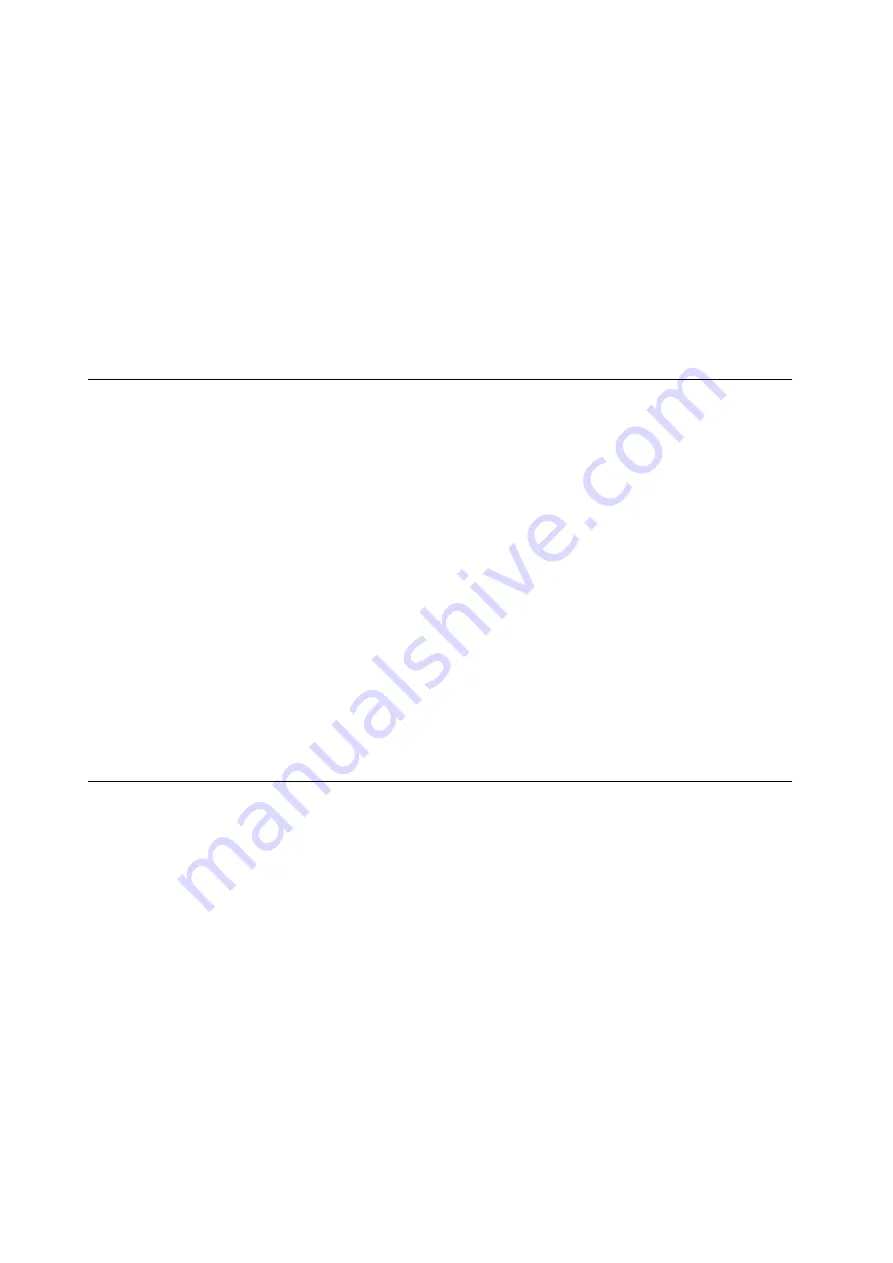
Safety System
System Description
20
Product Manual
If any of the dual switches in the safety circuit are opened, the circuit breaks, the motor
contactors drop out, and the robot is stopped by the brakes. If the safety circuit breaks,
an interrupt call is sent directly from the panel unit to the robot computer to ensure that
the cause of the interrupt is indicated.
When the robot is stopped by a limit switch, it can be moved from this position by jogging
it with the joystick while pressing the MOTORS ON button. The MOTORS ON button is
monitored and may be depressed for a maximum of 30 seconds.
LEDs for ES, AS and GS are connected to the two safety circuits to enable quick location
of the position where the safety chain is broken. The LEDs are located on the upper part of
the panel unit. Status indication is also available on the teach pendant display.
5.2 MOTORS ON and MOTORS OFF modes
The principle task of the safety circuit is to ensure that the robot goes into MOTORS
OFF mode as soon as any part of the chain is broken. The robot computer itself controls
the last switches (ENABLE and MOTORS ON).
