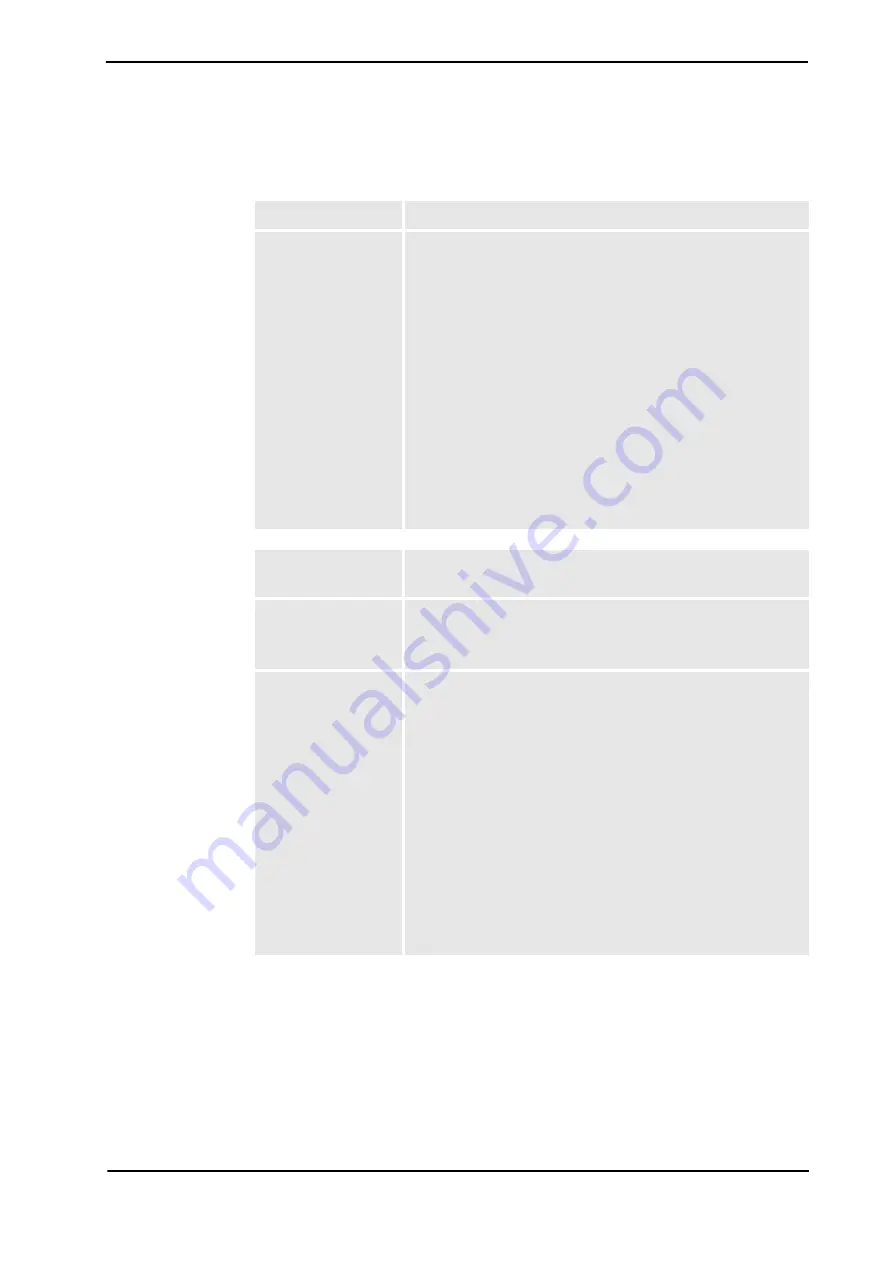
1 Description
1.2.1 Standards
3HAC 025861-001
Rev.E
11
The robot complies fully with the health and safety standards specified in the EEC’s
Machinery Directives.
Safety function
Description
The Service
Information System
(SIS)
The service information system gathers information about the
robot’s usage and determines how hard the robot is used. The
usage is characterized by the speed, the rotation angles and the
load of every axis.
With this data collection, the service interval of every individual
robot of this generation can be predicted, optimized and service
activities planned ahead. The collection data is available via the
FlexPendant or the network link to the robot.
The Process Robot Generation is designed with absolute safety in
mind. It is dedicated to actively or passively avoid collisions and
offers the highest level of safety to the operators and the machines
as well as the surrounding and attached equipment. These features
are presented in the active and passive safety system.
The time the robot is in operation (brakes released) is indicated on
the FlexPendant. Data can also be monitored over network, using
e.g. WebWare.
The Active Safety
System
Description
General
The active safety system includes those software features that
maintain the accuracy of the robot’s path and those that actively
avoid collisions which can occur if the robot leaves the programmed
path accidentally or if an obstacle is put into the robot’s path.
The Active Brake
System (ABS)
All robots are delivered with an active brake system that supports
the robots to maintain the programmed path in General Stop (GS),
Auto Stop (AS) and Superior Stop (SS).
The ABS is active during all stop modes, braking the robot to a stop
with the power of the servo drive system along the programmed
path. After a specific time the mechanical brakes are activated
ensuring a safe stop.
The stopping process is in accordance with a class 1 stop. The
maximum applicable torque on the most loaded axis determines the
stopping distance.
In case of a failure of the drive system or a power interruption, a
class 0 stop turns out. Emergency Stop (ES) is a class 0 stop. All
stops (GS, AS, SS and ES) are reconfigurable.
While programming the robot in manual mode, the enabling device
has a class 0 stop.
Summary of Contents for IRB 6620
Page 1: ...Product specification Articulated robot IRB 6620 150 2 2 M2004...
Page 2: ......
Page 3: ...Product specification Articulated robot 3HAC025861 001 Rev E IRB 6620 150 2 2 M2004...
Page 116: ...2 DressPack and SpotPack 2 9 1 Options 114 Rev E 3HAC 025861 001...
Page 132: ...3 Specification of Variants and Options 3 1 14 Documentation 130 Rev E 3HAC 025861 001...
Page 134: ...4 Accessories 132 Rev E 3HAC 025861 001...
Page 137: ......