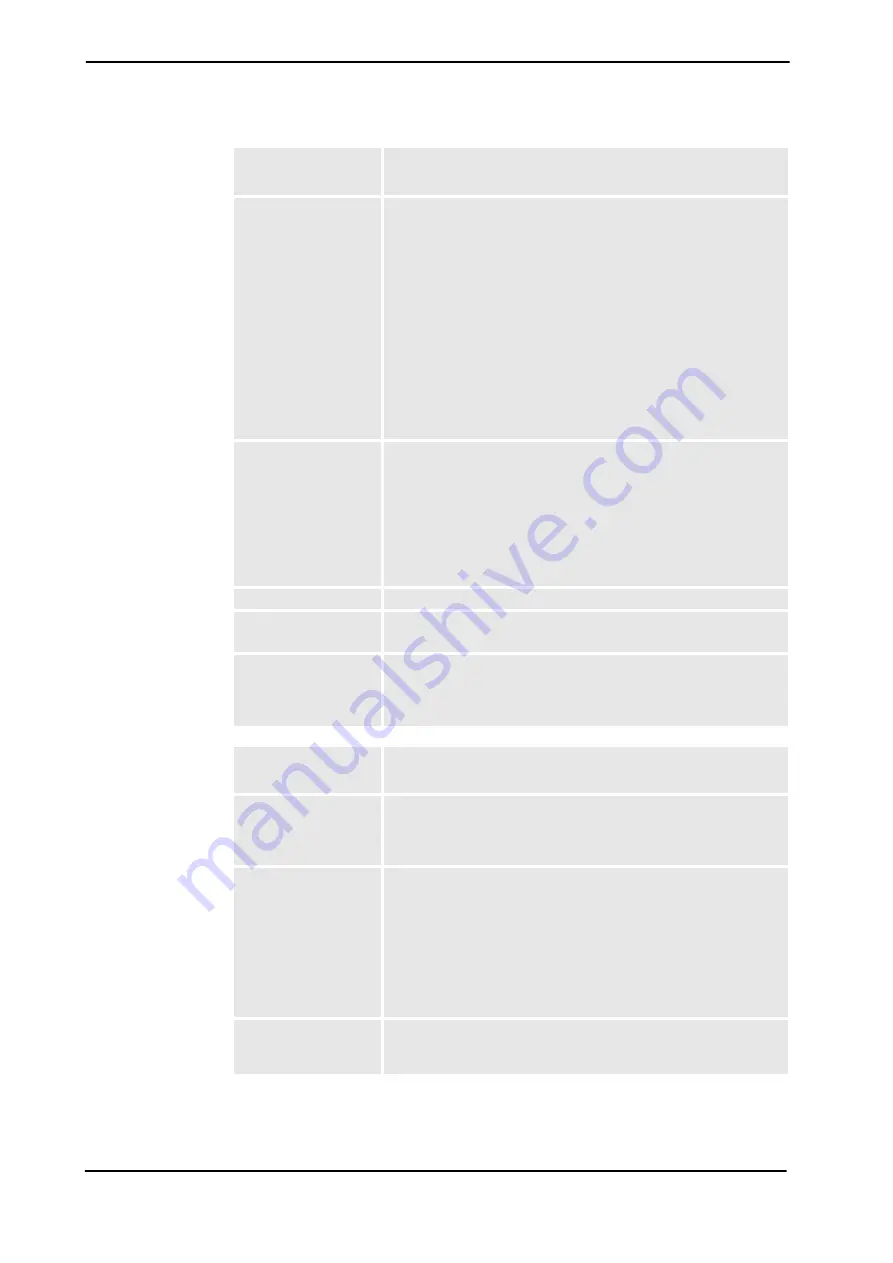
1 Description
1.2.1 Standards
12
Rev.E
3HAC 025861-001
The Self Tuning
Performance (STP)
The Process Robot Generation is designed to run at different load
configurations, many of which occur within the same program and
cycle.
The robot’s installed electrical power can thus be exploited to lift
heavy loads, create a high axis force or accelerate quickly without
changing the configuration of the robot.
Consequently the robot can run in a “power mode” or a “speed
mode” which can be measured in the respective cycle time of one
and the same program but with different tool loads. This feature is
based on QuickMove
TM
.
The respective change in cycle time can be measured by running
the robot in NoMotionExecution with different loads or with
simulation tools like RobotStudio.
The Electronically
Stabilised Path (ESP)
The load and inertia of the tool have a significant effect on the path
performance of a robot. The Process Robot Generation is equipped
with a system to electronically stabilize the robot’s path in order to
achieve the best path performance.
This has an influence while accelerating and braking and
consequently stabilizes the path during all motion operations with a
compromise of the best cycle time. This feature is secured through
TrueMove
TM
.
Over-speed protection
The speed of the robot is monitored by two independent computers.
Restricting the working
space
The movement of each axis can be restricted using software limits.
Axes 1 and 3 can also be restricted by means of mechanical stops.
Collision detection
(option)
In case of an unexpected mechanical disturbance, such as a
collision, electrode sticking, etc., the robot will detect the collision,
stop on the path and slightly back off from its stop position,
releasing tension in the tool.
The Passive Safety
System
Description
General
The Process Robot Generation has a dedicated passive safety
system that by hardware construction and dedicated solutions is
designed to avoid collisions with surrounding equipment. It
integrates the robot system into the surrounding equipment safely.
Compact robot arm
design
The shape of the lower and upper arm system is compact, avoiding
interference into the working envelope of the robot.
The lower arm is shaped inward, giving more space under the upper
arm to re-orientate large parts and leaving more working space
while reaching over equipment in front of the robot.
The rear side of the upper arm is compact, with no components
projecting over the edge of the robot base even when the robot is
moved into the home position.
Moveable mechanical
limitation of main axes
(option)
Axes 1 and 3 can be equipped with moveable mechanical stops,
limiting the working range of every axis individually. The mechanical
stops are designed to withstand a collision even under full load.
The Active Safety
System
Description
Summary of Contents for IRB 6620
Page 1: ...Product specification Articulated robot IRB 6620 150 2 2 M2004...
Page 2: ......
Page 3: ...Product specification Articulated robot 3HAC025861 001 Rev E IRB 6620 150 2 2 M2004...
Page 116: ...2 DressPack and SpotPack 2 9 1 Options 114 Rev E 3HAC 025861 001...
Page 132: ...3 Specification of Variants and Options 3 1 14 Documentation 130 Rev E 3HAC 025861 001...
Page 134: ...4 Accessories 132 Rev E 3HAC 025861 001...
Page 137: ......