In AUTO mode, you can switch the robot back on by pressing the MOTORS ON button on
the operator’s panel. If the circuit is OK, the robot computer then closes the MOTORS ON
relay to complete the circuit. When switching to MANUAL, the mode changes to
MOTORS OFF, at which stage the robot computer also opens the MOTORS ON relay. If
the robot mode does not change to MOTORS OFF, the ENABLE chain will break and the
ENABLE relay is opened. The safety circuit can thus be broken in two places by the robot
computer.
In any of the MANUAL modes, you can start operating again by pressing the enabling
device on the teach pendant. If the circuit is OK, the robot computer then closes the
MOTORS ON relay to complete the circuit. The function of the safety circuit can be
described as a combination of mechanical switches and robot computer controlled
relays which are all continuously monitored by the robot computer.
5.3 Safety stop signals
According to the safety standard ISO/DIS 11161 “Industrial automation systems -
safety of integrated manufacturing systems - Basic requirements”, there are two cate-
gories of safety stops, category 0 and category 1, see below:
The category 0 stop is to be used for safety analysis purposes, when the power supply to the
motors must be switched off immediately, such as when a light curtain, used to protect
against entry into the work cell, is passed. This uncontrolled motion stop may require spe-
cial restart routines if the programmed path changes as a result of the stop.
Category 1 is preferred for safety analysis purposes, if it is acceptable, such as when
gates are used to protect against entry into the work cell. This controlled motion stop
takes place within the programmed path, which makes restarting easier.
All the robot’s safety stops are category 0 stops as default.
Safety stops of category 1 can be obtained by activating the soft stop (delayed stop)
together with AS or GS. Activation is made by setting a parameter, see User’s Guide,
section System Parameters, Topic: Controller.
Summary of Contents for IRB 6400R
Page 4: ...Description 20 Product Specification IRB 1400 M97A BaseWare OS 3 0 ...
Page 6: ...Introduction 2 Product Manual ...
Page 10: ...Introduction 6 Product Manual ...
Page 12: ...Product Specification IRB 6400R 2 Product Specification IRB 6400R M99 BaseWare OS 3 2 ...
Page 78: ...Accessories 68 Product Specification IRB 6400R M99 BaseWare OS 3 2 ...
Page 80: ...Product Specification RobotWare 2 Product Specification RobotWare for BaseWare OS 3 2 ...
Page 82: ...Introduction 4 Product Specification RobotWare for BaseWare OS 3 2 ...
Page 104: ...Interbus S 3 2 26 Product Specification RobotWare for BaseWare OS 3 2 ...
Page 110: ...I O Plus 3 2 32 Product Specification RobotWare for BaseWare OS 3 2 ...
Page 128: ...PalletWare 50 Product Specification RobotWare for BaseWare OS 3 2 ...
Page 132: ...Safety 2 Product Manual ...
Page 148: ...System Description CONTENTS Page 2 Product Manual ...
Page 158: ...Structure System Description 12 Product Manual ...
Page 160: ...Computer System System Description 14 Product Manual ...
Page 164: ...I O System System Description 18 Product Manual ...
Page 168: ...Safety System System Description 22 Product Manual ...
Page 170: ...External Axes System Description 24 Product Manual ...
Page 174: ...Installation and Commissioning CONTENTS Page 4 Product Manual IRB 6400R ...
Page 196: ...On Site Installation Installation and Commissioning 26 Product Manual IRB 6400R ...
Page 270: ...Installing the Control Program Installation and Commissioning 100 Product Manual IRB 6400R ...
Page 292: ...Maintenance CONTENTS Page 2 Product Manual IRB 6400R ...
Page 299: ...Maintenance Product Manual IRB 6400R 9 Figure 4 Lubricating gearbox axis 1 4 3 1 2 ...
Page 312: ...Troubleshooting Tools CONTENTS Page 2 Product Manual ...
Page 350: ...Troubleshooting Tools 40 Product Manual ...
Page 352: ...Fault tracing guide 2 Product Manual ...
Page 362: ...Fault tracing guide 12 Product Manual ...
Page 375: ...Motor units Repairs 12 Product Manual IRB 6400R ...
Page 401: ...Arm System Repairs 38 Product Manual IRB 6400R ...
Page 409: ...Cabling Repairs 46 Product Manual IRB 6400R ...
Page 441: ...Special Tools List Repairs 80 Product Manual IRB 6400R ...
Page 479: ...Part List and Spare Parts Product Manual IRB 6400R 38 ...
Page 480: ...Part List and Spare Parts Product Manual IRB 6400R 39 ...
Page 481: ...Part List and Spare Parts Product Manual IRB 6400R 40 ...