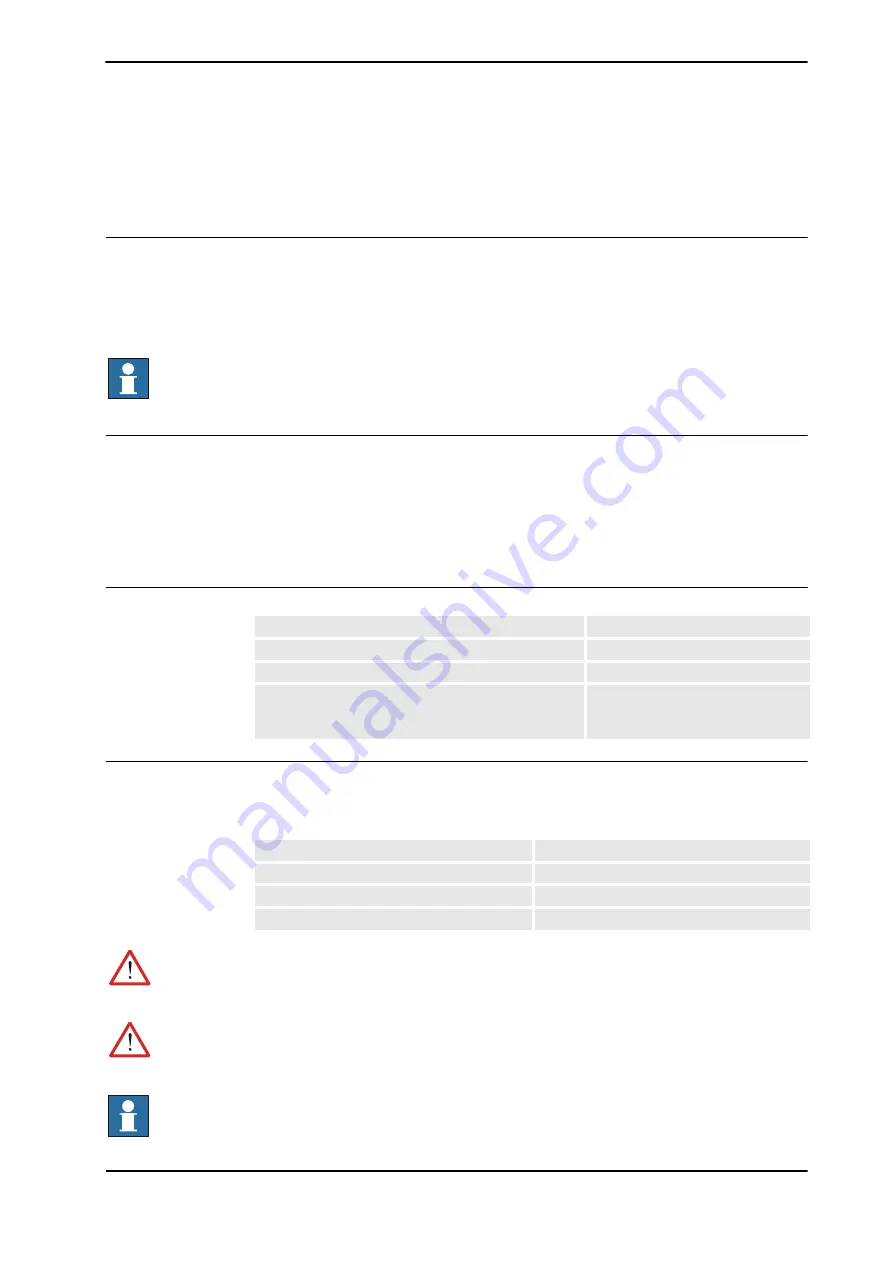
2 Installation and commissioning
2.6.1. Installation of IRB4400 in a water jet application
81
3HAC022032-001 Revision: E
© Copyri
ght
200
4-2008 ABB.
All rights reserved.
2.6 Additional installation (Foundry Prime)
2.6.1. Installation of IRB4400 in a water jet application
General
Robots delivered with the Foundry Prime protection are specially designed to work in water
jet cleaning cells with 100% humidity and alkaline detergent. To ensure that the protection
offers the best reliability, some measures are needed during installation of the robot according
to the procedures below.
For best reliability, it is also of highest importance that the special maintenance instructions
for the Foundry Prime robot are followed and documented.
Commissioning
•
Never switch off the overpressure in motors and serial measurement compartment
during cooling down of robot after it has been switched off.
•
When turning off an cleaning cell we recommend that the humid air inside a cell is
ventilated out, to avoid that the humid air is sucked into e.g. gearboxes due to the
raised vacuum when cooled down.
Environmental conditions
Air specification for pressurizing of robot
The air must be dry and clean, such as instrument air. Following table details the air
specification.
If the pressurized air contains oil, it could result in a brake failure in the motors and cause the
robot arms to fall down, leding to personal injure or physical damage.
If the air pressure exceeds the specified, it could result in a brake failure in the motors and
cause the robot arms to fall down, leding to personal injure or physical damage.
To secure sufficient air pressure, it is recommended to use a pressure sensor.
Humidity
100%
Washing detergent with pH
<9.0
Washing detergent must be approved by ABB.
Cleaning bath temperature
<60°C, used in a typical waterjet
cleaning application at suitable
speed.
Dew point
<+2°C at 6 bar
Solid particle size
<5 microns
Oil content
<1 ppm (1 mg/m3)
Pressure to robot
0.2-0.3 bar
Continues on next page
Summary of Contents for IRB 4400 - 45
Page 2: ......
Page 8: ...Table of Contents 6 3HAC022032 001 Revision E Copyright 2004 2008 ABB All rights reserved ...
Page 296: ......
Page 297: ... Copyright 2004 2006 ABB All rights reserved Foldout 1 ...
Page 298: ... Copyright 2004 2006 ABB All rights reserved Foldout 2 ...
Page 299: ... Copyright 2004 2006 ABB All rights reserved Foldout 3 1 ...
Page 301: ... Copyright 2004 2006 ABB All rights reserved Foldout 4 ...
Page 302: ... Copyright 2004 2006 ABB All rights reserved Foldout 5 ...
Page 303: ... Copyright 2004 2006 ABB All rights reserved Foldout 6 1 ...
Page 304: ... Copyright 2004 2006 ABB All rights reserved Foldout 6 2 ...
Page 305: ... Copyright 2004 2006 ABB All rights reserved Foldout 6 3 ...
Page 307: ... Copyright 2004 2006 ABB All rights reserved Foldout 8 ...
Page 313: ... Copyright 2004 2006 ABB All rights reserved Motor Axis 1 3 Sheet 103 ...
Page 314: ... Copyright 2004 2006 ABB All rights reserved Feed Back Axis 1 3 Sheet 104 ...
Page 315: ... Copyright 2004 2006 ABB All rights reserved Motor Axis 4 6 Sheet 105 ...
Page 316: ... Copyright 2004 2006 ABB All rights reserved Feed Back Axis 4 6 Sheet 106 ...
Page 317: ... Copyright 2004 2006 ABB All rights reserved Customer Connection Sheet 107 ...
Page 318: ... Copyright 2004 2006 ABB All rights reserved Pos Indicator Axis 1 Option Sheet 108 ...
Page 321: ......